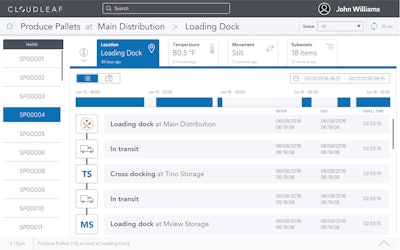
Editor’s Note: The following article is brought to you by Cloudleaf in partnership with the Supply Chain Network.
The world is getting smaller and in this digital age of information and online services, consumers are traveling further abroad and experiencing new exotic cultures, foods, and ingredients. In the US, these seed-experiences have grown to support a thriving ancillary food & beverage market of premium products. In fact many boutique retailers, including Trader Joes and Whole Foods, now exclusively sell hard-to-find, innovative, great-tasting foods, many under their own label. Larger hypermarkets, like Target and Walmart, have followed suit by introducing specialty food & beverage aisles and displays featuring a wide range of organic and country-focused products.
This uptick in consumer driven demand for premium products has put pressure on the food & beverage industry to deliver products sourced from across the map that are fresher, made from natural ingredients, and certified cruelty-free. Free from artificial preservatives, these products come with far shorter shelf lives and lower tolerance for prolonged exposure to varying environmental conditions of temperature, humidity, (ultraviolet) light, and elemental oxygen. This has led to an emergence of technologies that offer finer grade product controls and improve overall supply chain flexibility and responsiveness in order to satisfy emerging product quality and safety specifications. Ensuring real-time temperature and climate control throughout the entire cold chain from production to retail is quickly becoming the new normal.
A Challenging Regulatory Landscape
Complicating matters, industry stakeholders are experiencing increased regulations resulting from implementation of the Food Safety Modernization Act (FSMA). These stakeholders include every participant in the cold chain including: growers, production mills, packagers & bottlers, import & custom authorities, distributors, shippers, and retailers. Currently, navigating regulatory hurdles involves a tedious, largely manual, document trail to ensure end-to-end product traceability from farm-to-fork. At each hand-off point, numerous quality checks are required to guarantee product integrity and ownership transfer between stakeholders as the product moves through the chain. Any mistake along the way can result in product recalls, which can have adverse effects: negative publicity, government penalties, productions delays, downtime, and even class-action lawsuits. In order to maintain a competitive advantage in this dynamic industry, cold chain partners must establish a level of visibility to streamline and optimize production, storage and distribution workflows, all while staying within strict regulatory bounds.
A fluid and shifting regulatory landscape is still a sore point for the majority of stakeholders across the cold chain. Increasingly stringent quality standards, a sharp increase in the number of foreign suppliers, and FDA-imposed requirements are introducing new supplier management, compliance, and traceability challenges in the industry. Implementation of FSMA rules are putting pressure on the food & beverage cold chains to tackle these critical issues. For example, refrigerated warehouses and shipping containers must maintain as many as five different climate zones to satisfy the strict temperature requirements.
The effects of globalization only make the regulatory landscape more complex. Increasingly, foreign suppliers are becoming a larger component of the food & beverage industry, making supplier management, sourcing, and quality a top concern. The old adage ‘quality in quality out’ couldn’t be more relevant. As products and raw materials move across cold chain, participants, importation requirements and compliance constraints demand detailed record keeping at each point in the process, and paper-based record keeping only exacerbates the need for technologies that offer proactive traceability solutions.
Product recalls will inevitably escalate as Food and Drug Administration (FDA) enforcement strengthens around FSMA regulations. To avoid potentially brand-damaging recalls, companies are investing in industry-centric technologies to automate the numerous quality checks along the cold chain, document plant maintenance and safety, and cultivate transparency among suppliers and producers to provide traceability.
Actualizing Comprehensive Visibility
Given the nature of the perishable food & beverage industry, dynamic supply chains are exposed to increased risk of quality and compliance issues. Often times, products experience short lapses in temperature or time control that are not immediately detected or obvious upon inspection. This results in potential of spoilage at various points along the chain and may even lead to product recalls.
Achieving location and condition visibility of perishable products from grower to consumer is critical to addressing these risks This level of visibility requires gathering real-time operational data at each point in the production and distribution process, and providing actionable intelligence to each stakeholder in the chain, from grower-to-grocer. What is grown is as important as where it is grown. What is processed is as important as how it is processed. And what is tracked and monitored is as important as how it is tracked and monitored.
