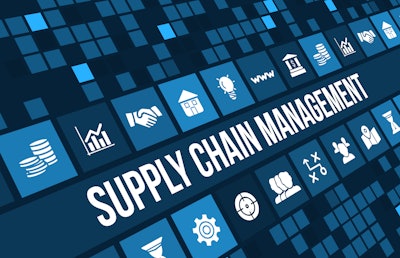
In food and beverage manufacturing, there’s a common saying: "If it ain’t broke, don’t fix it." While this mindset might apply to some aspects of the industry, it rarely pertains to manufacturing equipment, which is often “state of the art” and essential to maximizing output in a low-margin environment. Yet, when it comes to adopting advanced technologies like Industry 4.0 and other innovations, food manufacturers are slower to embrace change, relying on current systems that seem to function “well enough.”
Beneath the surface, many supply chains show signs of strain – from inefficiencies to hidden costs and untapped opportunities. While everything may look smooth at face-value, a closer look at processes, people, and systems can reveal critical gaps where technological investment can make a meaningful impact. The reality is that many supply chains are broken, even if it’s not immediately visible.
1. Demand planning: The hidden chaos of forecasting errors
Accurate demand planning and forecasting are essential to meeting customer expectations, reducing waste, and managing costs for food manufacturers. Though the industry presents unique challenges like fluctuating demand, seasonal trends, and the perishable nature of food products make forecasting particularly complicated.
Identifying the problem: Inaccurate assumptions and broken processes
The root cause of issues often lies in outdated or inaccurate demand planning, which may rely on incomplete data, manual processes, or limited forecasting tools like spreadsheets. These outdated methods can lead to inaccurate forecasts, ultimately resulting in either overproduction or underproduction. For example, a manufacturer may produce more of a product than needed, leading to spoilage and waste, or fail to meet demand, risking stock outs and lost sales.
Solution: Advanced demand planning software
To overcome these challenges, food manufacturers can adopt advanced demand planning software that leverages historical data, real-time market trends, and sophisticated algorithms to forecast demand with far greater accuracy. This software integrates data from various sources—including point-of-sale information and predictive analytics—to build a clearer picture of customer demand allowing food manufacturers to avoid both shortages and excesses.
Real-world example: Reducing excess in dairy manufacturing
Consider a dairy manufacturer that frequently overproduces milk, leading to high spoilage rates and wasted product. By implementing an advanced demand planning system that incorporated point-of-sale data and predictive analytics, they aligned their production levels more closely with actual demand. This transition helped reduce excess inventory by 15%, minimizing spoilage and better matching production to market needs.
2. Procurement planning: Invisible supply chain disruptions
Procurement is the backbone of any manufacturing operation, ensuring that raw materials like ingredients and packaging supplies arrive on time to meet production needs. Yet, many manufacturers operate under the assumption that their supplier relationships and delivery schedules are rock-solid. When occasional material shortages or delayed shipments occur, they’re often dismissed as isolated incidents rather than symptoms of a deeper issue.
Identifying the problem: Procurement planning breakdowns
These disruptions often stem from a lack of robust procurement planning. Without a system that ties procurement to demand forecasts and inventory levels, manufacturers risk ordering materials too late or in insufficient quantities. This misalignment leads to production delays, rushed orders, and increased costs as teams scramble to secure last-minute supplies.
Solution: Integrated procurement planning systems
Food manufacturers need procurement planning systems that integrate seamlessly with demand forecasting and inventory management tools. These systems provide real-time visibility into supplier lead times and inventory levels, enabling manufacturers to create dynamic procurement schedules. With better planning, raw materials can be ordered at the right time and in the right quantities, reducing the risk of stockouts and supply chain firefighting.
3. Optimizing production scheduling: Turning hidden inefficiencies into opportunities
Many food manufacturers assume their production lines are running at full capacity simply because output numbers appear satisfactory, but in reality, inefficiencies like frequent changeovers, unplanned downtime, and inconsistent production speeds often go unnoticed, quietly limiting potential gains.
Identifying the problem: Inefficient production scheduling
These inefficiencies usually stem from inadequate scheduling processes that fail to consider real-world constraints, such as machine capabilities, material availability, and labor shifts. Without a robust system, production lines can become either underutilized or overburdened, leading to wasted resources and suboptimal performance.
