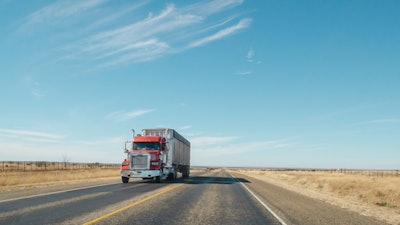
Evaluating what truck makes and models best fit a fleet’s operation can be an arduous process. Savvy companies with transportation fleets that operate Class-8 trucks spare no expense in evaluating tractor makes and models that best fit their operations and keep costs low. However, determining truck life cycles and knowing when to sell or trade that equipment can be just as daunting. Advancements in new trucks have made analyzing trade cycles critical for carriers looking to maximize their investment.
The change starts with a paradigm shift in life cycle asset management, moving from functional obsolescence to economic obsolescence. Legacy philosophies in fleet management must shift from “how many years can I run this truck” to “how many years should I run this truck.” Adding to this philosophy is an increased scrutiny of safety-related costs, including accidents and litigation. Companies are also taking safety obsolescence into account, realizing as trucks age there becomes a period when it makes more sense to upgrade to newer trucks with advanced safety features. The answer is found in a data-driven approach, with decisions that are made based on actual cost data.
Timing a truck’s life cycle means striking a balance of efficiency and asset disposal
Big data is the term that many fleet managers use to refer to a large set of data that is almost impossible to manage and process using traditional business intelligence tools. And, almost every industry today utilizes big data in some fashion. The interpretation of data and how data is used is where many companies fail in achieving the most value. Leveraging big data affects everything from operational strategies, logistics, procurement, truck maintenance practices, safety initiatives and more. In fact, the main components of operating costs that can be significantly reduced through proper analysis of data are maintenance and repair, market intelligence, fuel, safety, interest and tax implications.
As vehicles age, fuel efficiency decreases, while maintenance and repair costs increase, especially as warranties expire. From a safety perspective, as the vehicle ages, the safety technology becomes obsolete, putting the firm and their drivers at risk for costly accidents. For companies that emphasize the importance of bottom-line savings, there is a heightened importance for data to understand the Total Cost of Ownership (TCO) to remain competitive. This is done through paying closer attention to the life cycle of each individual truck. Elements such as the cost of fuel, utilization, finance costs, market conditions, maintenance and repair all impact the truck’s unique individual life cycle, giving better insights into determining and calculating the best time to replace aging equipment.
Cost factors that help base decisions for equipment acquisition
When a fleet meets its warranty threshold, costs associated with that truck immediately spike, thus making shorter asset life cycles more cost-effective toward an organization’s bottom line. Fleets that run their trucks on a seven-year life cycle instead of four years spend an additional $34,379 on maintenance per truck compared to four-year maintenance costs. Fuel expenditures also rise precipitously. In fact, according to a recent truck life cycle data index, a fleet can save up to $5,084 in the first year of fuel expenditures when replacing a 2016 MY sleeper, representing a 15% increase in fuel economy while reducing CO2 emissions. The timing of when to dispose of a truck does not rely solely on its maintenance schedule and fuel consumption. Its position on the balance sheet also comes into play.
From a finance standpoint, after year four of operation, variable costs per mile increase dramatically. The excess variable Cost Per Mile in Yrs. 5-8 is equivalent to $1,100 of fixed cost per month!
Key metrics to consider when implementing an asset life cycle cost management (LCCM) strategy
· Use analytical tools and data to gather miles for insights into fleet performance and variable and fixed ownership costs
· Finance deprecation vs. market value
· Fuel economy overview year-over-year
· Comparative cost analysis – comparing TCO cost of each vehicle against the newest model year
· Lease vs. purchase analysis
· North America Class 8 Tractors build rates and equipment cost analysis
· SWAP rates
· Residual value analysis – year over year
In conclusion, data analytics serve as the catalyst for change in analyzing each of these cost factors to help shift truck acquisition strategies for more optimal and efficient equipment life cycles. Shorter asset life cycles continue to prove to be more cost-effective, and tax reform standards have placed a greater emphasis on the lease vs. buy decision. Leveraging a shorter-term asset management life cycle cost management strategy based on flexible leasing will help organizations take advantage of lower tax rates, which should help expand their business and have an overall positive impact on the economy.