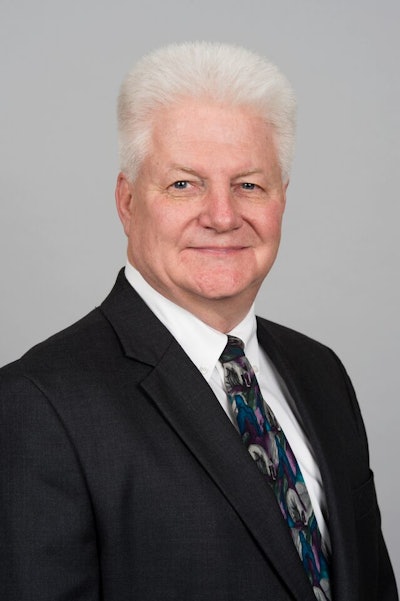
In the days before motorized vehicles became the standard means of transportation, what we now call “food logistics” was a much more parochial pursuit. Nearby farms were used as the main source of meat, grains, fruits and vegetables for the larger cities, while in rural areas, “logistics” oftentimes simply meant a trip to the woods to hunt for tonight’s dinner, with a stop at the family garden to gather the side dishes.
That all changed with the invention of motorized vehicles, as well as, some 50 years later, the creation of a comprehensive interstate highway system that supplements regional roads and puts many consumers a day or two’s drive away from the food and beverage source. The modern food logistics infrastructure is so efficient that it is estimated that food served in the United States can safely and efficiently travel, on average, 1,500 miles between producers and consumers. This is equal to the distance between the cities of Buffalo, New York, and Houston, Texas.
In conjunction with an optimized distribution infrastructure, improvements in refrigeration techniques have helped ensure that the thousands of tractor trailers that continually crisscross the nation can deliver their payloads, while they are still at the height of freshness. In fact, the system of farms, warehouses, distribution centers and commercial tractor trailer fleets has become so efficient that there is only one person who possesses the capability to upset the system: Mother Nature. But short of a debilitating hurricane, earthquake or winter blizzard, the food logistics train keeps rolling along.
That is, unless it is not powered reliably and efficiently. That means that the operators of fleets for food distribution must always have a ready supply of fuel on hand. However, achieving the highest level of optimized fuel use and cost can be tricky. That’s why food-distribution companies have begun investing in fuel-management programs that have been developed by providers who know how to deliver state-of-the-art fuel-management services. These companies can offer their expertise as a way to help the food distributor optimize fuel usage and cost in a number of critical areas. Among the most notable are:
Fuel Supply
Ensuring a ready supply of fuel is paramount to the success of any food distribution company. That’s why the main daily challenge that food distributors face is preventing fuel runouts that leave fleets idled, and knowing when and how to purchase fuel at optimum levels. They also must be able to integrate advanced fuel management technology with existing fuel supply systems, such as:
- Properly implementing automatic tank monitoring and unattended fuel-control systems that can drive greater business value through access to real-time fuel usage and cost data.
- Fuel-management solutions and services that help reduce overall fuel costs through strategic procurement operations, lower transportation costs, optimized inventory management and highly targeted financial management can result in increased profitability.
- Fuel-management solutions and services that can give food distributors their own fueling operations a complete platform to manage that fuel operation.
In addition, ensuring accurate fuel-inventory levels is critical for the food distributor since running out of fuel can be very costly and detrimental to the overall success and efficiency of the supply chain. No matter the size of the food distribution fleet, there is the chance that a lack of coordination and communication between its various operations will exist. This can lead to additional unnecessary and redundant fuel inventory reporting processes that can take the form of disruptive runouts or inefficient refueling needs, with any mistakes potentially resulting in higher fuel costs or prohibitive equipment downtime.
Alarm Management
Alarm-management services provide proactive visibility into what’s happening in fuel storage tanks, which is an important consideration when the food distributor has its own tanks from which fuel is drawn and which will have to be refilled on a regular basis.
Alarm management enables food distributors to mitigate environmental risks and reduce on-site maintenance costs by managing compliance, optimizing maintenance regimes and triaging site alarms.
Without an automated solution in place to proactively address alarm conditions and compliance issues, which are typically caused by overfills or undetected leaks, alarm trends cannot be analyzed and violations could go unnoticed. Unresolved compliance issues can result in hefty fines and may cause environmental damage, which can cost millions of dollars to remediate. In addition, the negative publicity that can accompany a high profile leak or spill event can do irreparable damage to a company’s brand and cause additional millions of dollars in damage due to loss of reputation.
Equipment Operation
Using enhanced fuel services also can be a notable way to improve the preventative maintenance capabilities of the food distribution fleet. Improved filtration on fuel-storage tanks will help improve fuel quality when it reaches the tractor trailer’s fuel tank. Equipment that is powered by high quality fuel will experience improved miles per gallon of fuel consumed, as well as reduced vehicle maintenance relative to the number of filter changes that are needed, engine maintenance, etc., all of which lowers operating and fuel purchase costs.
Fuel Theft
Food distributors that have on-site fueling operations will always be at risk of fuel shrinkage, either from internal employees or outside sources. Real-time access to fuel inventory levels and fueling habits at any time of day is a huge advantage for any company. However, the operations at food distribution companies can consist of hundreds of vehicles that are fueled at all times of the day or night, which can make the tracking of fuel usage patterns and inventory levels tough to get a handle on.
With that in mind, utilizing an automated fuel-tracking program that monitors fuel levels in the storage tank, along with when and how often a vehicle is being fueled, will provide important real-time inventory data to the site manager. This monitoring ability also can “red flag” any suspicious transactions pertaining to a specific vehicle. This can immediately eliminate any guesswork regarding expenditures for a specific day, week or month, and it is a highly dependable way to identify or mitigate theft, whether from an internal or external source.
Food distributors can only reach the peak of efficiency if their rolling fleets are kept on the road rather than idling at the fueling island or on a lift in the maintenance bay. This means that the fleet’s fuel supply cannot be compromised, and runouts cannot be tolerated. Ensuring an adequate fuel supply is only one piece of the puzzle, however. A truly successful food distribution fuel management program is one that also enables the operator to confidently manage site alarms, monitor the instances of potential fuel theft, and make it possible for the fleet to operate with reduced chances that time consuming and cost robbing maintenance or replacement services will be needed.
Peter J. Cochefski is the director of Ryder Fuel Services, Houston, Texas, a subsidiary of Ryder System, Inc. He can be reached at (281) 647-8900, ext. 222, or [email protected]. Ryder Fuel Services is a provider of fuel management services that focus on compliance management, remote monitoring, alarm management, service management, fuel management and supply, and environmental best management practices. For more information, please visit ryder.com.