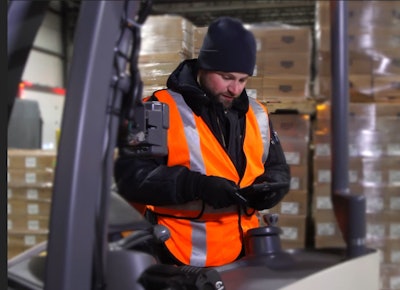
Founded in 1945 as a local distribution business, Arctic Cold Storage of St. Cloud, Minn., has grown into one the Midwest’s leading food distribution third-party logistics (3PL) providers in the past two decades. The company’s 250,000-square-foot warehouse now has four separate shipping/receiving docks with 38 dock doors. It handles between 130-160 truckloads per day, picking and prepping shipments of 17-18 million pounds of refrigerated and frozen food per week for large national franchisees and several Fortune 500 companies.
Stuck in detention
As one might imagine, managing this amount of daily trailer traffic was no small task. Arctic employed a variety of traditional tools, including multiple spreadsheets, two-way radios and yard checks on foot, but communication was difficult and often inefficient.
“One of our biggest pain points was detention and demurrage,” says Brian Kunkel, Operations Manager of Arctic Cold Storage. “We were using multiple spreadsheets and log books. Cutting and pasting from different spreadsheets sometimes led to overlapping appointments and confusion as to who had what time.”
With multiple carriers calling to schedule appointments at the same time and only one communal appointment spreadsheet, scheduling appointments with multiple carriers was cumbersome. Management might even challenge the warehouse to “step up their game” to meet demands if certain time slots were double-booked, leading to chaos in the logistics office and on the facility floor.
Moving trailers was often inefficient, as well, and detention charges occasionally occurred. Yard drivers would often come up from the back lot to the front desk to get a new list, which wasted time driving back around the building to pick up another trailer. By the time they reacted to the paper list, it could be obsolete from changes. Warehouse personnel would often have to scroll between a security camera or back and forth between different logs to check the status of trucks at the loading dock. If someone else was in the needed spreadsheet, they would have to wait until the other person released the file.
“The radio chatter was constant,” says Kunkel. “Communication is important, but radio chatter all day made it difficult to communicate effectively.”
Dok-Vu: A paperless system from Rite-Hite
Arctic shared these struggles with Rite-Hite, a Milwaukee-based company known for advanced loading dock and in-plant safety equipment. Rite-Hite had heard similar experiences and pain points from other customers, and was already working on a loading dock management software to solve these common challenges. Utilizing their strong partnership, Rite-Hite worked closely with Arctic throughout ongoing development to address specific issues and test various digital solutions. In May 2019, Arctic ditched its old-school paper system and fully committed to Dok-Vu.
Dok-Vu is a paperless software system for management of logistics operations. It virtually eliminates the need for spreadsheets and two-way radios that had previously connected managers, materials handlers, yard personnel and carriers. Dok-Vu allows employees to see an at-a-glance status of each dock position, while carriers can avoid long lines with the option to check themselves in along with opt-in text alerts on load status.
Managers using Dok-Vu can oversee appointments, monitor dwell times and help keep docks fully utilized, gaining better control of detention and demurrage charges, labor costs and shipping accuracy. Thanks to its intuitive loading dock dashboard, Dok-Vu also allows managers to review current trends and historical data to make more data-driven decisions and help identify additional improvements that they simply couldn’t see before.
Efficiency and safety improve, while detention and radio chatter diminish
Arctic’s employees and management have been thrilled with the Dok-Vu software solution. It has simplified their processes, increased productivity and improved efficiency at all levels. As a primary result, turn times and detention charges have been greatly reduced.
“If you look at our loading dock, you don’t see trucks lined up like you did 18 months ago,” says Kunkel. “The entire process has been streamlined.”
This efficiency has allowed Arctic to reduce its detention charges by 73% year-over-year. Dok-Vu has been the biggest reason for this rise in productivity. In turn, Arctic estimates an 8-10% increase in truck volume per week, which means more orders can be fulfilled.
In addition, staff is happy that multiple appointments can now be scheduled simultaneously and information can be accessed through one central location. Scheduling no longer involves waiting for spreadsheets to be updated, saved and closed; they can be made without any waiting or duplicated efforts.
In fact, due to the Dok-Vu paperless system, training time for new employees has cut down by 50%. New employees are able to get up to speed faster and do the work they were hired to do.
The easy-access communication and status updates go beyond scheduling. Material handlers, lift drivers, carriers and facility management are all on the same page when a truck arrives to be unloaded and/or loaded due to the Dok-Vu dashboard on tablets and monitors throughout the facility.
“The key is real-time communication,” says Jay Condon, general manager of Arctic Cold Storage. “Everything is electronic and real-time. There’s less of a chance something gets missed.”
Condon said that radio chatter has diminished dramatically. Radios are still used, but only a few times an hour, he said. It’s allowed all parties to focus on their job at hand without having to communicate all the details, which in turn has improved the safety of their operations.
The Arctic yard personnel is much happier, despite exhibiting some skepticism before Dok-Vu was launched. Arctic’s yard jockey, Andy Fitzgerald, described the company’s initial hesitancy.
“It’s putting a lot of faith into technology, but that’s what it is today. That’s the day and age we’re in,” said Fitzgerald, who added that since implementing it in May, his yard team has fully adopted the paperless solution. “There’s always going to be a question of will it work? And it does.”
Truck drivers and carriers have also noticed the improved communication and efficiency. Condon said he and Arctic understand that “drivers make their money on the road,” and Dok-Vu helps them do that. Drivers are able to check themselves in and out, as well as receive text alerts when a dock is available for loading or unloading.
“The dashboard has been very easy to use; it gives us great visibility to the facility,” said Kunkel. “We’re able to see what’s going in and out of trailers; what trailers have been in the dock for an extended period of time; any movement that’s going on throughout the facility, all under one spot, so it’s been a great addition.”
Arctic adding more docks to Dok-Vu
Though the entire operation is utilizing Dok-Vu software, Arctic plans to add onto the 7 docks with smart controls and equipment connected through the IIoT platform. And, 5 more will be upgraded by the end of 2020 and expects the remaining positions will be connected by the end of 2021 as part of a 3-year plan.
“Dok-Vu is game-changing,” said Kunkel. “It creates that bridge between our operations, our office and carriers.”