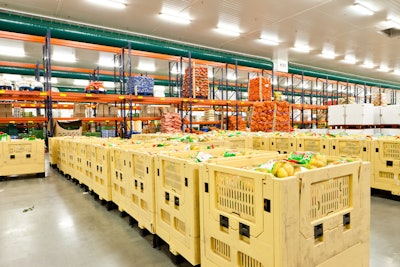
High-volume buying periods are a crucial time for food safety practice as consumer demand increases in grocery stores, putting additional pressure on grocers to ensure they are providing safe and quality products. To maintain effective food safety practices during surge periods, grocers must implement processes supported by solution-based technologies that optimize food safety operations and equipment performance.
Ensuring on-shelf availability
During high-volume periods, inventory enablement and on-shelf availability are especially critical for grocers and food retailers. Operators are responsible for managing fluctuations in demand, maintaining safety stock based on focus areas, and ensuring accuracy throughout promotions.
Most of the calendar year operates at “baseline focus accuracy” while promotion periods, special sporting and cultural events, and certain holidays bring “lift focus accuracy” requirements. In these cases, the margin for error in ensuring on-shelf availability for certain inventory items becomes wider as special deals or event-related favorites influence supply and demand and threaten out-of-stocks. If one particular brand is preferred over another during such a time, it’s important to focus on the aggregate movement of inventory at the category level rather than the individual brand, calculating any cannibalization between brands or private label options.
Maintaining quality and condition
Even more critical to seamless grocery operations during high volume periods is the condition of inventory available on the shelves for purchase. For example, if past-expiration-date yogurt is sold, the consumer will lose trust in the grocery upon discovering the out of code product. They may even choose to never shop at the offending food retailer again. If they notice a past-expiration product while they are shopping, they’ll lose confidence as they finish their shopping, shrinking their cart and reducing total basket. As grocers have long known, food is a very personal and essential part of the consumer’s life. The safety and quality of the food they buy for themselves is of the utmost importance. Monitoring the condition of on-shelf inventory is crucial to safeguard the trust of consumers, especially when making a brand-switch is relatively easy in a competitive market.
In addition to expiration dates, the on-shelf appearance of product, especially produce, greatly affects consumer behavior. If you have 150 pounds of bananas as on-hand inventory, but they are brown bananas, how many pounds of bananas do you really have? The answer, of course, is zero. If no consumer will select them off the shelf, the inventory essentially doesn’t count.
Proper rotation of produce is a key in-store operation for inventory maximization. Having established Standard Operating Procedures (SOPs) and intelligent formulas for time-based task management in place is helpful for ensuring that staff rotate fruits and vegetables in a revenue-maximizing manner.
Consider this example. The ripeness of strawberries deteriorates in real-time, potentially in front of the shopper’s eyes. Real-time prescriptive workflows informed by Internet of Things (IoT)-sensing capabilities enable grocery store employees to act before the produce goes bad. If there are ripe strawberries waiting in the backroom and strawberries going bad on the shelf, every minute that the situation hasn’t been remedied is lost time contributing to cart waste/shrink. Managing ripeness of ethylene-sensitive produce to “awaken” the ripening process at the optimal time is another proactive way to maximize inventory availability. Mitigating waste and loss for non-produce inventory can also be achieved by developing a food donation program that maximizes freshness for consumers and supports the community at the same time.
IoT connectivity empowering end-to-end visibility
Successful food retailing is a complex operation that starts long before product arrives at the store — from the field or slaughterhouse to the processing plant, warehouse, in-transit truck, and point of sale, all the way to the point of consumption. A pivotal point in this process, especially for meat products, is the hand-off of product from the truck to the back room of the food retailer. Temperature-sensitive foods deteriorate quickly if they are not transferred into refrigerated areas in adequate time after being dropped off from the truck.
IoT-enabled task management systems are making this transfer of high-value assets more secure by providing retail employees with prescriptive workflows. For example, the system might send a message by voice or text that communicates, “Hey, the truck with the shipment of beef and chicken products is arriving in 20 minutes. Go to the back room and prepare to receive the shipment. The temperature of the product remained within the proper range during transit.” Highly detailed prescriptions like this example are made possible by advanced analytics and IoT networks that collect and integrate data from disparate systems, creating workflows informed by intelligence gathered along every point along the supply chain.
These innovative approaches to leveraging the power of IoT automation include telemetry collection of numerous types of data, including location, weather conditions, temperature, humidity, velocity, transactions, logistics patterns, and consumer demand. Equipped with intelligence and digital decisioning from IoT visibility, retailer leaders are able to allocate demand appropriately — as available-to-promise, capable-to-promise, or fresh-to-promise — during fluctuations in demand.
End-to-end operational visibility is a must for the modern grocer and food retailer. Shifting consumer demand during high-volume periods requires sophisticated and intelligent systems that empower real-time operational decisions that maximize on-shelf-availability and inventory quality while minimizing shrink and loss.