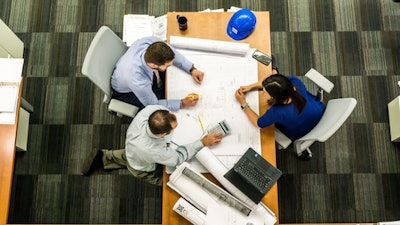
When supply chain disruptions strike, risk mitigation strikes back. And, it does so in many forms. Whether it’s enhanced software, improved employee training or solutions equipped with visibility features, managing risk is a 24/7/365 job. It requires all hands on deck, the latest and greatest technologies and the ability to pivot accordingly.
That’s because supply chain disruptions also come in many forms -- ransomware attacks and port closures, natural disasters and global pandemics, food fraud and cargo fraud.
If history repeats itself, disruptions of major magnitude will continue to rock U.S. supply chains. But, it’s how companies plan, manage and react to these disruptions that allows them to efficiently and successfully mitigate risk.
In Food Logistics’ October 2021 issue, editor-in-chief Marina Mayer talks with several industry experts about risk reduction, keeping danger at bay and what’s in store for 2022.
Here’s an interview with Kathy Fulton, executive director of American Logistics Aid Network (ALAN), with excerpts publishing in Food Logistics’ October 2021 issue. [CLICK HERE to read the article in full].
Food Logistics: The COVID-19 pandemic presented a host of risk/security challenges to today’s cold food chains. Now, the Delta Variant is looming its dark head. What is your company or companies in the cold food chain doing to mitigate and stay in front of these types of risks?
Kathy Fulton: Whether it’s a health risk, weather risk or some other kind of threat, we’re strong believers in the adage “an ounce of prevention being worth a pound of cure.” Except in our case, the operative word is preparation rather than prevention.
A big part of our work involves staying continuously connected to a wide variety of government, humanitarian and supply chain industry associations, even when there isn’t an active disaster. In fact, we have bi-weekly situation analysis and problem-solving meetings with many of these groups. During some disasters, like the times before and after major hurricanes, we’ll attend or organize these meetings and many more like them almost daily.
These connections and conversations allow us to get a much earlier and complete view of which new COVID-related and other crises are brewing and which existing crises are escalating. And, that in turn, allows us to rally our troops and map out our prevention and relief efforts more effectively.
I can’t say enough about the value of these constant lines of communication and the many other ways that we work to stay engaged across all sectors. Clearly we take the network part of our name seriously.
We also work to provide industries with better access to disaster visibility and relief resources.
One of the newest things we’ve done in this regard is to launch and host the Supply Chain Intelligence Center (SCIC). It’s a free tool that helps companies get a more real-time, dynamic view of disasters that are happening across the globe and to find out what the potential supply chain impacts are. That way, they can do a better job of anticipating and adjusting for these risks. We worked on the SCIC project for many years and had the support of many industry leaders, because we believed so strongly in the need for a one-stop resource like this.
Another way we provide this visibility is via our Disaster Micro-site. It’s a place on our website where we share helpful links and resources for various disasters, including COVID-19. While we’ll never claim to be health disaster experts (just like we’re not weather experts), we do feel called to put people in touch with the many organizations and experts that are. After all, knowledge is power.
Last but not least, we frequently host our free Disaster Simulation Game at industry events. The game is designed to get members of our industry thinking about best and worst disaster response practices. So far, we’ve taught it to more than 3,000 participants, and anecdotally speaking, I know it’s inspired many of them to go back and re-assess the strengths and weaknesses of their risk prevention and disaster relief efforts and hopefully to change them for the better.
Food Logistics: Please describe some of the technologies implemented to better mitigate risk, improve visibility/traceability and monitor farm to fork along the cold food chain.
Fulton: There are so many great commercial tools that are now available to help provide this information, and that’s a great thing for the entire food chain and the cause of disaster relief. I will say that after 16 years of helping with nearly every major U.S. disaster and many global ones, ALAN is hugely grateful to see tools like visibility dashboards and predictive analytics becoming more commonplace because they really do have the potential to be game-changers that can help companies do a better job of anticipating and preparing for disaster-related supply chain bottlenecks.
Food Logistics: Risk reduction entails other facets of the business, i.e., worker safety, product safety and plant safety. What is your company or companies in the cold food chain doing to protect employees, product, facilities, fleet and more?
Fulton: We believe one of our key roles is to be an advocate for personal and professional safety, which is why so many of our messages -- be they advisories, news releases, blogs, e-mail blasts or social media posts -- usually include some piece of advice that encourages organizations to focus on keeping their employees safe. It’s a small thing, to be sure. But, we think it’s still incredibly important to do.
Here are a few examples:
o From our S-T-O-R-M warning on our website. S tay safe. If you and your business facilities are located anywhere near a severe storm’s path, be sure to monitor your local National Weather Service forecast for real-time details. Just as important, please heed any warnings or advisories that pertain to you or your personnel and allow plenty of time for employees to evacuate or make preparations to shelter in place.
o DO make sure your employees are safe and supported. If any of your facilities were located in the tornadoes’ path, be sure to check in with employees to ensure they are safe and sound. And, if they have been impacted, make helping them and their families your first priority because even though many government and non-profits will be stepping in to provide relief, few things are more meaningful than knowing that the people we work with (and for) have our backs.
o Safety and preparation. Have you ever been one of those passengers who’s been entrusted with additional safety responsibilities simply because you’re sitting in an emergency exit row? You, as top business executives, have a similar obligation when it comes to protecting your employees. Simply put, it’s your job to prepare them in case something awful happens while they’re at work. This preparation can be as short and straightforward as safety reminders at all-hands meetings. Or, it can be as complex as formal drills and full-scale exercises like the from elementary school. Either way, you’ll be making a positive difference.
Food Logistics: Going into 2022, what are some things companies should be doing now to better identify risks?
Fulton: Stop talking and start doing. It isn’t enough to just talk about mapping out your supply chains and strengthening ties. Companies have to do the work of building true relationships across aspects of their businesses and supply chains. Those relationships could wind up being one of the most powerful and durable resources they have, especially if (or when) the power is out or systems are down.
Companies also need to expand their definition of what “potential threat” means. The last two years have shown that threats to supply chains can come from many sources besides the weather. From civil unrest and health issues to labor shortages, cybersecurity and more, it’s easy to believe we’ve pretty well seen it all over the past 24 months. But, that’s not a safe assumption to make. Companies should always be on the lookout for not only the common disasters (like hurricanes, tornadoes and cyberattacks) that could harm their supply chains, but also the unusual ones they might never have seen coming.
Companies also have to keep investing in early risk identification methodologies and practices. Just like today’s weather tracking tools can tell us a lot more about the potential path of a hurricane and our Supply Chain Intelligence Center can point out areas of concern, anything that gives them an advance heads-up is going to be of huge help in preventing what could be a “minor” disaster from turning into a major catastrophe.
Food Logistics: What are some things not addressed above that may be pertinent to our readers?
Fulton: Strong private-public partnerships are a must. When we step out of our silos (such as business, non-profit or government agency) and stop trying to draw on just our own resources and expertise, better things happen. These kinds of partnerships are where the best exchange of information about potential risks occur. They’re also where some of the best solutions come from.
Don’t forget about the importance of shared infrastructure and supporting its rapid repair or recovery either. So many relief efforts depend on getting it cleared, repaired, rebuilt, etc. as quickly as possible. And, few things are more important for supply chain resilience. Helping government understand supply chains will also help them prioritize repairs.
[CLICK HERE to read the article in full].