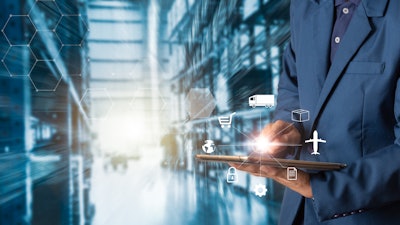
Cautionary news articles, growing industry concern and bare supermarket shelves – from basic pantry staples to potatoes, dairy, pork and beef – are causing concern about the security of the U.S. food supply chain. Many maintain the U.S. food supply is plentiful and safe, but manufacturers have now sounded the alarm, with Tyson Foods even taking out full page ads in national papers warning that the “food supply chain is breaking.”
There’s no question that the U.S. food industry is under unprecedented pressure from a pandemic and public health crisis that threatens multiple points in the national supply chain. So, how can they best navigate through this pandemic and prepare for another wave?
Companies that had anticipated the pandemic and its corresponding supply chain risk could have taken multiple steps that would help them during this COVID-19 crisis. From stockpiling personal protective equipment (PPE) for employees to varying supply chains geographically, keeping raw materials in stock and revising sick policies to incentivize people to stay at home when they had been exposed – in hindsight, companies will realize much could have been done in advance. A good pandemic plan could have helped them to consolidate the number of items they would sell in a crisis and vary their supply. Proper pandemic planning can seem daunting to those without experienced providers or guidance. Today, the value of allocating resources and priority to proper planning has become abundantly clear.
Some companies were clearly better prepared than others. Food manufacturers typically run tight supply chains due to the cost benefits that accrue, but COVID-19 has forced them to make rapid and previously unheard-of adjustments. It’s not too late for any producer to prepare for what is still ahead and take proactive action.
The chain starts here
The farming industry is under severe pressure in the best of times. They are now struggling to cope with excess supplies of highly perishable goods that they are unable to get to market. The widespread media images of farmers destroying milk, potatoes, and other crops coupled with forewarning that farmers will have to “depopulate” livestock – all while food shortages spread and hunger increases for many Americans – only heightens the national concern.
Consumers can still generally buy the food they need, if not the specific brand or cut of meat they want. Unfortunately, retailers and online sellers did not impose item limits early on, which led to consumer stockpiling that has compounded our demand issues. It’s also likely to result in consumers creating their own personal stockpiles to see them through the lockdown, and lead to much less consumer brand loyalty due to outages. When faced with dwindling supplies, economic constraints and growing unemployment, consumers will take what they can find and what they can afford. If they’re happy with that alternative product or brand they’re likely to stick with it when things return to normal.
The two biggest problems facing the supply chains now are employee illness and shortages of raw supplies. While these are certainly challenging issues, action can be taken, and it’s imperative that the industry prepare for a second, perhaps steeper, wave that could hit once social distancing rules are relaxed.
Employee shortages
Some 18 or more U.S. meat processing plants have been forced to halt production in recent weeks. While many other industries and companies have the luxury to move their employees to remote work, the crucial employees that staff our food supply facilities must physically work on those production lines. Similarly, retail employees who sell us our food are also on the front lines every day and risk contact with thousands of people who could transmit COVID-19.
To secure the U.S. food supply chain, protect employees and allow them to return to work, companies must be able to conduct immediate and consistent workforce testing, ensure every employee has PPE and strictly enforce social distancing mandates. Employers throughout the supply chain will undoubtedly need to incentivize employees to not work when they are sick, and ensure the proper accommodations are made for those employees who are in high risk categories. Employers must also factor in accommodations for those employees who have had possible exposure to the virus, accounting for extended self-quarantining periods beginning at the moment of contact.
Rethinking supply lines and raw materials
Producers and retailers typically run tight supply chains to keep expenses in line and margins tight. But, just-in-time supply chains only work efficiently and contain costs during business as usual conditions. This also makes it more difficult for those companies who have treated vendors like commodities to feel incentivized to prioritize them when they have alternate buyers competing for their attention.
Producers and retailers who are producing non-perishable materials can proactively map out their supply chain weaknesses, attempt to identify alternative supplies and work with their existing vendors to understand how solid their supply lines are likely to remain. Sometimes the shortage is due to geography, as some regions are more heavily impacted than others, and sometimes it’s a result of having to substitute alternative ingredients for harder-to-find ones – so flexibility will be key. For those producing perishable materials, they will need to calculate a minimum supply of material to maintain and pin-point alternative markets.
In many cases, there’s an abundance of raw ingredients that were previously being used in commercial operations such as hotels, restaurants and schools. Companies would do well to thoughtfully maximize these supplies according to demand, negotiating to repackage commercial supplies and ingredients for consumer sales. Retailers also must be prepared to limit purchases of sought-after goods in the early phases, as product availability will calm consumers and prevent hoarding, which is a normal reaction to shortages.
Planning for the future
While many companies were caught off guard by the severity of the crisis and its impact on our food supply chain, those that had a proactive, tested plan were able to quickly pivot and will better weather the crisis. This pandemic will fundamentally change business operations going forward, and we all need to focus not on returning to normal, but on adjusting to a new normal that finds us better prepared for a future pandemic.
The saving grace for the meat industry may be their large stores of frozen meat. And while it’s expensive to maintain, many manufacturers and retailers will opt to proactively increase their stores of essential ingredients, products and employee PPE so they are not caught unprepared again. The overarching lesson this pandemic has taught all businesses is that running tight supply chains with little to no excess may be the most inexpensive way to operate day-to-day, but it will never be the way to mitigate risk.
Without a doubt, a re-evaluation of supply chain planning to effectively weather future pandemics will require a thorough inventory of all risks to employees, customers and operations. This is the time to be vigilant and implement strategic business resilience planning to ensure the issues we're facing today don’t multiply in the future. Let’s hope that businesses have now come to realize that investing more on effective planning and mitigation will pay off exponentially in the long run.