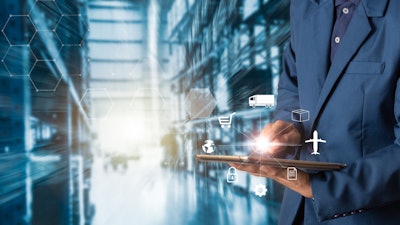
Warehouses and parcel facilities are becoming increasingly reliant on automated systems to help meet day-to-day demands while keeping operating costs in check. After all, they face growing SKU counts, while annual warehouse worker turnover remains near 50% and compensation costs have increased around 6.5% over the last two years for many businesses hiring material moving workers.
But that reliance on automation is not the only thing growing — so too is the breadth of functions automation can support. Whether a distribution center or parcel facility is looking to automate transportation, sortation, order picking, palletizing or other tasks, today there’s not just an automated answer. Often, there are many possible answers.
For operations that already have automated systems in place and are planning to scale or optimize their processes, there’s a key question: Adapt your current systems or adopt new technologies? For example, if a sortation facility needs to process a higher volume of packages, do they upgrade an existing sliding shoe sorter to meet new handling requirements, consider starting fresh with a robotic sortation solution, or embrace a solution that incorporates both?
Understanding your needs and goals
Before you get caught up with all the flashy technologies and software platforms, start the process by looking inward and getting a clear understanding of where your operation currently stands and goals for the future. An assessment will also help discover automation needs or opportunities you might not have thought about otherwise.
The operational characteristics most important to consider will vary somewhat based on the workflow you’re addressing with automation. For example, an operation’s tolerance for noise might be an important factor to consider when automating a process like sortation, where equipment can vary widely from robotic solutions or sorters with very low noise levels to technologies that produce more noise in operation. That criteria may not be as important for other options, such as more advanced, near-lights out operations. In general, though, many characteristics are consistent across different automation projects, such as these considerations for order fulfillment:
· Growth expectations. What are your current and projected growth rates for SKU counts, order volumes, lines and delivery promises?
· Facility characteristics. What constraints does your facility impose, and how might those apply differently to an entirely new solution compared to an upgrade of your existing system? For example, if a facility is pressed for space, the benefit of high-density storage offered by a new automated storage/retrieval shuttle (AS/RS) system might outweigh the relatively greater complexity and expense compared to a more straightforward upgrade. Similarly, is the facility part of a multi-site network or on a short-term lease? Those characteristics might point to solutions that have greater flexibility to be redeployed, such as autonomous case handling robots.
· Existing technologies. How old are the existing systems? In what ways are they not meeting the operation’s needs, or at what point in the future do you expect growth or changing needs to eclipse existing capabilities? Could they satisfy the operation’s needs with some minor adjustments, or is a major overhaul required?
· Inventory management requirements. How much product variety do you have to manage? How frequently are items picked over a designated period of time? Does the operation have processes like quality inspection before inventory is ready to pick? Can items ship in their original packaging or is packing in a separate outbound container necessary?
· Order fulfillment requirements. How many total orders and orders per line does the operation process per day, and how does that fluctuate throughout the course of a year? Are some items ordered more often than others, or is it a flatter, more even distribution? Perhaps the facility processes a high volume of large or irregularly shaped items that cannot be conveyed, or maybe some orders need to be moved to the top of the list to meet faster delivery promises. Consider any extra processes these orders might need to go through.
Understanding what’s out there
Armed with a clear picture of your needs, look at the full set of solutions available. While adapting current technologies may not be as flashy, sometimes the existing approach, with some simple upgrades, may still be the right one. In other cases, new technologies, or a combination of the old and the new, may the best path to create a truly effective solution.
For example, some systems make effective use of traditional and newer technologies, such as an order fulfillment solution that uses conveyor to transport items and a robotic arm and gripper for picking. It’s important to remember that deploying this type of solution is not as simple as just putting two technologies together. Achieving harmony requires calibrating each automated component and the software that manages them to work in sync – necessary to avoid logjams or “starvation events” that prevent utilization of the robotic system. To put it simply, combining multiple automated elements can produce powerful workflows, but is not as straightforward as simply selecting multiple technologies – how they are integrated to work together as a total system is key.
If your assessment revealed a need for the capabilities of new technologies, the next step in due diligence is understanding what options are available and the role they can play in your operation.
· AS/RS. Solutions like a shuttle system or cube storage served by small mobile robots can help facilities make the most of tight spaces – ideal for handling high SKU proliferation.
· Order picking robotics. Advances in vision, sensing, machine learning and gripping allow robots to identify and grasp a wide range of items with no advanced programing required.
· Robotics. For storage and retrieval, autonomous case handling robots have many of the same benefits as AS/RS solutions at a lower cost.
· Conveyor. Roller and belt conveyors move items through storage and can be used for accumulation functions, allowing for a controlled package flow.
· Sortation. Sliding shoe and cross-belt technologies can handle a wide range of items and package types, and offer various layout configurations and throughput capabilities.
· Manual guidance technologies. Trading paper pick lists for voice- or light-directed systems can enable greater accuracy and productivity, offering a solution that integrates with warehouse software systems.
· Software. The glue that holds it all together. Split-second response and information accessibility provide the control automated operations need to move efficiently.
Once you understand goals and available technologies, it’s time to make a decision. Ultimately, operational characteristics and current and future goals should be the guide when choosing whether the right solution means adapting what you have, adopting new technologies or a blended approach. Working with a systems integrator that has experience with a variety of technologies can help through every step of the process, from assessing needs to ongoing support well beyond installation. Be sure to prioritize unique requirements and continuously optimize whatever solutions you choose to match those needs as they evolve over time.