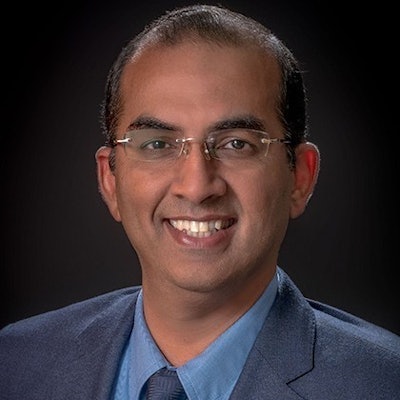
Companies around the world are working on establishing reliable cold chains that guarantee that products — whether they are fresh tomatoes, frozen foods, or life-saving pharmaceuticals — always arrive in good condition and safe for consumption, regardless of the destination.
Despite their best efforts to mitigate risks, cold chains still fail and expose products to risk and companies to substantial losses.
The damage doesn’t just hit corporate bottom lines -- it has repercussions for global food security and healthcare assurance as well.
Over one-third of the world’s food is lost to spoilage each year due to poor or inadequate temperature control techniques in-transit. This not only affects the availability of food sources, but also life-saving medical treatments across the world.
It’s vital for enterprises to not only identify and understand the biggest risks to their cold chain, but also how to address them.
Top 5 Cold Chain Management Risks
1.) Equipment Malfunction or Breakdown
This is probably the biggest reason why most optimized cold chains break down. Some of the things that could trip up a temperature-controlled supply chain operation include:
- Power Outages Whether it’s a blackout or simply someone forgetting to plug the refrigerator in, powered cooling systems can break down, especially when they’re on trucks or other modes of transport without access to uninterrupted power and redundant backups.
- Coolant/Insulation Failure Temperature-controlled containers with passive cooling typically rely on a coolant that is part of the packaging to keep shipments cold, which are tightly sealed and heavily insulated. The packaging isn’t infallible though, bad handling or wear and tear could damage the container and render the insulation and coolant moot, leaving your cargo exposed.
- Poor Circulation Temperature-controlled environments that rely on active cooling usually need proper circulation for best effect. Blocked vents or hotspots in temperature-controlled zones are a big problem in cold chains, and by the time anyone spots them it’s typically too late to reverse the damage.
- Insufficient Reserves/Redundancy Breakdowns happen, as do delays. Cold chains can accommodate these eventualities to a reasonable degree, but anything beyond that leaves stranded. Reasons why cold chains fail include:
o Lack of fuel —active cold chains depend on powered cooling solutions.
o Lack of coolant — passive cold chains depend on things like dry ice or other materials to keep shipments cool.
o Hard to find spare parts — especially relevant in long-haul shipments that use specialized or customized active cooling solutions.
o Limited back-up energy/coolant source —while redundancy is important, so is cost-efficiency.
2.) Lack of Uniform Standards or Infrastructure
Technology, infrastructure and cold chain standards differ across the world, making it more difficult for individuals running global operations to guarantee end-to-end integrity. Issues could include a lack of adequate cooling options, temperature-controlled warehouses and non-uniform cooling standards across intermediate storage facilities.
3.) Distribution/Delivery Cold Chain Risk
Unlike fixed temperature controlled warehouses, mobile cold storages (in transport) have many more variables to consider besides the amplified risk of equipment breakdowns, packaging failures or the inability to save shipments that are stranded due to breakdowns in remote locations.
4.) Human Error
Negligent staff, insufficient training, non-compliance with established protocols and inefficient use of equipment are some of the typical reasons cold chains fail. Some of the most common “human error” horror stories involve:
- Bad handling —damaged containers due to haphazard handling.
- Bad practices —leaving the refrigerator door open during last-mile deliveries.
- Bad paperwork —leading to unnecessary delays or detention.
5.) Theft/Pilferage
Whether it’s regular pilferage or the occasional hijack of a full truckload, cargo theft is an endemic problem in supply chains across the world. As a growing number of temperature-sensitive products hit the road, cold chains are now high-value targets for cargo thieves.
How Can You Reduce Your Cold Chain Risk
Cold chain interruptions are inevitable, despite your most diligent deterrents. Ensuring 100 percent cold chain reliability is possible, but also expensive, while it’s difficult to balance the growing cost of cold chain risk management with the relentless need to reduce costs, supply chain professionals today have an advantage their predecessors didn’t — the Internet of Things. IoT combined low-cost connected sensors for real-time shipment monitoring can help cold chain management.
The right, end-to-end IoT cold chain monitoring solution will afford shipping managers and quality control personnel alike the trifecta of what they need to ensure maximum cold chain reliability:
1.) Sense Data in Real-time
Knowing instantly about a temperature spike and which of your parcels are potentially affected is valuable information.
If your IoT gateway device has a GPS and the right set of sensors, you will be able to know where the temperature anomaly is happening and what possibly triggered it.
2.) Make Sense of Data
Besides risk reduction and better throughput, another bonus to continual monitoring is aggregated data. Sufficient logistics data, when properly analyzed, can be a treasure trove of predictive and real-time actionable insight.
You can use past performance and variables like the window of delivery, route congestion, possible deviations, fuel consumption and remaining coolant to continually suggest more efficient routes. Iterative improvements over time have a greater positive impact than sweeping procedural changes fraught with risk.
3.) Act on Insights Through Timely Intervention
If your shipment gets delayed, your coolant runs low or your refrigeration malfunctions, for example, real-time monitoring would give you a heads-up early enough to take effective action, dispatching a recovery or refit team to resolve the issue.
The cost of intervention is often lower than the cost of overcompensating on cold chain risk mitigation tactics like heavier insulated packaging, powered cold chain solutions or maintaining redundant safety stock, allowing you to run a leaner AND more reliable cold chain.
If you’re running a global logistics operation, it’s also a good idea to request help outsourcing your monitoring, real-time risk mitigation and other critical tasks to a response center that’s closer to the action. Outsourced logistics control towers are catching on, especially with logistics operations that need to handle large operations around the world.
In a world rife with uncertainty and disruption, you can’t always reduce cold chain logistics risk by doubling up on preventive measures. You need the power of real-time data-driven decision making possible through a combination of reliable data gathering, constant connectivity and advanced analytics – a cold chain monitoring solution that is truly end-to-end.