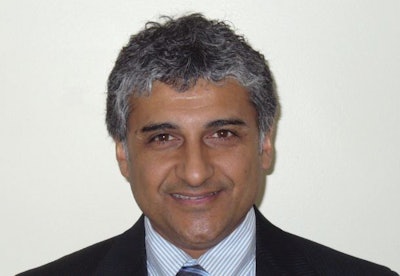
Previous authors of this column have pointed out the necessity for tighter integration of the food chain, the need for collecting key data along the supply chain for traceability, and the various technologies that are available to measure, collect, aggregate and distribute data for risk prevention and shelf life predictions. Furthermore, the FDA recently announced that it will carry out pilot studies to explore methods and data standards for rapid and effective tracking and tracing of food. The question that comes to mind is where to start? How do we design tightly integrated food chains and how do we communicate these specifications? Or in the case of FDA, how to design and conduct the pilots? How to compare two food chains? How to identify the risk points in the food chain?
At Georgia Tech’s Integrated Food Center, we have been studying various ways of representing and modeling the food chain that incorporate both process and data standardization to provide a means to answer the above questions. The result is FIRM, Food Integration Reference Model, a three-level hierarchical model for modeling, designing, communicating, and evaluating the food chain.
Supply chain view
At the top level of this framework is the supply chain view that describes each of the multiple entities or sites that participate in the chain. These can be producers, packers, transporters, processors, distributors, and retailers. For each site, its name, identifier, address, products and other key information are stored. Information on the possible links between each site is also kept at this level. The supply chain view shows how the product moves through the food chain, from its origin to its destination. It gives the time spent in each site and in transit, and the conditions under which it is shipped.
Site view
This view shows the main processes that touch the product as well as the main types of product movement within the site and from the site. The processes include receiving, put-away, picking, processing, packaging, loading, and shipping. Product movement includes: move, store and transform. A product movement is a result of one of more processes and may in turn trigger other processes. They consume time and, depending on the product, will require special considerations such as specific temperature range or special handling equipments. The site also specifies how products are shipped on each of the links such as ship in a reefer container at specified temperature and ventilation level. Product data and data formats for lot, batch number and product mix are maintained at the site level.
Process view
The process view gives the details of the main activities involved in each of the key processes that touch a product at a site. For each activity, it specifies the average time taken, the resources and equipments that are required as well as the documents or information that are collected or generated. It gives the specification for process execution and coordination, enforces data standards and data collection points, and allows computation of low level metrics. For example, the time for each type of product movement can be computed and the condition of the product documented. Hence, it is possible to know the total time a product spends in a site and the details on where and in what conditions it was spent. Data on when lot and batch numbers are to be captured and the lot numbers that go into a product mix are maintained at the process level.
The process layer allows documentation of waste and risk points at the activity level and enables the implementation of a HACCP (Hazard Analysis and Critical Control Point) plan.
Systemic view
Metrics computed at the process level can be aggregated at the site level and then at the supply chain level for a systemic view of the food chain. It is now possible to answer questions such as: What is the average time from farm to fork? Where are the major risk points in the food chain? What should be done to improve safety and reduce waste? It also possible to conduct gap analysis or study the impact of implementing a new technology such as RFID (radio frequency identification) tags at the operational level.
Benefits of a reference model
One of the main advantages of a reference model is that it provides a common language that facilitates communication, specifications, and benchmarking. The FIRM framework was developed to conform to this objective. It can be used in many ways: in a descriptive mode to document the processes and product movements at each site and between sites; in a prescriptive mode to specify the standards and specifications to be used for processes and product movements to maximize shelf life, minimize waste and minimize risks; as a means of enforcing data collection points and the monitoring of key performance indicators along the supply chain.
Computer implementation of FIRM for a particular food chain allows simulation of a recall and trace back. This is a major advantage when studying various configurations and data implementations and is less costly than actual pilots. When coupled with a data collection layer, the metrics can be used in a dashboard to compare planned with actual data, providing the basis for predictive analysis and traceability.