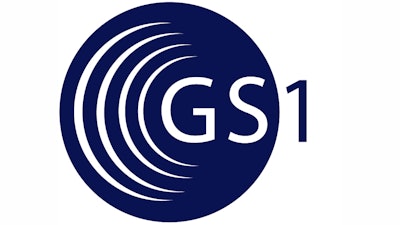
Foodservice distributors and manufacturers are working to improve data management in order to reduce cost and meet various government regulations for food safety and enhanced traceability. They are also finding that their foodservice operator customers, who face similar requirements, are requesting new data standards from distributors and suppliers. To assist with this effort, the Foodservice GS1 US Standards Initiative is a voluntary, collaborative industry effort seeking to establish a global language of business, introducing standards to help businesses identify, capture and share information.
Attendees at the recent International Foodservice Distributors Association (IFDA) distribution solutions conference at the Indiana Convention Center in Indianapolis got an update on how Independent Purchasing Cooperative (IPC) has identified efficiencies by implementing GS1 data synchronization throughout their system. IPC has required its foodservice suppliers and distributors to adopt Foodservice GS1 standards, a system IPC claims has already improved efficiency and shown opportunities for significant cost avoidance by enabling improved item information.
Rick Buttner, director of quality and supply chain risk, and Lucelena Angarita, quality/GS1 program manager of IPC, presented “GS1 GDSN Data Synchronization: Speaking One Language Throughout the Supply Chain.” IPC, a SUBWAY franchisee-owned purchasing cooperative for more than 30,000 SUBWAY restaurants, negotiates the lowest costs for goods and services while improving quality for their franchisees in the U.S., Canada, Virgin Islands and Puerto Rico.
“GS1 is a company we all use every day and don’t know it,” said Buttner, whose company has been involved with GS1 shortly after the Foodservice GS1 U.S. Standards Initiative began in 2009. The GS1 initiative encompasses a wide variety of industries, supporting 5 billion UPC scans every day. The foodservice initiative marks an attempt to drive the adoption and implementation of GS1 standards in the foodservice supply chain to: 1) optimize supply chain efficiency; 2) enhance food safety; and 3) improve product information.
Buttner said one of the most significant results of GS1 standards for his company has been using a uniform language for products, locations and transactions.
He noted that when IPC joined the GS1 initiative in 2010, they were hoping to improve product traceability. The company wanted a vehicle to improve traceability and reduce time to compile information for product withdrawals and recalls. The Food Safety Modernization Act (FSMA) requires the company to have a plan to enhance tracking and tracing of food. In addition, produce suppliers had introduced the Produce Traceability Initiative (PTI), which also enabled a way for IPC to improve product traceability.
IPC’s produce suppliers put them in touch with GS1. Since incorporating the GS1 standards into its operations, “enhanced product traceability will be the end result of following the standards,” Buttner said.
The IFDA, meanwhile, has encouraged foodservice manufacturers to adopt GS1 standards and in December of 2013 noted that 83 percent of foodservice manufacturer sales volume and 65 percent of distributor sales volume was committed to adopting and implementing GS1 standards.
Prior to adopting GS1 standards, IPC’s supply chain had three different product numbering systems, Buttner said. “We had to start with data synchronization,” he said. The company wanted to synchronize product data around unique identifiers and defined standard attributes.
To get GS1 standards approved by IPC leadership and implemented throughout their supply chain, Buttner hired Angarita two years ago.
Following Buttner’s remarks, Angarita took the podium and explained the company’s data synchronization effort in more detail.
Angarita said in order for their leadership team to approve GS1 implementation, their first objective was to determine tangible benefits from data synchronization. She said IPC used Six Sigma, a system that seeks to improve the quality of process outputs by identifying and removing the causes of defects (errors) and minimizing variability in manufacturing and business processes. “Companies need to allocate specific resources to this project in order to reap the true benefits,” she said.
IPC recognized that its product information did not follow an automated standard identification process, causing inaccuracies and delays in the supply chain.
The first step was to define the problem and identify why there were discrepancies in the product data. The second step was to measure and determine the unnecessary costs that the data discrepancies were adding to their system. The third step was to analyze root causes of this problem and establish solutions to automate and streamline product data management using GS1 standards. The final step was to control and monitor product data accuracy as well as measure the ongoing benefits.
The company has assigned a unique GS1 Global Trade Item Number (GTIN) for SUBWAY branded products and is requiring their trading partners to use this number in all business transactions. Using this unique identifier, product data can be synchronized through GS1’s Global Data Synchronization Network (GDSN). IPC became the “gatekeeper” for Subway labeled item information.
“Once we started synchronizing product information, we worked with logistics and identified discrepancies for 83 high volume products. Working on truckload optimization and material handling costs with the correct data yielded significant cost avoidance,” Angarita said.
Prior to implementing the full GDSN project, a pilot done with 27 high-volume items revealed IPC’s system and GDSN had 74 percent of items with one or more core discrepancies, such as dimensions or weights. In addition, there were core discrepancies between IPC and various distributors’ systems on 82 percent of IPC’s total active product catalog.
IPC is holding suppliers accountable for data completeness and accuracy. They have asked for select distributors to help provide feedback to suppliers by physically validating data published via the GDSN with a CubiScan and report back any discrepancies.
Angarita said the company found that there was less time needed to find and fix item data discrepancies by using GDSN as the source of truth. Manually entering item information and finding and fixing discrepancies in data was costing the company 26 percent of a full-time equivalent. Data mapping was costing 65 percent of a full-time equivalent plus additional software vendor cost.
By sharing and receiving data through GDSN, IPC and its trading partners were able to fix the discrepancies in less time. Under the old system, it took 15 to 30 business days to fix one product discrepancy via email or other forms of communication. By using the GDSN, all discrepancies were resolved in half a day to five business days.
“Once the traceability GS1 standards are in place, we will be able to trace product to the restaurant level,” Angarita said. In addition, there will be fewer operational disruptions at restaurants, less discarded good product, and potentially fewer product “outages,” resulting in lost sales.
IPC has set GS1 data synchronization and traceability adoption goals and compliance dates for its product manufacturers and distributors. IPC has asked distributors to prepare internal systems to receive and integrate product data via GDSN. Both distributors and suppliers are required to use 14-digit GTINs in all business transactions for IPC. Suppliers are required to ensure product attributes are within “tolerances” defined by GS1’s data quality group while distributors are being asked to monitor data accuracy by physically validating product and reporting discrepancies. After data synchronization is completed, they hope to be sharing at a future IFDA distribution solutions conference how their system is starting to meet the traceability objectives as well.
“With our trading partners’ help, we will be able to consistently make sure that this data is accurate,” Angarita said.
Elliot Maras is managing editor of Food Logistics.