Solution: Finite capacity scheduling systems
Manufacturers need scheduling systems that leverage real-time data to create optimized production plans. Finite capacity scheduling systems reduce changeover times, maximize available capacity, and adapt dynamically to disruptions, such as equipment breakdowns or unexpected order changes. This approach ensures a more efficient, reliable production process.
Real-world example: A beverage manufacturer cuts changeover times
A beverage producer struggled with extended changeovers, which increased production downtime by 20%. By implementing a finite capacity scheduling system, they streamlined scheduling processes, cutting changeover times by 40%. This improvement enhanced overall line efficiency, enabling the company to better meet customer demand while reducing operational stress.
4. Inventory management: The silent cost of overstocks and stockouts
Effective inventory management is essential, yet many food manufacturers assume their inventory is under control, even when facing occasional stock outs or excess inventory. These issues are often viewed as unavoidable rather than symptoms of a deeper problem.
Identifying the problem: Ineffective inventory management
Inventory imbalances typically stem from outdated or inefficient management processes. Overstocking ties up valuable capital, increases storage costs, and can lead to spoilage, while stock outs disrupt production and create missed sales opportunities. Without a system to balance these flows, inventory misalignments become costly and disruptive.
Solution: Inventory optimization tools
Inventory optimization tools, integrated within supply chain planning systems, enable manufacturers to dynamically manage stock levels. These tools automate reordering processes, adjust safety stock based on real-time demand, and maintain optimal inventory flow, reducing waste, cutting costs, and ensuring product availability.
Real-world example: Reducing spoilage in a bakery operation
A bakery frequently overproduced due to inaccurate inventory counts, resulting in high spoilage costs. By implementing an inventory management solution, they achieved a 30% reduction in spoilage, freeing up working capital and allowing them to reinvest in business growth.
5. Logistics and distribution: The bottlenecks you didn’t know existed
There are indications of hidden inefficiencies that can erode profitability and disrupt supply chain reliability in most all logistics operations, even those that may seem efficient if deliveries are mostly on time and customers complaints are rare. Rising freight costs and occasional delays have traditionally been dismissed as external factors, but even these are inaccurate assumptions.
Identifying the problem: Inefficiencies in logistics and distribution
Hidden bottlenecks in logistics often stem from suboptimal practices like inefficient route planning, poor warehouse management, and insufficient shipment consolidation. While these issues may not immediately impact day-to-day operations, they can significantly inflate costs and strain distribution networks over time.
Solution: Advanced logistics planning tools
Logistics planning software enables manufacturers to optimize delivery routes, consolidate shipments, and improve warehouse operations. When manufacturers streamline these processes, they can cut transportation costs, enhance delivery times, and elevate customer satisfaction.
Real-world example: Reducing freight costs for a meat processor
A meat processing company struggled with increasing freight costs and late deliveries to grocery chains. After adopting logistics planning software, they optimized delivery routes and reduced transportation costs by 15%, with fewer late deliveries.
Fixing what you don't know is broken
In the food and beverage industry, the adage "if it isn't broken, don't fix it" often prevails. While this mindset may offer short-term reassurance, it can obscure underlying inefficiencies that hold businesses back. Processes and systems that once worked well may have become outdated or inadequate, leading to missed opportunities, hidden costs, and declining productivity without being immediately apparent.
Manufacturers must shift their focus from reactive problem-solving to proactive optimization. Regularly evaluating people, processes, and systems is essential to ensure that daily operations not only function but excel in driving the business forward.
Advanced supply chain planning tools – such as demand planning, procurement, planning, finite capacity scheduling, and logistics optimization – enable manufacturers to identify and resolve shortfalls before they escalate. When manufacturers leverage these tools they can enhance agility, resilience, and efficiency, positioning themselves as adaptive enterprises capable of thriving in a rapidly changing market.
The cost of waiting until something visibly breaks can be steep, from missed sales opportunities to damaged brand reputation. Manufacturers must embrace innovation and continuous improvement to remain relevant and competitive. It's time to dig deeper, uncover what is truly broken, and take the necessary steps to fix it.