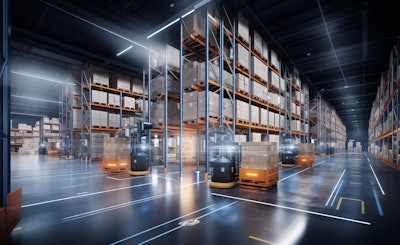
In the complex arena of food logistics, technology is increasingly intertwined with operational strategies to drive efficiency and responsiveness. Warehouse orchestration, leveraging predictive and prescriptive analytics, emerges as a transformative approach to optimize warehouse operations.
Integrating warehouse orchestration with existing systems
Warehouse orchestration technologies are not standalone solutions but function atop existing warehouse management systems (WMS), warehouse execution systems (WES), and warehouse control systems (WCS). By drawing and consolidating data from WMS, WES, yard management systems (YMS), and even labor management systems (LMS), warehouse orchestration creates a comprehensive overview that enables real-time decisions and facility-wide optimization. This integration allows for a single interface capable of managing the four critical pillars of warehouse orchestration: labor planning, inventory management, human-robotic interactions, and space optimization.
Warehouse orchestration defined
Warehouse orchestration orchestrates logistical components using advanced analytics to enhance decision-making and operational efficiency. It combines predictive analytics, which forecasts future scenarios, with prescriptive analytics, which outlines strategic responses. By optimally planning the perfect sequence of activities within the given constraints at each site, warehouse orchestration ensures that every operation aligns with business objectives.
1. Labor planning
Efficient labor management is pivotal in logistics. According to a study by MHI, almost 90% of warehouse operators identify workforce management as a key competitive factor. Predictive analytics forecasts labor needs by analyzing historical data, seasonal peaks, and order volumes. In contrast, prescriptive analytics utilizes this data to optimize where each person spends their time as conditions change, ensuring peak productivity. Critical to success in this area is the strategic planning of personnel deployment on specific equipment or designated pick areas, which is fundamental for operational efficiency and safety. This is challenging for warehouse leadership today, as site constraints, equipment availability, and overall flow constraints require labor management by task and area to constantly be reshuffled to promote optimal inventory flow.
2. Inventory flow management
Effective inventory management is crucial for cost control and service levels. Mismanaged inventory flow can lead to a significant loss in revenue due to controllable cuts, stockouts, and overstock issues. Predictive tools analyze past trends and current planned orders to project future inventory availability, and prescriptive analytics advises on actions to align inventory with expected demand, significantly reducing carrying costs and enhancing service quality. This manifests in a system responsible for managing both inbound and outbound operations from the same labor pool with the same spatial constraints to significantly enhance controllable fill rates by integrating these flows seamlessly. This often results in activities like cross-dock at consumer goods sites and almost always veers away from the usual "if we're busy, focus on outbound" framework often employed by the tribal knowledge present at most facilities.
3. Human/robotic interaction management
The integration of robotics in warehouses is transforming operations, and it's well documented at this point that robotic integrations can significantly increase pick speeds and throughput at facilities. However, most sites struggle with the seams of robotics or where robotic processes interface with human labor. "Cobots" are often employed to increase pick speeds, but log jams can occur at the more manual "packaging" processes. In consumer goods facilities, automated storage retrieval systems (ASRS) are fantastic for picking, but the human constraint of loading can cause bottlenecks and late loads outbound. Warehouse orchestration can balance out this work by strategically integrating human and robotic workflows to ensure an optimal handoff point between tasks. A significant amount of mathematics is required to do this well and appropriately consider the dynamic availability of human labor against the static capacity of robotic systems.
4. Warehouse and dock space optimization
The final component of warehouse orchestration involves maximizing warehouse and dock utilization without negatively impacting throughput. By understanding how much space will be needed for each upcoming shipment or receipt, optimization can recommend adjustments to optimize space usage, avoid congestion, and maximize flow through each facility.
In large consumer packaged goods (CPG) sites, the constraint is often racking or door space. However, the critical space constraints in retailers can be a pick buffer between processes limited to how many orders they can hold before shipping. Optimizing the use of these areas while considering labor, inventory availability, and robotic interactions becomes critical to running an effective site.
Leading companies have realized substantial benefits from implementing warehouse orchestration. By anticipating market fluctuations and dynamically accounting for demand to respond proactively, these companies have improved efficiency and customer satisfaction, setting a benchmark in the logistics sector.
Conclusion
Warehouse orchestration stands at the forefront of logistical innovation, combining predictive and prescriptive analytics to foster a new level of operational intelligence and adaptability. This strategy is vital for logistics companies to meet current market demands and scale for future challenges, making it a cornerstone of modern warehouse management.