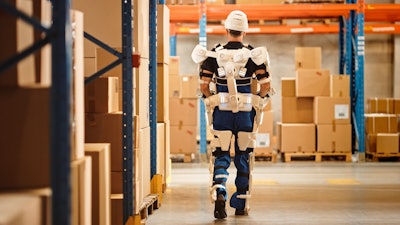
Working in commercial kitchens, food manufacturing sites or grocery stores requires employees to use repetitive movements, stand in one place for long periods, use awkward postures and operate improperly designed workstations and equipment. These duties can all lead to injuries known as musculoskeletal disorders (MSDs), which include injuries or disorders of the muscles, nerves, tendons, joints, cartilage and spinal discs.
The Bureau of Labor Statistics (BLS) reports that these strain and sprain injuries represent approximately 35% of workplace injuries. On average, these types of strain injuries account for $12 million in paid losses, according to the report. Back and shoulder strain claims are very common in workers' compensation, and these injuries can also lead to increased absenteeism and decreased productivity for employers.
Using exoskeletons to reduce worker injuries
Industrial exoskeletons are designed to take the strain off a worker's body to help reduce injuries. In fact, a study published in the Journal of Applied Ergonomics in 2021 suggests that wearable exoskeletons can reduce workers' back injuries in materials handling by anywhere from 20-60%.
It is estimated that the exoskeleton market was about a $500 million industry worldwide in 2021, but according to research from MarketsandMarkets, that figure is projected to increase to over $3 billion by 2026.
The use and adoption of exoskeletons in the workplace is growing, with numerous examples where employers are using this technology to help reduce risk in the workplace. One example of exoskeleton usage is a baggage handler at an airport – worn by someone moving suitcases all day. In the food sector, we are seeing exoskeletons being utilized in warehouses and distribution centers to help with the moving of goods.
Exoskeletons and worker safety
Companies must have a solid approach to risk management and understand the potential risks in various work environments, whether that is a food processing plant, an assembly line or a warehouse.
For example, can a worker properly wear a safety harness when wearing an exoskeleton? When wearing the exoskeleton, does the employee now take up a new footprint that changes their movement radius and causes them to strike machines or other employees? Does wearing an exoskeleton impact the employee's gait and put them at an increased risk?
In ergonomics, "risk transference" is studied to determine if wearing an exoskeleton to address a particular body part of concern can cause other potential issues. For example, does wearing an arm support exoskeleton when using a power tool amplify vibration to the hand and wrist?
It is critical that an exoskeleton – regardless of the industry – is comfortable for the worker and doesn't impede natural motions. And, of course, the exoskeleton can in no way compromise or otherwise cause problems in terms of overall worker safety.
The use of exoskeletons in the food industry
Several large food manufacturers are currently investigating the use and implementation of exoskeletons in the workplace. They see the potential use of exoskeletons to help workers lift heavy materials and work with the employees' arms at or above shoulder level.
For instance, in Australia and New Zealand, meat processors have been testing wearable exoskeletons in the meat packing environment, where MSDs are one of the most common injuries.
In the United States, the Food and Drug Administration (FDA) regulates food manufacturing. If a food manufacturer wants to implement exoskeletons in the workplace, the company would need to ensure it meets the FDA's regulations when they are in use. There are important requirements for the regular cleaning of exoskeletons in food processing settings.
Additionally, when it comes to utilizing exoskeletons in the food industry, food manufacturers need to ensure they're not creating additional hazards and exposures while addressing ergonomic risks. An assessment should be done to determine what problem they are trying to solve and start with the hierarchy of controls to mitigate the risk. If an exoskeleton is deemed appropriate as a solution, they should investigate what options are available and test the equipment. They should also look at their implementation plan, communication, employee training, and maintenance of the exoskeletons. It is also important to do a hazard assessment to determine if there are new risks when using the exoskeleton and develop plans to address them.
Safety concerns about exoskeletons in the food industry
There are some things to consider when it comes to food companies safely adopting exoskeleton technology, including:
- Improper implementation and communication by the company when rolling out the technology. The company may not have the safety management structure in place.
- Not using the correct device for the risk factors in the job.
- Not completing a complete risk assessment of the task and just buying a device that looks good.
If a food manufacturer is considering purchasing exoskeletons, they should follow the same focused process workers' compensation carriers adopt to evaluate and implement other ergonomic solutions.
Step 1: Ask what problem they are trying to solve and how the device will help them achieve their goal.
Step 2: Make sure to complete a risk assessment.
Step 3: Explore the hierarchy of controls to eliminate the hazard or engineering controls to reduce the hazard to a low level of risk.
Step 4: Create robust implementation and communication plans.
Calculating return on investment in exoskeleton technology
In the food manufacturing environment, a basic support assistive device for lifting and putting objects down could be as little as $1,000-2,000, which is something to consider when balanced against the cost of treating a back injury. Depending on the task being performed, more advanced exoskeletons can run into five figures.
There are several ways to calculate ROI. Here are some common methods:
- Reduction in incurred loss costs. This can be a challenge if there are limited losses, a new operation with no loss history or when there is job rotation or attrition because employees don't stay at the job long.
- Increased productivity.
- Reduced absenteeism.
- Improved quality.
- Improved employee morale and improved retention. Hiring is also easier because new applicants see that the company is working to protect its workers.