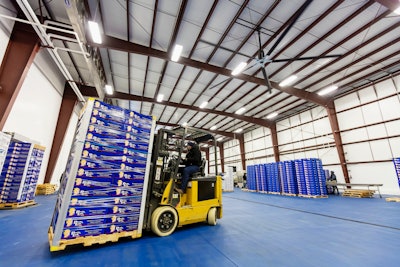
After some of the world’s finest California table grapes are carefully hand-picked for color and rigorously tested for just the right sugar content, one of their worst enemies is unwanted moisture.
If unwanted moisture occurs prior to or during the grape packing process, or even during shipment, that can lead to mold growth well before the perishable product arrives at its destination. The result is unsellable product which then means additional costs for everyone in the supply chain.
That’s why grape grower, packer and shipper Jakov P. Dulcich & Sons invested in four industrial high-volume low speed (HVLS) fans from EPIC Fans as integral components of its 16,000-square-foot California table grape packing facility in Delano, Calif. Among several benefits, the fans work hard to ensure that the company’s grapes remain free of unwanted moisture, especially during the critical packing process prior to shipment.
Unwanted moisture induces mold growth
Jakov P. Dulcich & Sons markets 15 different varieties of red, green and black seedless table grapes grown on 6,000 acres of vineyards. Harvesting normally occurs between July and mid-November when the operation ships approximately 60,000 boxes worldwide each day from a multimillion-dollar, state-of-the-art storage and distribution center. The facility includes a packing line operation, receiving area as well as 150,000 square feet of cold storage.
"Toting fruit in from the field and packing the product inside is a fairly new concept for us," said Jacob McCaa, General Manager, Jakov P. Dulcich & Sons.
The inside packing area also helps to ensure that company's table grapes are consistently packed at the correct weights so customers receive what they are expecting to receive. Packing the grapes inside also protects the product from the rain.
“We definitely can’t pack wet grapes,” McCaa stressed. “That’s because wet grapes will induce mold growth, so we carefully check for unwanted moisture in the storage boxes even before they’re sent to cold storage to await packing.”
Jakov P. Dulcich & Sons keeps its packing room at an even 52°F. When the grapes are removed from cold storage, that ensures they won’t sweat which could cause unwanted moisture issues in the product’s packing.
HVLS fans play vital role in product quality control
Vital to Jakov P. Dulcich & Sons’ quality, moisture and temperature control efforts are two 24-foot HVLS fans located above the 16,000-square-foot packing line area.
“We originally planned to invest in two industrial fans for the packing room for airflow and moisture control,” McCaa adds. “We knew that the increased airflow would help to keep the grapes dry, especially if they came into the receiving area wet.”
In addition, Jakov P. Dulcich & Sons was focused on reducing the amount of expensive energy consumption that is required to the keep the packing line area at just the right temperature.
“We’re anticipating that the industrial fans will help reduce our air conditioning costs for the 16,000-square foot packing line area, which can get quite expensive,” McCaa said. “Our HVAC system is also somewhat loud, and we don’t want to run it non-stop. The fans really help with the overall airflow and keeping the room at a consistent temperature.”
Increased comfort for forklift drivers
In the company’s receiving area, Jakov P. Dulcich & Sons’ forklift drivers are benefitting from two 12-foot diameter HVLS fans. The fans keep the drivers more comfortable while they wait for the table grapes to arrive in totes on pallets from the field.
The company’s covered, but open-air receiving area, is especially uncomfortable for forklift drivers during the harvest season’s hottest months. That’s because they wear heavy jackets while transporting harvested table grapes between the receiving area and the operation’s cold storage which is kept at 32°F. One trip between the receiving area and cold storage can mean a drop of 60°F or more.
The receiving area’s fans also provide needed airflow for the pallets of grapes that are stored short-term in the receiving area prior to chilling.
Easy fan control with maximum benefits
All four of Jakov P. Dulcich & Sons’ HVLS fans feature black blades with silver hubs, struts and motor cover.
“We’ve found that operating the fans is very easy using a touch keypad,” McCaa shared. “Overall, the fans are a real blessing for our forklift drivers. They were pleasantly surprised to experience how much more comfortable the receiving area environment is now when they arrive there from cold storage. They no longer sweat during hot weather while waiting for another pallet of grapes to arrive from the field.”
McCaa concluded, “Based on our experience, we highly recommend industrial HVLS fans for any packing facility in the ag industry with a commodity that requires moisture control, coolness and sufficient airflow.”