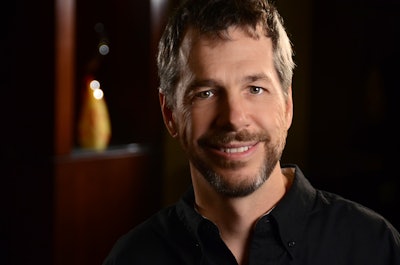
Moving from handmade products to assembly lines, mass production and computerized systems, the manufacturing industry has continuously evolved to find better and faster ways to push products out the door. Today, we are in the middle of a digital transformation called Industry 4.0, wherein cloud computing, the Industrial Internet of Things (IIoT) and cyber-physical systems are melding to create smart factories of the future.
These factories connect a menagerie of advanced digital and manufacturing tools and systems, such as smart devices embedded with sensors, robotics, process control systems, self-operating vehicles and more via Wi-Fi networks and the internet to improve efficiency and optimize production. They run with minimal human intervention. Not lights-out production, but operations with smart components that can autonomously make adjustments based on the data collected from the plant floor. With less human intervention at this level, there are fewer defects and errors, resulting in higher quality products and increased customer satisfaction.
Beyond the factory floor, Industry 4.0 enables quality professionals, C-level executives, VPs, and plant managers to make better, data-based decisions about overall operations. If a production line in a carbonated beverage facility has refined its target fill amounts to not only be within specification limits, but also to reduce overfill, this best practice can be identified at the corporate level and replicated across all facilities to maintain product consistency and minimize waste.
According to The Boston Consulting Group’s recent report, Sprinting to Value in Industry 4.0, “The value created by Industry 4.0 vastly exceeds the low-single-digit cost savings that many manufacturers pursue today. The new technologies promise to revolutionize manufacturing, thereby shifting the competitive balance among countries and transforming the industrial workforce.”
While adjustments on the plant floor can amount to incremental cost savings, imagine what that would mean if that same change was made across operations with dozens or hundreds of plants. For instance, a leading North American consumer packaged food and beverage company implemented quality management software with a centralized database to collect, analyze and monitor data in real time for three of its plants. The company was able to react to variances and out-of-spec issues as they arose and quickly make adjustments to prevent scrap, reduce “giveaway” and maintain a consistent taste profile. This one initiative resulted in a $2.1 million annual, sustainable improvement in savings due to waste reduction. Extended to its more than a dozen plants, the annual improvement in savings approaches $10 million.
The foundation of Industry 4.0 is automation and data exchange. However, a recent survey by InfinityQS of 260 manufacturers, including some of the world’s largest manufacturing organizations, found that 75 percent of respondents still are manually collecting data. Worse yet: 47 percent of those rely on pencil and paper.
To achieve the digital transformation that Industry 4.0 promises, manufacturers must put down their clipboards, and automate their data collection processes. And the data can’t just get dumped and lost in local, siloed databases after it’s collected. Implementing a cloud-based quality management system centralizes data collection in a secure, reliable hosted environment, without the need to “rip and replace” existing hardware at individual locations.
Once data are unified in a centralized repository that is accessible to all stakeholders within the organization, it’s possible to visualize more than a single aspect of operations. The outcome is real-time visibility of the entire enterprise, from end-to-end, including suppliers, incoming inspection, ingredients, in-process checks from shop floor operators and the quality lab, process data, packaging, and finished products. This enterprise visibility identifies potential opportunities to increase output, decrease costs and improve quality across manufacturing operations.
A transformation of this magnitude can be daunting. Luckily, Industry 4.0 isn’t an all or nothing proposal. Food and beverage manufacturers can take a more iterative and agile approach to adopt Industry 4.0 components at a pace that is better aligned with their financial and human resource capabilities. Starting with a single system (like a quality management system) that unifies data in a centralized database can provide enterprise visibility, so companies can better understand and optimize operations while determining the next step in the overall digital transformation.
While digital transformation can be executed in a phased process, it’s important to realize that manufacturers around the world have already begun the process to adopt Industry 4.0. The German government included it in their strategy to computerize manufacturing nearly five years ago, and in 2014, Cincinnati mayor, John Cranley, declared his city to be the “Industry 4.0 Demonstration City.”
Time’s up for old, manual manufacturing practices. Manufacturers must put down their pencils and take the steps necessary to adopt Industry 4.0 or be left behind in the dust of competition.