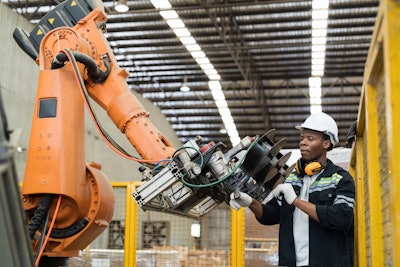
Technology has become an extension of us. Phones never leave our hands and now we can possess extra arms with the recent introduction to Apple Vision Pro, allowing us, for example, to cook while reading a virtual cookbook — no added limbs needed. In the warehouse, robotics are extending a helping arm to fill labor gaps and wearables are transforming process for the better.
A recent report from Descartes Systems Group found that nearly 76% of the supply chain and logistics leaders surveyed are experiencing notable workforce shortages in their operations, and what’s more, 37% of respondents would characterize the resource shortage as high to extreme.
A freezing halt to labor
In the frozen food sector, where working conditions can be harsh, robots are proving to be invaluable. Many of these systems operate flawlessly in sub-zero temperatures. This ensures the seamless movement of goods within cold storage facilities. Automated guided vehicles (AGVs) and robotic arms navigate through freezer aisles, retrieving and transporting products with precision.
In a tour with Ocado Intelligent Automation at the Manifest 2024, Mark Richardson, CEO at Ocado Intelligent Automation, explained the process of its Ocado Storage and Retrieval System. Specifically, the options for use in cold storage that help fill the gaps in worker shortages and in capacities where human workers might not want to work. He described how temperature-controlled storage can hinder human workers, requiring them to take breaks for their own safety. This is where robotics has a niche need to operate in stride with the human workforce.
Automation in this sector not only addresses the challenge of finding human workers willing to endure extreme temperatures but also significantly reduces the risk of injuries associated with working in such environments. Heather Chapman, head of ergonomics at Soter Analytics, says employers must empower workers with tools to understand their movements and individualized safety risks.
"After all, all bodies are different. There’s plenty of technology, like computer vision or wearable sensors, out there that can help employees understand how they are increasing their risk of injury before they get hurt. This is an easy way to give employees more oversight when it comes to how they’re moving their bodies on the job, without making them feel psychologically unsafe," explains Chapman.
Smart technology being used in a warehouse.Summit Art Creations/stock.adobe.com
ABB describes how industrial collaborative robots are bridging the gap by providing ease-or-use for those non-robotics specialists. This is key when considering the introduction of technology to a workforce that may not be in the midst of upskilling yet.
Dave Food, head of product supply chain at Board International, predicts that in 2024, supply chain companies will need to reevaluate training and upskilling strategies, as the shift from manual to digital fulfillment continues to accelerate.
Where wearables come in
Wearable technology is another innovation transforming the warehousing landscape. From smart glasses to exoskeletons, wearables are enhancing the capabilities of human workers and making the job more appealing in challenging environments.
According to ProGlove research, over half (56%) of warehouse and logistics leaders are currently utilizing industry wearables to improve efficiency in the warehouse.
“The potential is huge for human-machine collaboration,” says Stefan Lampa, robotics pioneer and CEO of ProGlove, “Undoubtedly, the number of organizations relying on automation will increase in the coming years. It’s an enormous undertaking that will bring with it a significant change in people’s work. However, there are many different boxes to be ticked in a warehouse’s total operations. As a result, the mental acuity, agility and problem-solving skills human workers provide will have a significant part to play for years to come. Over the next decade, connecting those human qualities with the power of automation technologies will be a key part of success.”
Smart glasses, for example, provide real-time information to warehouse workers, improving order accuracy and reducing errors. In food, where climates might mean a worker need to wear thick gloves, voice-activated commands through smart glasses can improve communication and task execution.
Brian Calus, director of sales at Vuzix Corporation, says smart glasses allow technicians to tap into an unlimited set of resources by communicating their situational point-of-view with remote experts and receive instruction, in real-time, to solve issues in the field.
Worker wears an exoskeleton to assist.gorodenkoff/stock.adobe.com
And digging deeper, technology isn't just in the suit but behind the data and analytics needed to test and track environments, strain and the use of the product.
For example, Verve Motion recently introduced Verve Logic, a software and data analytics platform that integrates into its wearable robotics SafeLift exosuit to pinpoint critical areas that pose injury risks to industrial workers as they work.
Christopher Buck, head of product at Verve Motion, says there is measurable impact on the world through the use of these technologies and functions.
"The real-world impact of this technology stems from the exosuit's dual function: it not only protects workers from injuries by supporting their bodies during ergonomically risky lifts but also lessens the effort needed for all lifts, including those considered ‘safe.’ As a result, workers can return home to their families unharmed and with enough energy to enjoy their lives outside of work,” explains Buck.
Nearly 42% of respondents in the ProGlove research are certain they will invest in industrial wearables to improve warehouse operations in the next five years. Meanwhile, less than one-quarter of respondents are currently using full automation. Whether it be through robotics, wearables or a combination, there's no doubt that technology is revolutionizing the warehouse sector and filling critical labor gaps. As technology continues to advance, the joint effort between human workers and these innovative solutions is offering safety, security and longevity to the future of warehouse advancement.