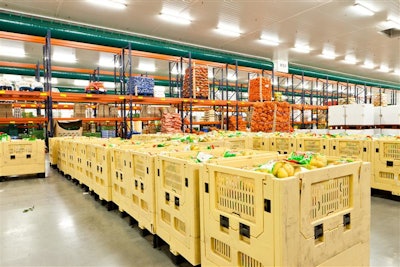
Certain products in short supply during the holiday season was the latest reminder that we haven’t seen the end of supply chain issues, especially during this Coronavirus disease (COVID-19) pandemic. Despite the fact that shortages have become a recurring theme, it is still very difficult to predict problems too far in advance and certainly not with a high degree of accuracy.
In hindsight, such shortages make sense, but can be extremely difficult to predict far ahead of time. Yet while no one has a crystal ball for the distant future, it is nevertheless possible to detect imbalances with sufficient lead time, not necessarily to prevent the imbalances entirely, but to proactively mitigate their undesirable effects.
Harnessing the power of technology
In the New Normal, end-to-end supply chain visibility is critical for spotting potential supply and demand imbalances down the road, and increasingly, there are technologies that can play an invaluable role in this.
One such technology is a supply chain “control tower,” a centralized “hub” of data, metrics and analytics that spans the entire end-to-end supply chain. There are machine learning-based predictive technologies that can understand the complex mathematical relationships between various factors of the supply chain such as labor, demand, supply lead times, etc. and can alert users with predictions that in “x” number of weeks, for instance, there is a “y” percent probability of a shortage of a certain item (even just a 20% chance of a shortage may warrant action).
A supply chain control tower can perform complex analyses in real-time using an array of data in ways that are simply impossible for human beings. It can also continue collecting additional data as time passes, which allows the algorithms to make predictions more confidently. To clarify, this is not the same as having a crystal ball. Even the most advanced control tower technology may not be able to determine, say in mid- or late November what is going to happen in mid-February when Valentine’s Day comes along. However, it may be able to detect certain anomalies in early January, which indicates a potential problem in February, and may give organizations enough time to take corrective action.
It is possible that back in the summer, some of these food and beverage processors did not know or be able to predict a shortage. But, maybe sometime during the fall, companies were able to see an upward tick in demand coupled with a labor shortage, and were able to detect this relatively early enough to give customers a heads-up in early December.
Monitoring both upstream and downstream
As recent shortages and imbalances have shown, it’s critically important to monitor both the upstream and downstream supply chains. If you’re a food and beverage manufacturer, you obviously need to have a pulse on what’s occurring downstream—what customers are buying in grocery stores, what they’re ordering from restaurants and related details. This is all data that will position you to make better production and channel management decisions. But, you also want to know what’s happening upstream--what is the supply situation? What is the labor situation? For example, how has the labor shortage on farms this year led to supply chain imbalances?
Labor shortages were also part of the reason some product shortages; it wasn’t just about the increased demand. In addition to monitoring the end-to-end supply chain and making predictions based on current data, machine learning-based technologies can use historical data such as patterns that occur on particular days, weeks and months throughout the year; the effectiveness of pricing actions; the current unemployment rate, which may affect purchasing patterns; and other relevant and related historical factors that affect demand patterns.
What to do about shortages and surpluses
Spotting potential problems in advance is only half of the equation. The other half is the question of what to do about them. If you’re anticipating a surplus of a product due to current or anticipated low demand, perhaps you could offer promotions or discounts to avoid the obsolescence of inventory. On the flipside, let’s say that even after ramping up production capacity and with the suppliers providing everything they can, you realize you’re not going to have enough of a product. There are still some things you can do.
Some organizations, for instance, have the ability to balance supply and demand using price levers. We saw this occur with grocery prices throughout the year. Another option is to explore substitutability. For example, let’s say a particular variety or SKU is going to be out of stock. Not all out-of-stock scenarios are created equal, particularly in trying times like these. It may be that even though fans of that particular variety or SKU may prefer that one, they would also be fine with buying another kind of variety, thus increasing supply for the latter may partially solve the problem.
This ties in to the importance of being transparent and communicative about the shortage, so that customers can explore alternatives. On the supply side of the equation, it’s important to take uncertainty into account when planning. A lot of systems plan based on averages—for example, let’s say an organization plans for 800 units on an average week, but that number can actually range anywhere between 200-1,400 units. Then, 800 is the mean of a very broad range, and you want to take that variability into account when planning. This should be done not just during the pandemic, but also after we come out of it because we shouldn’t assume that the world will “go back to normal” anytime soon. Some changes and trends are likely to either be permanent or at least persist for some time.
Lastly, build some redundancy into your system. If you’ve always gotten one of your raw materials from a single supplier, it may be a good time to sign up with two additional suppliers, because now more than ever before, you don’t want to put all your eggs in one basket. Redundancy is key in establishing a resilient supply chain. When all of this is taken as a whole, the dominant theme that emerges is the importance of end-to-end supply chain visibility and monitoring what is happening both upstream and downstream. What are the market and labor trends? How can technology best be leveraged to collect data and identify potential problems?
Continually asking such questions and harnessing the power of supply chain control towers and other technologies can afford organizations the time to communicate the situation to their customers and take appropriate actions.