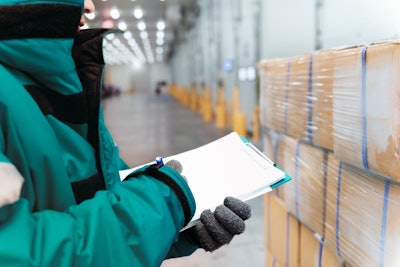
Refrigerated trucks and trailers play a vital role in the food supply chain, hauling perishable items and transporting fresh and frozen goods from producers to distribution centers and then to grocery stores, restaurants and institutional facilities. They’re used routinely to make on-time deliveries and keep commodities safe at controlled temperatures.
Over the past two years, as the Coronavirus disease (COVID-19) pandemic has brought about new supply chain challenges, the refrigerated trucking industry has continued to fulfill its essential role. Driving that success-- away from the bright spotlight that’s been on refrigerated supply chain issues-- have been dedicated professionals in back offices and on the road who have implemented better operating practices and the use of state of the art technology.
There are common issues that can arise in refrigerated transportation operations, and which technology and effective operations can address:
- As much as 32% of all refrigerated cargo is loaded at the wrong temperature. That is often due to poor loading practices, for example, when produce is left sitting at a loading dock for a long period of time.
- Equipment breakdowns are a fact of life, and when a refrigeration unit fails unexpectedly the potential for the entire shipment to spoil rises quickly.
- Driver errors occur because configuring refrigeration unit temperatures can be a complicated task. Being familiar with the operation of reefer systems is something they need to do on top of their primary responsibility for safe and timely vehicle operation.
- Even before a refrigerated load is dispatched, incorrect documentation and inaccurate load data can jeopardize the cargo.
Beyond those issues, the temperature-controlled freight supply chain is a rapidly changing environment. Failing to meet ongoing and new challenges can lead to rejected loads and costs for cargo claims and insurance, not to mention equipment, fuel and driver expenses. Worst of all may be the long term effect of spoiled loads on a company’s reputation and its customer relationships.
So, how prepared are you to ensure the integrity of the refrigerated freight you’re hauling? More importantly, perhaps, how can you mitigate the potential for costly lost loads?
Part of the answer for successful refrigerated food transportation operations stems from their use of advanced reefer monitoring systems. These solutions ensure that cargo temperatures stay within an acceptable range and provide real time alerts if changes occur. Additionally, their remote monitoring and control capabilities can be used to verify temperatures and proper operation, protecting cargo and taking the responsibility off drivers.
Premium reefer management solutions use manufacturer protocols to enable a higher level of seamless, two-way access to the refrigeration unit. That allows users to set and adjust temperatures as well as initiate processes such as pre-cooling cycles. These solutions differentiate themselves by ensuring the accuracy of temperature readings compared to lower cost alternatives, which can be inaccurate.
And they have other benefits beyond minimizing temperature-related problems. Their reporting features, for example, can reduce dwell times and optimize reefer performance. Easily integrated with industry leading transportation management systems they can facilitate better route and load planning, decrease fuel use and lower maintenance expenses.
Not to be overlooked is their value in this highly regulated industry segment. Their ability to automate compliance with the U.S. Food Safety Modernization Act (FSMA), the Safe Food for Canadians Regulations (SFCR) and other food safety regulations ensures that stringent requirements on food transporters for pre-cooling and in-transit temperature monitoring, as well as data collection and recordkeeping are met consistently and correctly.
Deciding on the right reefer management solution requires planning. From the tracking device to the web interface with dispatch system to analytics and reports, there are many aspects to consider. Most importantly is the ability to justify your choice by determining a return on investment (ROI).
In general, there are five keys areas for potential savings that can be facilitated by a reefer management solution:
- Reduced fuel consumption stems from eliminating unnecessary continuous usage by enabling reefers to operate in start/stop mode. Some estimates are that switching to a start/stop solution can reduce fuel use by as much as 50%. Another source of fuel savings comes from detecting extended reefer operation, for example if a shipper cools the trailer, loads it partially and then leaves the unit running until it is fully loaded.
- Reduced service costs come from performing preventive maintenance when it’s required, not too early or too late, by using the system to track accurate reefer unit engine hours and trailer mileages.
- Reduced labor costs are possible by eliminating the need to have personnel assigned to turning on reefer units in advance of loading or changing temperature set points. With remote reefer activation and checks, two-way communications can handle those tasks effectively.
- Reduced cargo claims can result from identifying temperature set point mismatches between load and order requirements and the actual trailer temperature. Fewer trailer thefts are possible with trailer lockdown features and local geofenced location monitoring as well. In both cases, these risks are greatly reduced when personnel can be notified immediately if cargo temperatures are too low or too high or if a trailer is moved without authorization.
- Reduced dwell times can be realized with the ability to quickly track the location of refrigerated vehicles and pinpoint ones that have been idle for too long. Reports on dwell time and utilization lower fuel and driver costs and improve productivity, allowing you to increase revenue and improve profitability.
One of the biggest technology developments in the past few years for reefer monitoring systems also helps drive a faster ROI. With advanced communication systems, including expanded cellular networks and satellite systems, carriers can utilize dual mode solutions to connect with their vehicles across North America at all times and at the lowest cost. Complementing that benefit are lower cost data plans, enabling the transfer of more information more frequently.
There’s no question that reefer monitoring and control are among the keys to ensuring the timely transportation of food and cargo integrity. Increasingly as well, they are a necessity for meeting regulatory requirements, and the real time visibility into load location and status needs of shippers and receivers.
By investing in reliable, advanced and comprehensive reefer monitoring technology, leading temperature-controlled freight carriers are safely and productively delivering food goods to customers. In turn, they too can improve the efficiency of their supply chains.