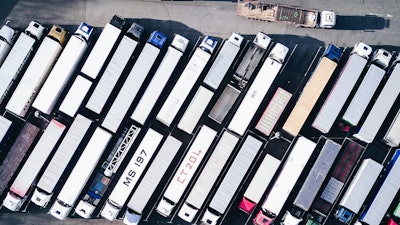
It’s no secret that the supply chain has experienced some major disruptions over the last few years. Logistics companies serving the food sector have been faced with a variety of challenges stemming from the pandemic, and even though it seems like the world is slowly inching back to normal, many of these challenges are likely to persist well into the foreseeable future.
One of the most pressing challenges seems to be persisting capacity pressures. Although some facets of this problem are outside of our control, understanding where the problem is coming from is the first step in creating solutions. From labor and reefer truck shortages to surging demand, logistics companies are tasked with overcoming a number of barriers in order to solve the looming capacity crisis.
Labor shortages
Similarly to other industries, labor shortages have hit logistics companies hard. But the problems faced by logistics providers are compounded by an issue that has plagued the industry for as long as many can remember — high turnover rates. Staffing challenges in the logistics industry have existed long before the onset of the pandemic. Truck drivers have a notoriously difficult profession, and this has led to one of the highest employee turnover rates of any industry. According to American Trucking Associations, the turnover rate at large fleets averaged 89% in March 2021. Naturally, the Coronavirus disease (COVID-19) has exacerbated stress placed on drivers making staff retention even more difficult over the past few years. According to an article published by CBS News, an average of 300,000 truck drivers leave the profession each year, and with training and apprenticeship programs operating at reduced capacity since the onset of the pandemic, labor shortages may persist for a while.
Particularly for logistics companies that serve the food and beverage industry, staffing issues can lead to major crises. Unlike with many other consumer goods, food products are often perishable, putting greater pressure on companies to fulfill deliveries on time. Untimely food product deliveries can create a shockwave leading to unstocked grocery shelves, disrupted restaurant operations, and a whole host of other problems.
In order to combat the labor shortage, employers should focus on doing the best they can to retain existing employees, as recruitment can be costly and frustrating. Providing fair wages, adequate vacation time, and competitive benefits are just a few ways that companies can increase employee retention rates. Remember, the world has changed, so employers need to adapt to meet the evolving needs of their employees. Taking some time to step back and listen to people’s needs can go a long way in boosting morale and reducing turnover.
Reefer shortages
Labor isn’t the only input in short supply. Reefer shortages have made shipping perishable products in a timely manner extremely difficult. The shortage has been exacerbated by shipping lines that have started to carry general cargo in unplugged reefers to meet the short supply of dry containers, making the problem even more dire for food shipping companies. Furthermore, congestion at ports and vessel delays have also contributed to the problem.
A temporary fix for logistics companies shipping perishable goods is to use air freight in place of ground or sea transportation, but this is not a long-term solution. Although this approach might put a band-aid on the problem for some shipping lines, air freight is the most expensive mode of shipping and will likely erode profits on low-value goods.
An alternative solution that has proven successful in our company has been using box trucks for time-sensitive deliveries. Many people in the industry associate full truckloads only with 53-foot containers and overlook the capabilities of 26-foot box trucks. Thinking outside the normal go-to solution and using box trucks to handle time-sensitive overflow has proven to be an effective tactic in meeting deadlines for several large clients.
Surges in demand
Last but not least, logistics companies are struggling to meet increased demand. It may seem counterintuitive that increased demand for food products presents a problem, but when combined with shortages in labor and other inputs, a major issue arises. Coming out of the pandemic, many restaurants and other food businesses are seeing a surge. This has created a “bullwhip effect”. For example, imagine a restaurant sees a 15% demand increase for steaks. Anticipating a further increase in demand, the restaurant inflates its orders with suppliers not by 15%, but by 20% to meet predicted growth, and those suppliers thereby inflate their orders to meet the increased demand and so on. Although these changes may seem small, they compound and create a massive ripple effect throughout the economy.
Right now, there is no easy solution for meeting increased demand, especially given the concurrent labor and reefer shortages. It’s important for food retailers to try their best not to over-order products, as doing so will continue to create ripple effects in the supply chain. Through maintaining an open dialogue, retailers, supplies and logistics providers can work together to reduce unnecessary pressure placed on the supply chain and help things slowly return to normal.