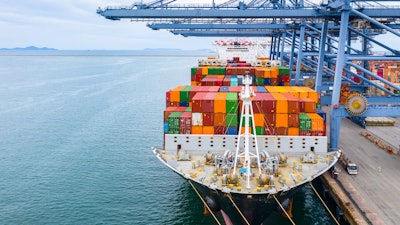
Even before the pandemic, cracks in the global supply chain were showing. When U.S. and China trade relations became strained, so did the supply chain. The pandemic, of course, only made matters worse and has continued to weaken the supply chain. Shutdowns of major ports coupled with heavy congestion at other ports, critical part shortage and increasing e-commerce demands are just some of the challenges facing today’s supply chain. It is not surprising therefore that a Gartner survey revealed the growing focus on supply chain resiliency. It found that 21% of the surveyed supply chain leaders believed their networks were now highly resilient with another 55% striving to become more resilient over the next three years.
For those companies that have gained supply chain resiliency and others taking steps in that direction, advanced technologies will play a central role. It is important to understand how optimization software encompassing technologies like artificial intelligence (AI), machine learning, advanced algorithms and predictive analytics are advancing various supply chain operations, from demand, network and spare parts planning to inventory optimization and management.
The main challenges
There is a lot of room for improvement across the supply chain, but many of the challenges stem from these primary shortcomings. They are a lack of real-time, actionable data and supply chain visibility, as well as reliance on old strategies and systems such as just-in-time inventory management, lean manufacturing, Excel spreadsheets and single-sourcing strategies. These deficiencies are contributing to a wide range of supply chain bottlenecks.
The industry is experiencing increased warehousing space shortages, overcrowded rail yards, ships anchored off the West Coast ports awaiting unloading and overall container shortages. Manufacturers are slowing down or shutting down production lines due to severe part shortages.
In addition to losses sustained as a result of supply chain challenges, there are the costs to be incurred to develop more resilient operations, which in itself, introduces another challenge. The Gartner survey found that 58% of supply chain leaders believe that achieving resiliency results in increased costs for structural changes in sourcing, manufacturing or distribution models. In addition to increased costs, there are potential risks, including those associated with heightened customer expectations and inventory obsolescence, among others. Companies best able to pivot and achieve resiliency with minimal risk are generally those that already have strong market positions, higher profit margins, commodity vs. specialty product lines and can withstand new market or regulatory pressures. They will also be the organizations that take steps toward digital transformation to achieve more agile, connected and autonomous supply chain ecosystems leveraging advanced optimization technologies and initiatives.
Leveraging advanced technologies
Demand planning. One of the most important benefits optimization software delivers is real-time data and supply chain visibility. Through greater transparency, organizations on the supply chain can make better decisions, which in turn, enable them to optimize their resource utilization, improve productivity and enhance customer service. For example, many manufacturers have good insight into their Tier 1 suppliers, but beyond that, they lack knowledge of what Tier 2 and 3 suppliers their Tier 1 suppliers rely on. This can pose a real problem in demand planning, manufacturing and inventory management; a problem further exacerbated by volatile market conditions and shorter product lifecycles. Applying a demand planning solution, manufacturers can plan by product categories, regions and customers, conduct “what if” simulations to unveil alternative strategies when needed and even analyze how various sales promotions or seasonality affects demand planning. By leveraging advanced optimization software, companies achieve better transparency. This vastly improves the quality of their demand planning, product availability and service levels, while streamlining the planning process, facilitating lower inventory levels and freeing up capital.
Inventory optimization. Staying ahead of demand by optimizing inventory requires an ongoing balancing act. This can only be achieved with digitalization that supports and integrates optimal forecasting and planning with real-time data. As a result, a company can improve its procurement based on market conditions and real-time knowledge of stock levels. Intelligent software, incorporating intuitive workflow functionality, provides self-adapting forecasts based on market trends, seasonal impacts and unexpected demands. Its management by exception feature provides inventory planners with information that enables them to address high-priority tasks first and avoid negative situations such as running out of a certain stock item. Just as with demand planning, software targeting inventory optimization provides full transparency of inventory planning processes, which reduces planning efforts by 25-50%, inventory levels by up to 40% and procurement costs, while concurrently, increasing product availability.
Spare parts planning. Managing both predictable and unpredictable spare part requirements is vastly improved with forecasting capabilities driven by smart algorithms and operations research that provide full transparency to enable informed spare parts planning and logistics. These algorithms provide details regarding future demand and make dynamic adjustments to stock levels to ensure that an ample supply of spare parts stock is in line with production needs and product life cycles. The technology automates various processes including order approvals for parts forecasted to have high demand and synchronization of demand planning. This enables a company to achieve a delivery capacity approaching 100%, while reducing procurement and inbound logistics costs.
Digital transformation and the future of the global supply chain
When planning of these aforementioned processes and others is fully-integrated the greatest gains across the supply chain can be achieved. Through digital transformation, an optimized internal supply chain, from purchasing to manufacturing, distribution and sales can be realized. Improved planning of budgets, demand, distribution, production planning and procurement can be achieved. Internal supply chain improvements also benefit the global supply chain as individual companies become more resilient through heightened supply chain visibility, greater agility and optimized asset and workforce management. It will not happen overnight. It will take years, but over time, more companies will shed risky strategies like single-sourcing, traditional inventory controls and reliance on less than real-time supply chain data.
Boards of directors and investors place greater demands on company management to deploy digital solutions that improve supply chain resiliency. There will also be a broader rollout of supply chain as a service (SCaaS) as more companies look to further improve their service levels. The trend toward digital transformation of supply chain processes will pay off in improved customer service levels, increased sustainability and competitiveness. The investments made in advanced digitalization technologies will be returned in what PricewaterhouseCoopers (PwC) has estimated to be a payback period of approximately 1.8 years.
The road to supply chain digital transformation
As with any major initiative, embarking on supply chain digital transformation demands careful consideration of several criteria -- corporate culture, workforce management and related skill sets, infrastructure and goals tied to these important initiatives. A strategic plan should be developed and led by an internal team with representation from all areas of supply chain operations and across all levels of the organization. The company’s corporate/general counsel and finance functions should also be involved to impart their knowledge and advice pertaining to potential financial, tax, regulatory/compliance and risk matters, including cyber risks and the need for a digital twin to detect inherent risks. The plan should make a strong case for why digital transformation is essential and clearly convey the benefits to be derived.
Once a plan has been established, selection of a supply chain solution provider can commence. It is important that any third-party vendor(s) chosen be well-vetted and screened for experience in global supply chain processes. Vendors should be able to cite references of companies they have supported with advanced technologies and working towards digital transformation. Ongoing monitoring of the project’s implementation is critical to ensure goals are met and within the scheduled timeframes.
Closing remarks
Gartner reported that over 50% of organization have not started actively building a “roadmap for supply chain digital transformation.” For the global supply chain to become more resilient and able to withstand disruptions such as a global pandemic, natural disasters, geo-political turbulence and man-made errors, it will be important that digital transformation happen on a wide scale basis.