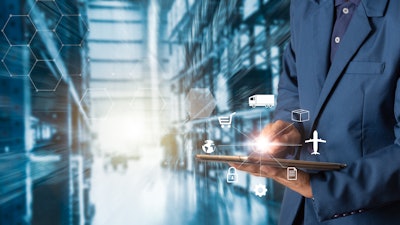
When it comes to food and beverage manufacturing, the days of companies having only a single product to keep assembly lines humming for full shifts are waning. It’s not uncommon for manufacturers to have to get creative to make money, which means diversifying their customer base.
In order to diversify your customer base, you need the right equipment and technology, but this can be an expensive endeavor. The goal is to remain flexible enough to take on new work without needing to invest more than is necessary. The manufacturers that stay successful and competitive in a brave new manufacturing world that is changing every day are the manufacturers with the ability to remain flexible. This means investing in technology that will increase efficiency and improve their competitive advantage.
The idea of robots in the manufacturing space is nothing new. They have always worked alongside humans to do the work that is considered “dangerous, dirty, and dull.” They never complain about the tasks they are chosen to undertake, but the issue is that they have only ever been able to complete a single task. The robots may perform the same task for multiple SKU, but typically a robot is permanently installed to a single location on the factory floor.
Unlike humans that can bounce from line to line and one conveyor belt to another, robots are, for the most part, static. They can’t move. Once they have been programmed to do a task, that is the only task they are capable of completing and the only location the robot is deployed. In order to get the most out of your robot investment, you need to have enough production orders to keep the robot operational at all times.
For instance, robots can be programmed to drop a scooper into a container of protein powder. That’s easy. It can complete that task thousands of times in a day. It’s one of the “dull” jobs that a human can do, but their time would probably be better spent elsewhere. But if a new contract is signed that goes beyond dropping a scooper in a jar, that requires new programming or an entirely new robot. You can start to see how this can hamstring a manufacturer that wants to take on new business, but can’t justify investing in new robots to handle new demands.
There is a way forward, however, and it has to do with the idea of a flexible robotics solution. Robots that were once programmed to handle just one task can now be programmed to handle more than one assignment. With imagination and creativity, it allows the manufacturer to stay relevant and compete for new contracts that may have been out of their reach with static robots.
When it comes to mid-market manufacturers, they exist in an environment where contracts are short and demanding. With larger manufacturers, diverse product options often drives constantly changing production demands. When one order ends, another must be signed to fill that work. If the work that pertains to the new contract can’t be fulfilled by the existing technology, more money must be invested, which, as we’ve discussed, is not a recipe for success.
This is where flexible robotics comes into play. Companies that invest money in a flexible robotics environment can take on more work with myriad outputs because the robot becomes a dynamic part of the process.
Let’s look at palletization as an example of how flexible robotics can thrive. In a traditional manufacturing environment, a robot might be programmed to stack one item on a pallet. As the product rolls off the conveyor belt, the robot puts it on the stack, and then the stack is removed and a new pallet is put down in its place. The process repeats itself. The robot may be capable of palletizing multiple SKUs but traditionally, a robot is anchored to the floor near a single output conveyor.
With flexible robotics, a robot can be programmed to move from one conveyor belt to another and stack different items on pallets, instead of being relegated to just one production line which may not always be producing. These mobile cells can be designed to relocate manually or even automatically roam the factory floor – at a safe speed, of course, and do the proper palletizing that would take multiple robots to do in a traditional setup. With a mobile robotic cell, the robot can stay utilized more frequently and less robots will be required to service multiple production lines.
Of course, it’s imperative you find the right partner who will engineer the right flexible robotic solution for your process, depending upon your offerings. You can’t go it alone. But you would also be surprised at just how flexible a robotic solution can be when it’s properly programmed to meet your business needs.
Once the flexible robotics operation is in place, earning ROI begins immediately, and the human capital becomes more valuable because they can operate more than one cell at a time. Productivity and uptime increases, and with it, the role the humans play within the manufacturing space. This makes your employees feel more involved in the work and makes your workplace more desirable when you are looking to fill open jobs.
The need to fill open roles will not dissipate any time soon. But a flexible robotics solution can give you the flexibility to put humans into key roles overlooking the plant floor and give them a greater sense of worth, while ensuring your operation can handle any task.
In the end, the manufacturers that succeed are the manufacturers who will integrate creativity into the warehouse and ensure it can flex to meet the needs of clients, no matter who those clients are or what tools they have at their disposal.