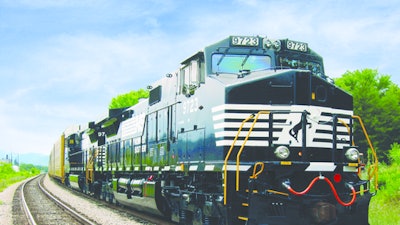
The transportation, manufacturing, distribution and society in general dodged a big bullet recently when a massive rail strike in the United States was avoided. We are not out of the woods yet, there is more negotiating that needs to be done to get a long-term agreement in place to keep rail cars moving. But, for now, trains are running. This is just the latest example of the unsteadiness that has come to define today’s global supply chain.
A transportation crisis averted…For now
The supply chain industry has been dealing with one issue after another since COVID-19. All industries, especially manufacturing and anything related to supply chains and the movements of goods were hoping that once society had a handle on the pandemic, things would get back to normal. Well, not so much. There are still a number of lingering issues caused by the pandemic that continue up and down the global supply chain, as well as problems that actually started before COVID-19 that are now disrupting the day-to-day movement of goods. A rail strike would just add insult to injury.
Now that it seems the rail strike won’t happen, the issue as to why the rail strike would’ve happened to begin with has been pushed to the back burner. That is where the industry has made mistakes throughout the pandemic, dealing with issues like transportation shortages, expanding value chains and rapidly changing consumer preferences. Out of sight, out of mind. However, that is not how the supply chain works, behaves or thinks. The industry needs to treat the supply chain like it is a living, breathing thing that has a mind of its own. Companies need to anticipate how its moves, twists and turns will impact both short and long-term scenarios for all manufacturing sectors and all regions.
People often make the mistake of not realizing how much the manufacturing and distribution industries rely on rail transportation. Industrial, chemical, high tech, consumer products and food and beverage all rely on rail to transport goods throughout every level of the supply chain. Raw materials, ingredients, packaging, work-in-process, finished goods and essential supplies like fuel, solvents and processing chemicals are best served by rail transportation. If there was a strike, essentially all of these transports would just shut down. Now, many manufacturers could temporarily turn to alternate means of transportation to weather the storm of a massive strike. However, the ripple effects of this would impact many other businesses and cause massive supply chain distress.
Manufacturers need to have contingency plans in place to help manage around these issues. Some industries related to manufacturing and supply chain are still not in a position to handle another big disruption. The pandemic forced manufacturers to re-engineer facilities to make safe working environments amid labor shortages.
Again, pandemics, natural disasters, storms, fires and nationwide transportation strikes are huge disruptors that are at the top of the severity scale. Being able to get through these types of issues unscathed is probably impossible to do. However, there are things that can be done to try to avert major impacts to business operations.
Better managing industry disruptions
The first step toward recovery is learning to better manage a crisis. Having processes and systems in place to establish contingency plans is a must.
One step is a sales and operations planning (S&OP) process. While considered a long-term planning process primarily used for strategic planning, S&OP is a process that can help businesses design the strategic plan and use the process to manage the operation and execution levels of planning. It takes the integration, dissemination and passing of data from distributions, forecasting, manufacturing and supply planning systems to align all areas of a business with trading partners. One of the critical steps to make this work at all levels of planning is the inclusion of your entire business ecosystem – your customers and suppliers as well as the departments of your enterprise.
A good, solid S&OP process can help with the following areas:
● Distribution and transportation contingency plans
● Inventory management
● Managing customer delivery requirements and expectations
● Managing suppliers and supplier inventory
● Managing outsourced process and contract manufacturing
● Temporary process changes
Bottom line is, we are in an age of constant flux in many markets served by all manufacturing industries, and supply chains continue to get taxed and tested. The companies that succeed and can manage through this constant flow of disruptions will be the companies that have the people, processes and systems in place to quickly gather and analyze large amounts of data and use it to initialize and execute multiple layered plans at the same time.