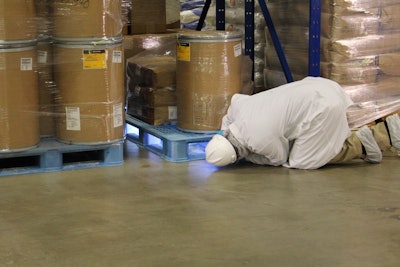
As the old adage goes - “plan your work and work your plan” – and this strongly applies to pest management. Companies cannot have success without a well-executed and thoughtful plan, and the consequences of not having one can appear quickly. Pest management plans fail for one of two reasons—the plan was not appropriate for the pest or the plan was not followed properly.
In a food facility, shortcomings commonly include:
1. An inaccurate initial risk assessment.
2. Customer and pest management provider (PMP) expectations are not aligned.
3. Changes in the facility that the plan does not account for or adapt to.
4. Not having the right tools or people to implement the plan as outlined.
Pest problems are typically escalated as a result from a poorly executed plan, and sometimes multiple pests and problems are at play. A new risk assessment must be performed by a PMP who knows the food industry, including the risks and sensitivity that come with it. With that knowledge, the PMP can critically assess the risks and develop a plan that works toward mitigation. The plan should never be a quick fix, although it should include initial high-impact resolutions. It should identify the risks to help develop the rest of the plan, which includes providing monitoring tools and frequency to assess the situation over time, control tools that the PMP can control immediately, and over time, implementing sanitation and structural changes the customer can follow to reduce harborage (both potential and actual) and creating a follow-up with plan modifications as needed or at least annually.
Site risk assessment
Since the entire plan rests on the risk assessment, it’s important that it’s done thoroughly and correctly.
The following elements must be included for a strong risk assessment:
Data dive. Particularly when recovering from a bad pest management plan, it’s important to know how things got the way they did. Did it happen quickly, with one small issue exploding into a huge one? Or was it gradual and over time? The new PMP typically won’t have access to this data, but if the customer is comfortable providing the information, it will make the risk assessment more accurate. This may include:
► Previous plan’s service reports and audit reports
► Trends
► Facility changes, both structural and processual (Did the client add a new building? A new product? Become certified organic?)
► Discussions with key members of the team as they’ll most likely have their own, often varying, perspectives of what went wrong
► The facility’s environment. While we learn the most about a facility by being on-site, we can get clues of additional risks by looking at that account through global satellite imaging. Using a program, such as Google Maps, we can see important pieces of the landscape that may influence the risk to the facility that we may not see on site. Some risks may include a body of water, railways, proximity to zoos, etc.
On-site assessment. Research and experience doesn’t replace what’s happening on-site. Risk assessments are never one-size-fits-all. Each facility will have differing priorities and resources that will determine how they handles those risks. These differences may include:
► Age and structural soundness of the facility
► What ingredients are processed
► Organic certification
► Neighboring facilities
► Greenspace and landscaping surrounding the facility
► Sanitation processes
► Product flow
► Equipment design
► Known or highly likely pest issues
► Varying regulatory standards to meet
Identifying solutions. Once you’ve listed all the pest risks of a facility, the next step is to propose solutions to mitigate those risks. Clients may or may not choose to move forward with those solutions, but it’s vital that they’re identified and proposed as part of the initial risk assessment, particularly when recovering from a poor pest management program. A common mistake some PMPs make is to propose what the previous PMP had in place, whether it was a good or bad plan. Instead, approaching the facility as a clean slate and proposing solutions that will mitigate all the risks identified from the new on-site assessment, is crucial to providing lasting solutions. As part of this, the PMP proposing these solutions must be well-versed in all the potential solutions. This may require discussion with other members of the team or exploring alternatives to standard responses. Looking at a situation with fresh eyes and innovative, progressive recommendations, can make all the difference in resolving the situation.
Developing a pest management program
After completing a thorough risk analysis, the customer and PMP must agree on a program. This program should address as many of the concerns identified in the risk analysis as possible. The customer will build out this program based on their perceived priorities and risks. A customer who has felt the impact of recalls or shutdowns due to a poor pest management plan may see the value in a more robust program, rather than one who has not felt that same impact. Communication and discussion are necessary so that the PMP and client become aligned on what the expectations of the program are. There’s no right or wrong program, but our expectations as to what that program will resolve has to be clear. Once aligned, the new program is put in place. Often, there will be more plans to add to the program as necessary, but this first program is the starting point.
Team-based execution
Executing an effective pest management plan takes a team. The technician is at the forefront of execution and must be well-equipped to handle the problems identified in the risk assessment efficiently, effectively and within the confounds of a sensitive environment. They must be able to use the information their monitoring devices show and focus on control techniques. The PMP will serve as a partner to the client to communicate facility changes that are necessary to support the control tools implemented.
In addition to this partnership, the technician also needs a team behind them. Management, colleagues, and technical resources need to be readily available and utilized as necessary. Particularly when recovering from a poor pest management program, an extra set of trained eyes is invaluable.
Program evaluation
One of the most important responsibilities of a PMP is to perform an annual facility assessment and quality audits on their food accounts. Some of the plan weaknesses may already be known and were previously deemed of low priority. The auditing and assessment bring those weaknesses to light and make them a higher priority as decisions are made to change the program.
All pest management programs should evolve as conditions, pests and facilities change. A stagnant program can often be the cause of the failed pest program. The audit and assessment may also uncover weaknesses in the program that were not previously identified. As large problems are tackled, smaller ones become more evident and need to be addressed in the program. The management team is in a position to make those changes through discussion with the client and technician. This evaluation and assessment of a program will keep the new PMP’s pest management program from becoming “the previous PMP’s poor pest management program.”