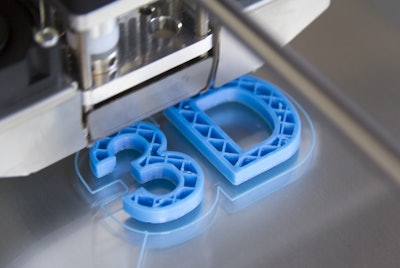
Food and beverage manufacturing plants face significant hurdles on their factory floors to achieve maximum productivity. With aging technology and the pressure to meet evolving consumer demands, operators in charge of keeping a factory running smoothly struggle to keep up when there are kinks in the supply chain for replacement parts. Machine downtime on manufacturing plant floors, whether due to equipment failures or supply chain disruptions, affect productivity and impact timely order fulfillment.
These challenges lead to increased costs, wasted resources, and disruptions in production schedules, highlighting the urgent need for innovative solutions to keep the equipment running smoothly. The need for innovation is pressing, yet the tools available often fall short. Many are eager to adopt new technologies, but where do you begin?
This ever-evolving landscape is being accelerated by the drive for further process automation. Food and beverage manufacturers are turning to 3D printing for solutions. By leveraging the capabilities of 3D printing to streamline production processes and to reduce waste and enhance flexibility, manufacturers can address these challenges effectively. This ensures a more sustainable and prosperous future for the industry.
Introducing additive manufacturing
Additive manufacturing (AM), or 3D printing, builds objects layer by layer, bypassing the need for traditional tooling and enabling faster, more flexible production. While initially used for prototyping, 3D printing has evolved into a critical tool for the factory floor, with the machine reliability and material strength required for industrial environments. Parts printed with continuous carbon fiber, for example, are as strong as aluminum parts, but weigh up to 80% less. And 3D printing on the manufacturing site gets spare parts and upgrades onto the floor or bottling line in hours rather than days or weeks.
How 3D printing boosts production and revenue
3D printing provides tremendous opportunities for food and beverage manufacturers to reduce costs and build resiliency into their spare parts supply chain. By enabling on-demand production of custom components, fixtures, and end-of-arm tooling, AM streamlines manufacturing processes, reduces costs, and accelerates production timelines.
Each minute a packaging line is down cuts into the profits. With additive technologies available on the floor, food and beverage manufacturers can resolve line down situations as quickly as possible, with minimal costs and labor. Customized tools and components become much easier to develop and implement with a reliable 3D printing solution on premises, allowing for more flexibility to change lines quickly to meet customer’s demands. Instead of waiting for new tools to be made and shipped to the factory, they can be developed and printed onsite.
For example, end of arm tooling for packaging equipment produced by AM allows teams to consolidate parts and create custom end-effector solutions while drastically reducing the cost and lead time to produce the part.
Other functionality such as vacuum systems, sensor mounting, and cable routing can be incorporated into the design of the parts, minimizing the chance of entanglement or collision with other parts of the work environment.
On a packaging line, custom push plates are used for a range of purposes: diverting and sorting, rejecting, inserting and feeding, and lane switching. Using AM to produce these parts allows for continuous improvement teams to gain additional flexibility to improve performance in hours and days instead of weeks.
Reducing inventory challenges and environmental impact
AM offers a practical solution to reducing waste and downtime in food and beverage factories by eliminating the need to physically store spare parts. Traditional manufacturing often involves minimum order quantities of spare components, leading to unnecessary costs and space requirements. With only one on the shelf, replenishment AM parts are made on-demand, exactly when and where they're needed. This shift from waiting for replacement parts to producing them as required minimizes downtime spent waiting for part shipments, reduces costs usually tied up in physical inventory, and reduces environmental impact by reducing unused inventory that ends up in scrap.
Beyond just cost savings, AM also helps cut down on environmental impact. By making parts only when necessary and at the point of use, it reduces shipping waste and supports sustainability efforts. Additionally, AM allows for designs to be optimized for efficiency, further decreasing material waste during production. This eco-friendly approach not only meets consumer expectations for responsible manufacturing but also enhances brand reputation and competitiveness.
From a financial perspective, AM's waste reduction benefits can directly contribute to increased profits. Without the need for extensive spare part inventories, manufacturers can redirect resources to more strategic areas. Plus, by making parts on-demand, the risk of overstocking or running out of stock is minimized, preventing financial losses from obsolete inventory or stock shortages. In essence, AM streamlines operations, ensuring better resource management and improved profitability for food and beverage manufacturers.
As the food and beverage industry navigates an era of rapid change, 3D printing offers flexibility at scale. By leveraging 3D printing’s capabilities, manufacturers can overcome challenges, increase production, reduce waste, and enhance agility, ensuring a sustainable and profitable future.