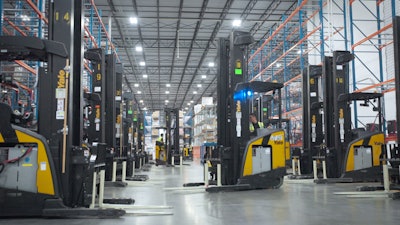
Occupational Safety and Health Administration (OSHA)’s national emphasis program (NEP) is designed to reduce and prevent workplace hazards in warehousing and distribution center operations. Announced in July 2023, inspections under this three-year emphasis program focus on hazards related to industrial vehicle operations, material handling and storage, and more.
As the NEP progresses, what are inspectors targeting at warehouses in general, and food and beverage facilities in particular? And how can operations prepare for inspection and take steps to reduce injury rates?
What prompted the program
OSHA introduced this program in response to dramatic growth in warehousing and related industries, and the accompanying surge in injury and illness rates. The warehouse workforce has more than doubled in just a decade, expanding from 729,000 employees in 2014 to more than 1.7 million in 2024.
This influx of inexperienced workers into the warehousing industry and persistently high employee turnover has exacerbated common safety challenges. In the five-year period from 2018-2022, the national incidence rate for injuries and illnesses that resulted in days away from work, restricted or transferred (DART) increased from 3.9 to 4.7 cases per 100 full-time workers. National total recordable cases (TRC) have increased from 5.1 to 5.5.
The goal of the NEP is to help operations make improvements to reduce these injuries and lost days. According to OSHA’s assistant secretary Doug Parker, "enforcement efforts are designed to do one thing: lead to permanent change in workplace safety."
How the program works
The program is nationwide, however state-level OSHA agencies can adopt the federal NEP or their own state emphasis plan (SEP) that meets the federal OSHA program requirements and is as effective as the NEP in protecting workers and work-related injuries, illnesses and deaths. The way that warehouses are selected for inspection can vary by state, but the federal program determines site selection and scheduling through a targeting system.
Establishments from two lists are scheduled for inspection in random order. The first list includes facilities with warehousing, distribution and parcel processing industry codes and the second includes a limited number of retail establishment industry codes with the highest injury and illness DART rates. State programs may use another approach to schedule facilities for comprehensive safety inspections.
What compliance officers look for
Under the inspection procedures set out by the program, safety officers must review injury and illness records and their reporting status and complete an evaluation of potential hazards throughout the facility. Inspections focus on a variety of serious safety and health hazards common in warehousing and distribution center operations, including:
· Powered industrial truck (PIT) operations
· Material handling and storage
· Walking-working surfaces
· Means of egress
· Fire protection
· Heat hazards
· Ergonomic hazards
For cold food and beverage operations, additional safety and health hazards that are potential areas of focus include:
· Personal protective equipment (PPE)
· Flooring and spill hazards
· Material handling for refrigerants and chemicals
· Ventilation
Inspections for retail establishments focus on storage and loading areas but may be expanded in scope if evidence shows that violations may exist in other areas of the establishment.
How to prepare for inspection
All states and territories offer on-site consultations that can help businesses identify areas of weakness and provide suggestions to improve health and safety. “Consultation” is an important distinction from “inspection,” as they are available at no cost and with no risk of citations.
Citations are not issued for any would-be violations the consultant identifies. Rather, the establishment simply agrees to correct the problem and records from the consultation are not shared with the inspection department.
How to address lift truck safety
Lift truck safety is multi-faceted, site-specific and requires a comprehensive approach. Food and beverage warehouses can be busy, noisy and include cold and freezing environments. Lift truck operators must carefully maneuver and place loads at significant heights and navigate tight spaces and congestion. Beyond the inherent complexities of working safely and effectively in these settings, each million square feet of warehouse space requires about 80-100 lift trucks, and recent difficulty sourcing and retaining staff can result in warehouses utilizing a larger share of inexperienced operators.
Published OSHA estimates indicate that 35,000 serious injuries involving forklifts in some manner occur annually, and studies show that greater operator training and retraining on proper forklift operation could reduce accidents by as much as 70%.
Examples of types of accidents involving forklifts and some of the possible causes or contributing factors include:
· Forklift tip-overs: turning too quickly, uneven or unbalanced loads, abrupt mast movement, turning on an incline and driving with the load elevated or on uneven surfaces.
· Accidents involving pedestrians: undisciplined or untrained workforce, insufficient traffic separation between forklifts and pedestrians, improper use of warning signs, traffic controls and signals; pedestrian and operator inattention, including fatigue, distraction and carelessness; and not looking in the direction of travel.
· Falling loads: lack of appropriate load backrest for the loads in question, damaged overhead guard, damaged forks or attachment; moving, lifting or tilting the mast too quickly; and improper load creation, including off-center, damaged and unsecured goods.
· Forklift falling off a dock or trailer: trucks or trailers rolling away, slippery floors, worn or damaged truck or trailer floors and improper or missing dock plate.
· Personnel falling from forks or personnel platforms: absence of dedicated aerial lifts; unapproved, unattended, or unrestrained lifting platforms; and prioritizing speed and convenience over safety.
· Impacts with other equipment or objects: operating too closely to other forklifts in front of or around the truck, traveling too fast for the warehouse layout, traveling without a full field of vision or not looking in the direction of travel.
Which solutions can help mitigate hazards
Comprehensive, OSHA-compliant operator training is the essential foundation for safe operation. A properly administered forklift and pedestrian training program is the single most effective means of reducing forklift accidents.
For additional support, warehouses can evaluate opportunities to leverage technology and assistance from experienced lift truck operator training or fleet management professionals. Lift truck technologies can provide varying types and degrees of support for managers or operators, such as providing a data-based view of problem areas or operating practices that require attention, helping to enhance situational awareness or even automatically reinforcing operating best practices. Every warehouse is unique, and technology can be an operational tool and additional layer of support for many OSHA directives.
Taking the next step
Inspections for the warehouse safety NEP have been underway since October 2023. As your operation prepares for inspection and takes steps to prevent accidents and reduce risks, consult the OSHA resource for your state for an evaluation of your facility.