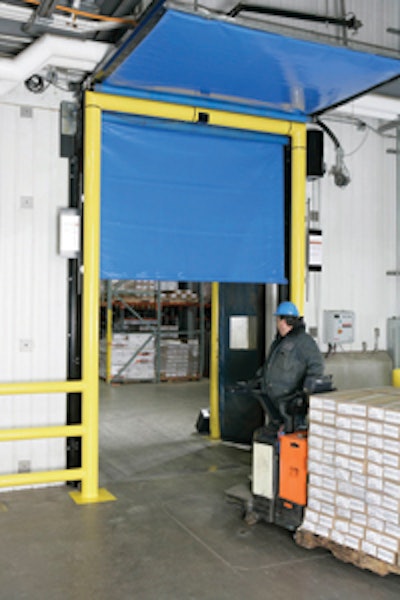
The U.S. Labor Department re-leased data showing that energy prices jumped 5.4 percent this past May, from the previous month. There's no doubt that it's becoming more and more expensive to maintain the environments in today's food and beverage warehouses-especially with freezers, where problems with a door's seals can leech thousands of dollars a year in wasted energy.
It's vital that companies be aware of the latest trends in facility door uses and the cost, as well as productivity savings, they can obtain by using the right door for the right application. However, there are a vast array of door products on the market, ranging from fabric doors to steel doors to plastic curtains to folding doors and even air doors.
These products can be manual or activated by a pull cord or automatically activated by a sensor eye. With all the different types of doors out there, how does a facility manager decide which products are best for his warehouse?
"To me, doors are like a tool kit," says Dwight Clark, vice president, sales marketing for Jamison Door Co., in Hagerstown, MD. "I just have to figure out what a customer is trying to do and match them up with the right technology."
Dock Doors
"When it comes to dock doors, you've got three things to look for-first, something that will block the opening. Next, something that is low-priced and finally something that has a higher ‘R' value (the measure of a door's level of insulation)," says Clark.
"Most people use typical sectional doors like your garage doors at home," notes Jon Schumacher, director of marketing for Rite Hite Corp. of Milwaukee.
Josh Brown, national sales manager for TKO Dock Doors, a division of 4Front Engineered Solutions Inc., agrees. "In warehouse applications, they're putting doors on that you would put on your garage."
He suggests warehouses might want to look into options for these doors that include wider tracks and bigger rollers, as these are much stronger than standard rollers. In addition, instead of using springs to lift and balance out a door, facility managers may want to opt for counterweight systems. This way, they don't have to be concerned about door springs rusting or even potentially breaking. Switching may also save money in terms of maintenance.
Rite Hite has developed a dock door with only one moving part on it.
"Basically it turns a shaft and makes the curtain go up-and-down," says Schumacher. "We've taken a lot of the maintenance out of it."
When choosing a dock door, check the available space above its doorway.
"If you have any space limitations, such as duct work in the ceiling, where you can't bring the door up into the horizontal position, you would want a rolling steel door that coils up on itself, over a barrel," notes Karen Cohen, product manager, commercial doors and operations, for Overhead Door Corp., Lewisville, TX.
Other things to look for in a dock door are how thick the door is in terms of insulation value and how well it seals.
"We are actually seeing more demand for high R value products, particularly in the ice cream business, or when you have a cold dock," notes Jamison's Clark. "It's going to benefit you from an energy standpoint, plus you can maintain your temperatures. Wherever people are really concerned about maintaining temperatures on their dock, their only solution is a higher R value product like an R28-30, which is a 4-inch thick product."
"For cold storage, the better a door seals, the more savings you'll get on cost of ownership," says TKO's Brown. "This is because you're going to be able to recoup some of the upfront cost of the door over time, due to energy savings."
Brown also notes that food and beverage facilities are subject to quality inspections of their warehouses, which entail officials examining dock doors for potential gaps that would allow insects and air to infiltrate the premises. "They'll get written up for that and fined," he explains. His company's products can help eliminate door gaps from occurring because they have a unique seal which is attached to the door itself that closes off a door's perimeter. When the door goes up, the seal goes with it. "A standard door is going to have a rubber seal attached to the door jams or the sides of the opening that will seal off the gap."
Check For Durability
In addition, warehouse facilitators should keep door durability in mind.
"In every warehouse the door is going to get hit at some point. It just depends on how abusive your situation is. Look for a dock door that has some kind of impactability to it," notes Rite Hite's Schumacher.
