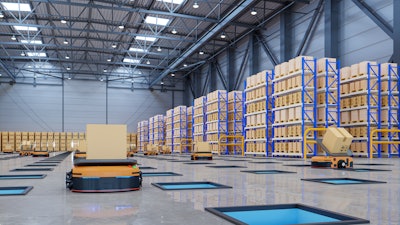
In a recent global Warehouse Vision Study commissioned by Zebra Technologies, 76% of warehouse associates agreed they would feel comfortable working alongside an autonomous mobile robot (AMR), and it’s important we keep it that way.
AMRs can take on the menial work that people don’t want to do – the things that make people feel like robots, such as moving materials and inventory. They can also empower associates to become fully autonomous on day one of a new job. Instead of having to ask another person what to do or where to go, workers can turn to AMRs to help guide them through task lists and route them to the right location for picking and put away.
In other words, AMRs can help eliminate the walking and talking that disrupts workflows, and your employees have the potential to reach maximum productivity the moment they clock in. However, this potential is contingent on trust. Employees must trust the AMRs to do what they’re supposed to do, and that’s a trust that’s often influenced by how safe they believe AMRs to be. It’s also a trust that has been challenged in the past – but only because people tend to fear the unknown. They must see to believe.
That’s one of the reasons why I have been working so hard with other roboticists, safety experts and supply chain leaders these past few years to define and advance new safety standards specific to AMRs, including the recently released ANSI R15.08 standard. If we want people to trust that AMRs are safe to use, we must give them a way to assess and verify – especially since there are no specific OSHA standards for the robotics industry today.
Click here to hear more about humans and AMRs working together:
Not all mobile robots are the same – and safety standards must account for that
Though AMRs are industrial robots, they work very differently than other robots used for assembly, conveyance, or sorting in factories, warehouses, distribution centers (DC) and transportation hubs. They are highly mobile, fully autonomous, and pretty much able to go wherever they want within the buildings mapped by their navigation systems. There is no one controlling an AMR with a human machine interface (HMI), at least not with a joystick in the traditional sense. You essentially configure AMRs one time using a cloud-based, drag-and-drop interface in a process that takes a few hours to complete. From there, the AMRs are independent.
Of course, they are receiving some guidance from workers on where to go next – especially when used for the pickup and transport of materials, goods or even recycling. But there is no one watching over them while they’re on the move. They self-navigate to the next stop. They are not confined to travel guide paths like automated guided vehicles (AGV), either. That means we must take every precaution when designing, manufacturing, deploying, and scaling AMR solutions to minimize the risk of safety incidents.
Yet, it was unclear for years what those precautions should be, and it was difficult to hold AMR manufacturers or integrators accountable for safety when most people in the industry didn’t know what to look for from a safety perspective. Furthermore, it would be irresponsible to say that the same safety guidelines should apply to AMRs and AGVs. Though both are mobile robot platforms, they operate – and interact with people – very differently.
So, a group of manufacturers, integrators, end users, and component suppliers convened frequently over a 4-plus-year period to develop what is now known as the ANSI/RIA R15.08 standard for industrial mobile robots (IMR), which articulates the specific standards for AMRs versus AGVs and even mobile manipulators.
The first part of this three-part standard was enacted in December 2020 and defines the safety requirements for industrial mobile robots, including AMRs. Basically, it provides requirements for manufacturers on the machine’s design to reduce risk and help ensure worker safety. It also helps customers identify what specifically to look for when shopping for a mobile robot – what to think about when introducing AMRs to people-trafficked environments.
When you buy a car, you know it needs working brakes at a minimum to be safe to drive. Things like power steering, blind spot assist, a calibrated speedometer, and airbags are also critical to supporting the safest driving experience possible. With an AMR, the ANSI/RIA R15.08 standard safety requirements list includes things such as what the robot can detect and see, how far and high the robot can see, how quickly it needs to stop, what signals and indicators are required, and allowed travel speeds. But you probably wouldn’t know that if we had not developed this standard. Some engineers and roboticists could advise you on safety, but you wouldn’t have a checklist to reference. Now you can download the safety requirements set forth in the ANSI/RIA R15.08 standard and review the minimum requirements for mobile robots.
Now, I should note that there aren’t any required robotics safety standards in place today from a regulatory perspective – this includes the new R15.08 standard. However, choosing an IMR that is compliant with the R15.08 standard is mandatory in the sense that you must reduce your risk and liability when deploying any type of machine or technology. This goes back to my earlier points about earning workers’ trust. There are legal and insurance considerations too, of course. But if you commit to choosing robots that you know meet the highest safety standards, then it becomes easy to build trust and reduce liabilities.
Raising the bar – and reach – of robot safety standards
The second part of ANSI/RIA R15.08, which should be finalized this year, focuses on the safety requirements for AMR integrators. It will provide guidance on how to build an integrated system with AMRs and add on components to an AMR base in a way that preserves the safety rating of the original, individual machine design. We want to help ensure modified AMRs or scaled AMR systems can still operate safely. We also want to give decision-makers and end-users clarity on how to verify solution safety in these cases.
In the third and final standard part, we’ll outline end-user safety requirements that end-users must follow. This will be the do’s and don’ts list for those configuring, managing and using the AMRs, as well as those charged with training workers and managing the entire deployed environment.
If you have questions on what an AMR or other industrial mobile robot system should include from a safety perspective, I recommend you download the current standards documentation from the RIA website. And please be sure to ask your sales representative – or whoever is helping you design, deploy and manage your mobile robot system – if all robots in your fleet are fully compliant with ANSI/RIA R15.08. If they don’t know, have them contact the manufacturer or integrator to confirm.
AMRs can solve a lot of problems your business is facing right now, so let’s make sure they aren’t adding a new one. I want you and your workers to trust the AMRs that you’re rolling out will operate safely so you can feel comfortable leaning on them more as customer demands increase and calls for greater workflow automation grow.