Industrial Internet of Things (IIoT) technologies provide out-of-the-box connectivity and real-time data across the cold chain to identify product contamination or degradation. The collection of sensors, devices and systems are smart-enabling reusable containers of raw materials and goods to provide intelligent tracking, monitoring and management capabilities. These end-to-end visibility solutions are pivotal to offering high quality user-experiences, where consumers increasingly demand detailed information on ingredients of their premium product purchases, including traceability back to the point of origin. Maintaining competitive advantage in the global food & beverage industry is predicated on ensuring reliable product quality, full compliance, and end-to-end transparency.
Case In Point: Real-World Pain Points in the Olive Oil Industry
Consider the tightly regulated olive oil industry, where global suppliers prevail and history of fraudulent production is the new normal. Transactions must be documented to help track the transit of olive harvests as they move from growers to production mills, bottlers and then to packaging facilities for global distribution. This is a cumbersome, manual system which includes as many as five different quality checks, yet an estimated 70% of the olive oil sold in the United States is either counterfeit or contaminated in some way.
Lack of reliability in the olive oil supply chain is largely due to stringent logistics and storage requirements. Proper storage of olives prior to processing at the production mill is critical for producing high quality oil. Many production mills have a predetermined, inflexible capacity for processing, which means dwell time before and during the milling phase is a key concern for producers. The main issues during processing relate to temperature, hygiene, and processing time. While it’s relatively easy to control these critical factors during the processing phase, it’s a different story when auditing the oil at packaging facilities, shipping docks, or distribution centers. Product recalls happen frequently in the olive oil industry as a result of limited product visibility and traceability, damaging the product’s overall reputation.
IIoT to the Rescue
Let’s look at how an IIoT-enabled approach to monitoring the location and condition of olives alleviates the pain points of supplier management, compliance, and traceability in the chain.
IIoT sensors and devices trace olives at the point of origin, where the growers determine post-harvest dwell time to confirm product viability as soon as olives arrive at the mill. Excessive storage dwell-times trigger an automated notification, informing operation managers to examine the state of the harvest and either accept or reject the batch. This new level of visibility keeps growers on their toes by holding them accountable. Growers with a history of consistently mismanaging their harvest gain a reputation as poor quality suppliers. On the other hand, when a good batch of olives hits the production floor, detailed specifications are monitored and fine-tuned during the processing phase. This transparent approach of monitoring the state of olives incentivizes each stakeholder to improve operations of their part in the cold chain. This cycle of positive behavior reinforcement improves overall product quality over time.
In the operational technology (OT) domain, sensors stream real-time data from the edge of the supply chain to cloud analytics, providing valuable insights to growers, operations managers, and logistics companies on ambient environmental conditions, dwell-times, physical shock, temperature, humidity, tampering and a host of other related metrics. These edge-to-cloud data flows are critical for proper auditing and regulatory compliance as olives move from one phase to the next on their journey to becoming fine olive oil. Each touch point in the cold chain presents a potential weak-link. Stakeholders can minimize the scope of product recalls by identifying single points of failure and isolating specific batches or containers of problematic olives to reduce compromising the entire production run.
IIoT represents the collection of enablement technologies to provide end-to-end visibility and enable granular tracking, monitoring and traceability of perishable products. Even with strict regulations challenging cold chain partners, these distributed IoT technologies give operation managers, shipping providers and distribution centers the tools necessary to optimize production and exceed the industry’s regulatory benchmarks. In the end, a data-driven approach that bridges the OT domain with the back-office IT systems offers the missing ingredient in the cold chain.
The Cloudleaf Solution
Cloudleaf is an IIoT solution for monitoring, managing and monetizing distributed-asset ecosystems across cold chains in the food & beverage industry. Cloudleaf’s value-proposition embodies the paradigm shift in IoT adoption and usage across internal and third party facilities to effectively sync up the chain from end-to-end. Cloudleaf’s Sensor Fabric™ mesh of sensors, gateways and cloud services represents a targeted approach to providing managers enhanced visibility into their operating technology in order to actualize synergies and optimize production throughout the cold chain, delivering real value for suppliers, producers, and carriers in the food & beverage industry.