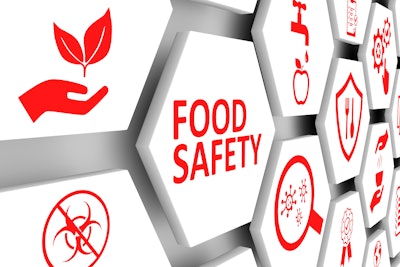
The Foreign Supplier Verification Program (FSVP) is a cornerstone of the Food Safety Modernization Act (FSMA), ensuring that imported food products meet the same safety standards as domestically produced goods. FSVP compliance is not just a legal obligation but also a critical safeguard for public health. However, non-compliance can result in severe consequences for businesses, including regulatory penalties and operational disruptions.
Here’s an outline of the tangible impacts of FSVP non-compliance and actionable strategies for avoiding common pitfalls. Leveraging proactive approaches and automation tools can significantly reduce risks and streamline compliance efforts, ensuring both safety and business continuity.
Understanding FSVP non-compliance
FSVP non-compliance occurs when importers fail to meet the requirements outlined in 21 CFR 1 Subpart L, which aims to ensure that imported food meets U.S. safety standards. Common violations include failing to develop an FSVP plan—a key framework for assessing risks and enforcing food safety controls. Inadequate supplier evaluations and missing hazard analyses, which identify biological, chemical, or physical hazards, also frequently lead to non-compliance.
Proper documentation and verification are essential for avoiding these pitfalls. As the FDA states, if a process isn’t documented, it effectively didn’t happen. Comprehensive records of supplier evaluations, hazard analyses, and corrective actions are critical to demonstrating compliance and preventing violations.
The real-world impacts of FSVP non-compliance
Non-compliance with FSVP requirements can significantly impact financial stability, reputation, and operations.
Financial repercussions. Violations can result in steep FDA fines, import alerts refusing product entry, and costly recalls requiring extensive logistical efforts, eroding profits further.
Reputational damage. Non-compliance undermines consumer trust, leading to loyalty shifts toward competitors and harming market share and long-term brand equity.
Operational challenges. Increased FDA scrutiny can result in more inspections, resource strain, and supply chain disruptions, delaying sourcing, shipping, or approvals and jeopardizing business continuity.
These combined impacts highlight the critical need for strict adherence to FSVP requirements.
Common pitfalls in FSVP compliance
Maintaining FSVP compliance is complex, with common pitfalls often leading to costly violations.
Lack of clear supplier evaluations and verification protocols. Failing to conduct thorough supplier evaluations or establish robust verification processes can result in overlooked risks, such as poor food safety practices or regulatory non-compliance.
Inadequate qualifications to implement FSVP requirements. A poorly trained team often leads to incomplete documentation, missed evaluations, and improper hazard analyses, leaving compliance gaps and increasing the risk of violations.
Complex supply chains. Managing compliance across diverse, multi-regional supply chains can lead to inconsistencies in hazard assessments and oversight, increasing the likelihood of noncompliance.
Failure to document or update procedures. Outdated or incomplete records undermine compliance. Supply chain changes, like new suppliers or processes, often require updates to the FSVP. Failing to document these changes invites FDA citations.
Avoiding these pitfalls requires proactive oversight, consistent updates, and thorough documentation practices.
Strategies to avoid FSVP violations
Navigating the complexities of FSVP compliance requires proactive planning and adherence to best practices. By implementing the following strategies, importers can mitigate risks and maintain alignment with FDA requirements.
Establish a comprehensive FSVP plan. A detailed FSVP plan serves as the foundation for compliance. This plan must outline specific procedures for supplier assessments, hazard analyses, and verification activities. A well-crafted plan ensures that all aspects of the FSVP are systematically addressed, reducing the likelihood of oversight.
Conduct annual supplier audits. Annual audits are the verification method preferred by FDA for ensuring suppliers continue to meet FDA standards. Using risk-based verification methods allows businesses to allocate resources effectively, focusing on high-risk suppliers or products. These audits help identify potential non-compliance issues before they become violations.
Prioritize staff training. FSVP compliance hinges on having a knowledgeable and well-trained team. Investing in training programs ensures staff understand regulatory requirements and the proper procedures for evaluating and managing suppliers. Specialized training is needed when products subject to different FDA requirements are being imported. Requirements may include Preventive Controls for Human Food, Preventive Controls for Animal Food, Produce Safety, and others.
Implement robust documentation practices. Accurate and organized documentation is critical for demonstrating compliance during FDA inspections. Importers must maintain comprehensive records of supplier evaluations, hazard analyses, and verification activities. Regularly reviewing and updating these documents ensures they reflect the latest supply chain and regulatory status changes, providing a reliable compliance trail.
By incorporating these strategies, businesses can significantly reduce the risk of FSVP violations while fostering a culture of compliance and food safety.
How automation can streamline compliance
Automation has emerged as a powerful tool for simplifying and improving compliance with the FSVP. By leveraging technology, businesses can address common challenges such as documentation errors, inconsistent evaluations, past due verification activities, and complex supply chain management.
Enhancing supplier evaluations. Automation tools can standardize supplier evaluations, ensuring that all assessments are thorough and aligned with FDA requirements. These systems often include pre-built templates for hazard analyses and supplier verification, reducing the need for manual input while ensuring compliance. Automation also allows for real-time updates, enabling businesses to quickly adapt to changes in supplier processes or regulatory standards.
Streamlining documentation and risk assessments. Maintaining accurate and up-to-date records is a cornerstone of FSVP compliance. Automated systems can centralize documentation, organize data for easy retrieval, and provide automated alerts for missing or outdated records. For risk assessments, automation tools analyze supplier and product data to identify potential hazards, offering actionable insights that allow businesses to prioritize safety measures effectively.
Real-time monitoring and reporting. Automated solutions enable continuous monitoring of supplier performance and compliance metrics. This includes tracking shipments, reviewing audit results, and flagging deviations in real time. When preparing for audits, these systems can generate comprehensive reports quickly, minimizing preparation time and ensuring that businesses are ready for FDA inspections.
Reducing human error. One of the greatest advantages of automation is its ability to reduce human error. By automating repetitive tasks like data entry and record management, businesses can avoid common mistakes that might lead to FSVP violations. Automated tools also provide consistency across supply chains, ensuring that every supplier is evaluated using the same criteria and processes.
By integrating automation into their compliance strategies, businesses can streamline FSVP processes, improve operational efficiency, and ensure consistent adherence to regulatory standards.
Securing compliance for a safer supply chain
FSVP compliance is not just a regulatory obligation—it’s a vital practice for protecting public health and maintaining business integrity. Non-compliance risks extend beyond fines and operational disruptions; they jeopardize consumer health, their trust and the long-term viability of your brand.
While meeting FSVP requirements can be complex, proactive strategies like detailed supplier assessments, robust documentation, and regular audits lay the foundation for compliance. Coupled with automation tools, these measures can streamline processes, reduce human error, and ensure consistency across even the most intricate supply chains.
By prioritizing compliance today, businesses can safeguard their operations, strengthen their reputations, and contribute to a safer, more transparent food supply chain. Act now to secure your place in a compliant and competitive market.