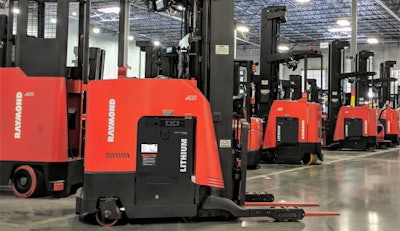
As the supply chain continues to evolve, innovations that streamline food processing, packaging, shipping and delivery progress with it. From improvements to essential lift truck equipment to advancements in automation, energy and operator training and assist technologies, the modern warehouse floor functions more effectively today than ever before — giving open-minded leaders with a commitment to continuous improvement opportunities to rethink their operations for greater profitability, productivity and efficiency.
In addition to the dynamic supply chain, upcoming trends are a result of changing consumer needs. From a greater emphasis on convenience to a renewed desire for operational efficiency and security, new preferences call for a shift from tried-and-true procedures to innovative business models that champion modernization. The adoption of which can help organizations stand out as technological and cultural leaders in the new year and beyond.
Here are some of the innovations reshaping the food supply chain and at how warehouse managers can learn to effectively incorporate these technologies to create a seamless, streamlined, end-to-end operation that meets business and consumer needs alike.
Enhancements in forklift and operator assist technologies
Since its invention and rapid adoption, the forklift has served reliably as a supply chain mainstay. Today, organizations are aiming innovations in lift truck technologies to improve on that strong foundation by incorporating advancements that: increase uptime; improve speed and mobility; streamline diagnostic procedures; and lower operating and energy costs — dramatically cutting consumption without reducing productivity.
Not only are forklift technologies evolving but also the systems that warehouse managers rely on to manage and maintain them, including operator assist and data collection technologies, are growing increasingly advanced. Operator performance data collected by labor management systems allows facility leaders to use information intuitively, helping them to solve challenges before they grow more complex.
Take, for example, maintenance records that indicate frequent tire replacement on a specific forklift. Previously, warehouse leaders might simply solve the initial symptom, like replacing the tires as often as needed, without answering a deeper, data-driven question: Why might a specific lift truck need more frequent tire replacement?
However, with sophisticated data collection and management systems, businesses can now connect siloed pieces of data together to uncover previously unseen inefficiencies. By digging deep to determine the specific operating conditions a forklift is being used in, companies can more easily diagnose the underlying issues that create inefficiencies in the first place — rather than simply addressing them after they arise.
These are the principles of Industry 4.0 — a supply chain mindset developed to encapsulate the collaboration between more-efficient machines and more-sophisticated collections data to cohesively solve challenges and reduce costs.
Of course, data collection, analyzation and implementation are only part of the evolving forklift innovation landscape. Operator assist technologies that prioritize workforce security are improving rapidly as well, increasing efficacy and reducing on-the-job demand. Innovations that minimize lift truck mounts and dismounts, as well as securely fasten operators while using lift trucks and other equipment, can drastically reduce risks while improving efficiency. These innovations allow different operators to perform different job responsibilities based on their unique skillsets and not on equipment limitations.
Best practices such as these serve another key purpose: By putting operator care front and center, security innovations help warehouse managers to meet shifting regulatory standards and proactively avoid costly infractions.
Adopting fleet automation
Customer preferences for a fast, smooth and efficient supply chain have become paramount to successful food logistics organizations. To that end, incorporating automation, including autonomous forklifts that work alongside manual operators, can dramatically increase productivity on the warehouse floor. Creating hybrid fleets that rely on a seamless network of operators and autonomous lift trucks allows warehouse managers to reduce overhead and increase overall efficiency while saving on labor costs associated with training and operator management.
This new, modernized approach makes the best use of both on-the-floor workers and advanced equipment — rather than removing integral operators from important positions, automation assists them in quickly and reliably performing key job responsibilities, contributing to a more efficient operation and fostering an internal culture of continuous improvement.
As automation continues to become an integral part of hybrid fleet management in the food logistics sphere, organizations looking to keep up should consider the benefits of incorporating autonomous forklift technology into their operations — or risk falling behind the curve in 2025.
The rise of lithium-ion
Engineered to integrate seamlessly into modern fleets, lithium-ion technology offers a host of benefits for facility leaders. From increased productivity with long run-times to greater sustainability, lower emissions, superior capacity retention and faster charging, lithium-ion lowers total costs for warehouse managers in one low-maintenance power solution designed for the next generation of supply chain logistics.
Business leaders should note the growing customer preference for lithium-ion. As green energy solutions continue to grow in importance, so will solutions that contribute to a cleaner, more efficient warehouse. As such, integrating lithium-ion should be a top business priority for leaders looking to meet customer needs while remaining compliant with evolving environmental, health and occupational hazard regulations.
Making the most of VR and AR
In today’s dynamic, fast-paced work environment, teaching and reinforcing best practices is more important than ever. A key advancement in warehouse operations involves the adoption of virtual reality (VR) and augmented reality (AR) technologies that can help new trainees and seasonal workforce members rapidly develop the skills needed to succeed without impacting day-to-day operations.
Both VR and AR systems offer unique, engaging teaching and development scenarios that equip operators with necessary skills. VR simulators act as flexible, scalable teaching tools, helping workforces become more efficient and expanding operator skills in an immersive way, minimizing risk and creating safer conditions for new hires and seasoned employees alike.
AR technology, including integrated equipment detection and notification systems, can further enhance forklift efficiency on the warehouse floor. By incorporating intelligent speed limitations, real-time object detection, operator notifications and more, crucial safety protocols and best practices are continuously reinforced, allowing employees to quickly learn and expand their talent.
Together, VR and AR advancements make for a smart investment, offsetting hidden costs associated with less-than-optimal operator training and care.
The future of forklift and supply chain technologies
As the food supply chain industry continues to evolve, these emerging trends underscore a critical reality: Innovation is less about wholesale replacement and more about strategic integration, creating a seamless work environment that emphasizes efficiency, productivity, speed, security and safety. Technological advancements such as fleet automation, sophisticated data collection, lithium-ion power and enhanced operator training tools are already transforming supply chain operations, but not by eliminating human expertise.
Instead, these systems are designed to support skilled workers, creating adaptable workplaces that forward-thinking leaders should look to implement in 2025 and beyond in order to succeed. By staying informed about emerging trends, investing in operator training and maintaining a commitment to a culture of continuous improvement, businesses can develop resilient supply chain strategies that meet both operational goals and changing consumer expectations — leading to the best products, best workplace conditions and best results.