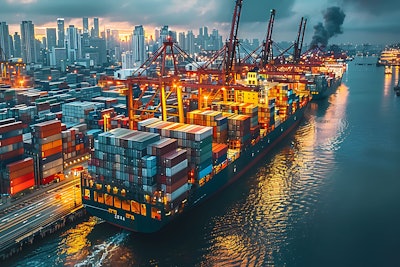
The early 2020s were a challenging time for manufacturers worldwide. A global pandemic, the resulting supply chain disruptions, and economic volatility exposed the vulnerabilities of offshore production. As a result, reshoring and nearshoring have gained renewed attention as strategies to enhance supply chain resilience and reduce dependence on distant manufacturing hubs.
Moving production closer to home offers potential benefits, from reducing logistical risks to responding faster to market demands. However, despite mounting interest and government incentives, Parsec Automation’s State of Manufacturing survey found that 50% of North American manufacturers have no plans to reshore.
This raises a critical question: Why are so many manufacturers hesitant to nearshore or reshore operations? Are they still relying on the pre-pandemic benefits of offshoring, or do nearshoring and reshoring present more challenges than they solve?
The reality is that re- and nearshoring come with both risks and rewards. A clear-eyed evaluation of these factors can help manufacturers make informed, strategic decisions about the future of their operations.
Exploring nearshoring and reshoring: Opportunities and challenges
For manufacturers evaluating supply chain strategies, nearshoring and reshoring offer distinct opportunities and challenges. While both approaches aim to enhance supply chain stability and operational efficiency, they take different paths to achieve those goals.
· Nearshoring shifts production to a geographically closer, lower-cost country. For example, a U.S. manufacturer moving production from Asia to Mexico would be considered nearshoring. This approach can reduce lead times, simplify logistics, and improve regional trade benefits, but it may also require adapting to different regulatory environments and supply chain ecosystems.
· Reshoring (or onshoring) brings production back to a lower-cost region within the same country as the manufacturer. Manufacturers pursuing reshoring often do so to regain control over quality, workforce stability, and supply chain resilience. However, balancing labor costs and infrastructure readiness remains a key consideration.
Each approach presents a trade-off between proximity, cost, and operational complexity. The key for manufacturers is to align these strategies with long-term business goals, weighing both the risks and rewards.
The risks of re- and nearshoring
Manufacturers considering nearshoring or reshoring must recognize that these are complex, large-scale transitions with significant logistical and financial implications. Some key challenges include:
1. Finding suitable infrastructure
A successful relocation depends on existing infrastructure—from industrial real estate and power grids to transportation networks. If the chosen region lacks the necessary infrastructure, companies may face unexpected costs and delays in getting operations up and running.
2. Securing a skilled workforce
Manufacturers can build a state-of-the-art facility, but without a readily available and skilled workforce, production will struggle to get off the ground. Certain industries—such as semiconductor manufacturing—require highly specialized labor, which may not be easily accessible in every region.
3. Adjusting supply chain logistics
Moving production is not just about relocating a factory—it’s about rebuilding an entire supply chain. Existing suppliers, transportation partners, and logistics workflows may no longer be viable, requiring businesses to secure new partnerships and adjust lead times accordingly.
4. Managing upfront costs and disruptions
While long-term cost savings may be possible, initial investments in facility development, workforce training, and supply chain adjustments can be significant. Additionally, the transition period may cause temporary disruptions in production, impacting delivery timelines and customer relationships.
These risks don’t mean that nearshoring and reshoring aren’t worthwhile, but they do require careful planning and mitigation strategies in order to be feasible.
The rewards of re- and nearshoring
Despite the challenges, manufacturers that successfully implement re- or nearshoring strategies can unlock significant benefits, including:
1. Increased supply chain resilience
The farther materials and products need to travel, the greater the risks of delays, shortages, and disruptions. By bringing production closer to home, manufacturers reduce their exposure to geopolitical risks, transportation bottlenecks, and unexpected global crises.
2. Lower long-term operational costs
While labor costs in nearshoring or reshoring locations may be higher than offshore alternatives, proximity to customers and suppliers can lead to overall cost savings. Reduced shipping expenses, faster turnaround times, and improved supply chain efficiencies can offset labor differences over time.
3. Improved product quality and compliance
Shorter supply chains often lead to greater quality control. With production closer to headquarters, manufacturers can better oversee operations, enforce compliance standards, and ensure consistency in materials and processes.
4. Enhanced brand reputation and customer responsiveness
Consumers and businesses are increasingly prioritizing sustainability, local sourcing, and ethical manufacturing practices. Companies that reshore or nearshore may benefit from a stronger reputation, increased customer loyalty, and improved responsiveness to shifting market demands.
Should manufacturers pursue re- or nearshoring?
There is no universal answer to whether manufacturers should nearshore or reshore. Instead, companies must conduct a pragmatic assessment of whether the potential benefits outweigh the risks. Some key considerations include:
· Strategic fit. Does relocating production align with the company’s long-term growth plans and market demands?
· Total cost analysis. Beyond labor, how will infrastructure investments, logistics, and operational changes impact overall expenses?
· Talent availability. Is there a strong workforce in the chosen region to support production without extensive retraining?
· Supply chain complexity. How will a relocation impact existing supplier relationships and lead times?
For some, staying offshore may still make the most economic sense. For others, reshoring or nearshoring may provide long-term advantages that outweigh the short-term costs. What’s clear is that these decisions should be based on real business needs, not trends or pressure to follow a one-size-fits-all approach.
Manufacturers should take a measured, data-driven approach to evaluating nearshoring or reshoring—factoring in financial, operational, and competitive considerations. With thorough planning, proactive risk mitigation, and a clear understanding of business objectives, manufacturers can successfully navigate the complex landscape of nearshoring and reshoring—leveraging these strategies not just for resilience, but for long-term growth and competitiveness.