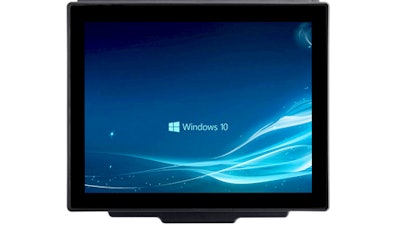
Whether you run a warehouse for manufacturing, retail, shipping or storage, every second counts. The 21st century is all about speed and no waste. Customer expectations are increasing, the supply chain is transforming and technology continues its unrelenting evolution. On top of this, there’s the pressure to increase throughput, reduce inventory cycles, hit increasingly tougher targets and generate even higher profits.
Against this backdrop of ever-escalating internal and external demands, it’s paramount that your warehouse operation is performing optimally. But, productivity has many facets – mobile technology being one of them, presenting four major challenges for the efficiency of warehouse operation—connectivity, hardware breakdowns, unengaged workers and inflexible technology. The good news is, there are several actions you can take to combat these challenges.
Secure good connectivity
For any warehouse, 100% connectivity is the pot of gold at the end of a rainbow. To get your hands on this treasure, you need a robust wireless infrastructure with seamless roaming from one access point (AP) to another at the speed of a forklift. But, in a vast building with changing contents, it’s not that straightforward.
Whenever upgrading or even just maintaining your wireless network, you should bring in external, independent experts who can give objective advice about the best WiFi design and equipment for your set up. Involve your internal network people too. Having several viewpoints can sometimes uncover some previously unthought of solutions.
Take a good look at your APs to check they are sited at the optimal locations. The best way to do this is to complete a network survey that will quickly discover any hidden dead spots or other problems.
Don’t forget to plan for your inventory as well as your set up. Stock levels fluctuate and different materials can affect signals in different ways – steel shelving or metal cages deflects; wood, liquids, or clothing absorbs; and concrete totally blocks.
Finally, there’s another element to connectivity that doesn’t concern your network. It’s your devices. Ideally you will run rugged devices featuring dual antennas. Having two antennas enables the unit to pick up the strongest available signal. This results in a more stable connection, without interruptions, in every corner of the warehouse.
Minimize the impact of computer breakdowns
Unfortunately, technology has not yet reached the point where we can build an infallible computer, so your devices will break down. But, despite not being able to avoid failures entirely, you can still reduce the frequency and the time it takes to fix them.
Purchase devices built specifically to survive the demanding environment of a warehouse. Dust, moisture, vibrations, and changes in temperature are all common conditions that will make consumer-grade devices fail quicker than truly rugged devices. And, watch out for devices that are just an average tablet dressed up with rubber corners that might not be up to the job.
When evaluating rugged devices for your business, make sure you choose high-quality products and consider the total cost of ownership (TCO) rather than just the upfront price tag. To calculate TCO, consider all costs that occur during the lifetime of the product – for example cost and frequency of breakdown, service and repair, and last but not least, the cost of loss in productivity. By doing this, you reduce the risk of buying equipment that seems affordable at first and then ends up surprisingly costly, at a point when there’s nothing you can do about it.
Buying high-quality, fit-for-purpose devices vastly reduces the frequency of computer breakdowns. But to fully minimize the impact of lost productivity, make sure you have a good process in place that kicks in when issues arise. One way to do this is have swap out units on site, fully charged and ready to go in case a device fails. Then, have a plan in place to troubleshoot devices remotely.
And, it’s not just quality of devices you should look for. Working with a quality partner who can provide a solid service contract and guarantee the availability of spare parts is just as important.
Engage and motivate employees
Engaged and motivated employees can help your productivity improve. Make them feel valued and provide them with the right tools to do their job to stop them clock-watching and struggling with technology.
The first thing you can do is to involve them. Your workforce is a potential mine of information that can help you boost your productivity. They know your warehouse and their jobs back to front, so they can highlight inefficiencies that you may not have considered before. Ask them what they think and listen to what they say.
Secondly, combat resistance to change by engaging them in the process. For example, when you’re procuring new tablets or vehicle-mount computers they can help set requirements, test potential new devices, and onboard other members of staff.
And finally, give them the right tools that help them do their jobs. A fit for purpose device that’s built for the warehouse environment means they have a tool they can depend on. A fully locked-down device with a custom image means they stay on track with their tasks. Tailor-made shortcuts save time. Up to date software will appeal to the tech-savvy and bigger screens can help the more mature members of your team.
Inflexible technology
Technology is designed to help. But, inflexible technology turns into a hindrance. Old, incompatible, or not fit-for-purpose devices slow down workers as they try to find workarounds or waste time trying to get things to function correctly.
Make sure your warehouse is running genuine rugged devices. Consumer-grade kit and many semi-rugged computers are not built to withstand the harsh environment of a warehouse. Rubber corners or a slightly tightened housing do not go far enough in most cases. Buy from a reputable company with a track record in supplying warehouses, to ensure you procure equipment that not only speeds up your workers, but also reduces errors.
Get your hardware and software customized for your operation. Functions and onscreen shortcuts can save valuable time and stop your workforce becoming frustrated. As mentioned before, custom imaging keeps employees focused and only lets them access the information they need to do their job.
Finally, update hardware when needed to reduce incompatibility problems, slow devices, and computer breakdowns. Software updates should only be performed when required, such as security updates.