According to the experts, impactable dock doors may cost anywhere from $900 to $3,000 dollars. To determine what kind of impactable door is required, a company needs to estimate the level of damage a door will sustain over the period of a year. These doors prevent damage to themselves through a number of means. In some cases, when a forklift strikes a door, a few of the panels will breakaway. Other doors breakaway in their entirety when hit. Some doors only flex when struck and then bounce back into position.
Overhead Doors' Knock and Lock product features two impact resistant sections on the bottom of an insulated door. When struck, these sections swing outward and automatically swing back in place, thanks to a bungee cord that runs through the panel.
"We estimate that 90 percent of damage to dock doors is on the bottom two sections," says Overhead's Cohen.
TKO Doors offers its Knock Out door, which knocks to the outside when struck by a forklift.
"You just pull it back into the tracks," explains Brown. "You eliminate the damage you have so that you don't have to call in for emergency service."
Rite Hite has an impactable door that features True Auto Re-Feed. Should the door get hit as it's opening, it re-aligns itself on the way up.
There are a number of advantages to using an impactable dock door-the main one being productivity. If a warehouse suffers the loss of a door due to collision, they can no longer use it to load and unload trailers. Loss of productivity means loss of income, as well as warehousing personnel that are standing around doing nothing and getting paid for it.
Another advantage is the savings in maintenance costs. The experts estimate that the cost to repair the bottom panel of a standard sectional door can run anywhere from $400 to $600, whereas many impactable doors cost only about $400 more than a sectional door.
"This means they pay for themselves in two-to-five years," says TKO's Brown. "If you have to replace a panel twice every year on that standard door, it's about $800 a year."
Freezer Doors
Freezer doors are another subject entirely. Not only must they be able to take a hit, they must also be able to withstand temperatures in the neighborhood of zero degrees Fahrenheit. The current trend is the use of high speed roll up doors, which are composed of thin fabric.
These doors have no R value and in order to prevent ice from building up on the freezer side, warehouses have to keep heat lamps on them that use anywhere from 15 to 30 kilowatts of energy. In addition, the heat generated by them must also be removed.
"Keeping the ice off your door can cost you anywhere from $10,000 to $20,000 a year per door opening," notes Rite Hite's Schumacher. "We manufacture a roll up door with an insulated panel, which doesn't require heat lamps. A lot of our customers are getting rebates from energy companies because they're saving so much money."
Schumacher's company also offers insulated bi-parting doors. These types of doors open faster than rolling doors. On a typical eight by 14 freezer door, the rolling door has to go up 14 feet while the biparting door only has to open eight. Schumacher says that if a warehouse freezer has the room in its opening to allow a door's panels to slide to the side, it's a better option.
"The biggest cost in a freezer door is really when it's open and you let all that heat in and then have to remove it," notes Schumacher. "So the faster you can get your door open and then close it, the more money you're going to save."
Another factor to keep in mind is how well a freezer door seals.
"If you have a door that doesn't seal well, you're going to get ice building up wherever the seal is bad," warns Schumacher. "It's lost energy."
This is why faster moving doors can be critical in a freezer situation. The faster they move the less chance they stand of being hit by a moving forklift and having their seals compromised.
Air Doors
This brings us to re-circulatory air doors, which aren't doors at all. Instead, blowers blast air across the opening of a freezer or cooler doorway, which stops refrigeration loss as well as moisture migration. The air is sucked in on the other side of the door by an intake device, which recirculates the air.
"One of the big advantages is frost elimination," says Jamisons' Clark. "You're not running all the defrost cycles on your refrigeration systems, which is where your big expense is, because you don't have all this ice forming on your coils."
Air doors present a number of other benefits. Safety-wise, there is the prevention of ice formations on the floor, walls and ceiling, which is a problem in freezers where a great deal of moisture is present. Additionally, air doors provide complete visibility, which cuts down on collisions. There is also a productivity gain-workers don't have to wait for doors to open and are able to move product faster.
However, air doors are expensive and need to be justified from an energy savings standpoint. The initial investment is only offset if a warehouse has a lot of pass-throughs in its cooler or freezer, which translates to high open door times.
"With high open door rates, you have all the effects of not having a door there at all," Clark says. These effects include loss of treated air, influx of moisture and higher energy costs. "The busier you are, the more a traditional door works against you."
Before settling on a door, vendors suggest warehouse managers do their research-they should take a look at what their doing currently in terms of door designs and whether or not it's working. They should also review how many pass-throughs each door is getting, as well as the amount of damage they are subject to. Then they need to consider what it is they wish to achieve with each door.