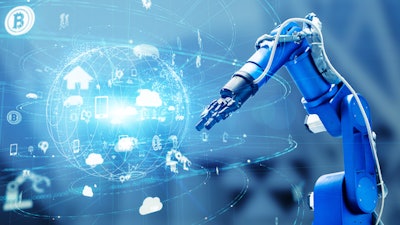
Even as the industry recovers, the persistent problem of filling open positions is burdening manufacturers big and small. The significant talent shortage in the manufacturing space is not new, but it’s getting worse. A shortfall of nearly 2.4 million manufacturing workers worldwide is expected by 2028. Unless industries address the inability to fill open positions, there will be consequences far beyond the realm of manufacturing.
With access to the most mobile and adaptable workforce to date, now is the time for manufacturing leaders to think more inclusively about their talent, and diversity is critical. One of the largest untapped talent pools is those with disabilities. This group, inclusive of 61 million Americans, has historically been overlooked by employers across all industries, including those in manufacturing.
Naturally, many manufacturing roles involve some form of manual work, which can prove more challenging for those with disabilities. With advancements in technology, however, it’s easier for those who are blind or visually impaired, deaf or hard of hearing, or for those who have mobility problems to join the workforce -- even in a field typically perceived as manually intensive, like manufacturing. Manufacturers can tap into this talent pool to fill gaps by empowering them with the tools and technologies they need to succeed.
1. Robotic-assist devices
Contrary to what some may believe, “robots,” defined in many ways, are not here to take people’s jobs. When used to support suitable applications, they are very beneficial to business operations, especially those in the manufacturing space. For example, on the shop floor, robotic-assist vehicles can be programmed to deliver and align raw or semi-finished materials, retrieve carts of material from staging locations or preposition them to specific picking locations, all without the need for human intervention. The goal is to allow the robot to help address the mundane, heavy and non-value-add aspects of the daily workload.
When it comes to employees with mobility challenges, robotic solutions can alleviate the obstacle of getting around the shop or warehouse floor. Depending on their role, some associates may be required to walk 8-10 miles each day. While that kind of distance is daunting for anyone, this is exceptionally difficult for those already facing mobility challenges. Robots help reduce or eliminate non-value-add travel, allowing employees to spend more of their valuable time focusing on higher-value tasks, ensuring greater productivity, more efficient operations, and a more satisfied employee.
2. Mobile computers
Mobile computers serve multiple functions within a manufacturing or warehouse environment. Inventory management, order picking, product returns processing, receiving and put-away activities, the reporting of manufactured goods as “finished,” all can be accessed and completed in the hands of an associate on the shop or warehouse floor. While a versatile tool, mobile computers are often preconfigured with small text and close-range scanning capabilities, a less than ideal tool and scenario for an employee who is visually impaired. However, a growing number of newer devices can be equipped with adaptive technology, facilitating the types of modifications necessary to enhance the user’s experience.
With customizable mobile computers, employees who are visually impaired can utilize accessibility accommodations to perform assigned tasks. Common customizations include larger text and fewer items displayed on the screen; modified colors and audible messages to alert employees to accuracy conditions (green) and error conditions (red); and long and short-range scanners to ensure employees scan labels consistently. Handles installed on a mobile computer enable an employee to control the device, which otherwise could prove challenging. These accommodations allow visually impaired employees to improve their individual and team productivity while accurately and efficiently completing assigned tasks.
3. Voice-directed picking
Voice-directed picking has been a staple of warehousing and distribution operations for more than three decades, improving pick accuracy, employee productivity, and by doing so, reducing operating costs. With this technology, warehouse employees utilize a headset and small wearable computer/radiofrequency device to receive verbal prompts that direct them to complete any number of daily work tasks. The picking of customer orders is a perfect example. Workers receive work queues automatically and then use a combination of predefined commands and codes to identify the pick location, quantity and details of a product. The software interprets the employee’s response, logs progress and completes work, all without the need for pen, paper or visual cues. The software will even repeat commands at the employee’s request.
While voice-directed picking was not explicitly designed for accessibility, organizations leverage the technology to empower its blind/visual impairment (BVI) employees. The headset and wearable computer device have become an adaptive technology that provides visually impaired employees with the ability to perform at the same rate as non-disabled employees. By decreasing time-to-pick, this technology elevates all affected employees’ performance in the warehouse and increases customer satisfaction with order fulfillment accuracy north of 99%.
Bottom line
Last year, just 17.9% of disabled Americans were employed, down from 19.3% in 2019. Rapidly evolving technologies create new and different employment opportunities for those with disabilities across all industries, and some business leaders may miss out on this highly motivated, valuable pool of talent.
As diversity and inclusion become more of an expectation in today’s workplace, manufacturing leaders will be well-positioned to spearhead these efforts. Investing wisely in accessibility measures and technologies will immediately impact businesses and those with disabilities, creating a more robust industry moving forward.