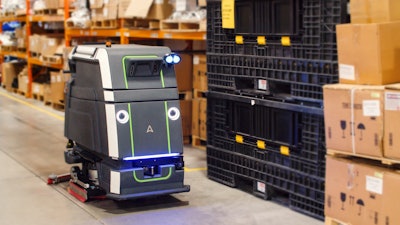
The cleaning needs of food processing and consumer packaged goods facilities are like no other. Around-the-clock shifts with equipment constantly kicking up dust and debris make for a challenging environment when it comes to facility cleanliness and safety.
Consider this: the second largest area of a facility is the floor, second only to the ceiling. The reality is that everything falls on the floor, making it ground zero for dust, dirt and debris. Depending on the size of the facility, the floor can become filthy within hours. Next, consider just how many moving items kick up dust and dirt from the floor: carts, forklifts and workers themselves. It’s a recipe for a disaster.
Quality food products and healthy workers start with a clean facility. With global supply chain issues and labor shortages plaguing the industry, cleanliness has never been more important when producing, distributing or purchasing food and consumer packaged goods.
Food safety: A myriad of challenges
Manufacturing and distribution facilities are built for efficiency and ease of moving materials, with very little thought given to cleaning convenience. Hard-to-reach areas, tight corners and large areas requiring cleaning have become commonplace. However cleanliness is paramount to facilities; one simple cleaning slip-up could contaminate the product on hand. Making matters harder, dust and debris particles are unavoidable by-products of the manufacturing process. Consumer manufacturing facilities require tough, industrial-level scrubbing.
Likewise, in 24x7 production settings, shift employees are constantly coming and going while equipment is always on. Without frequent cleaning, it doesn’t take long for facilities to become untidy which can affect productivity and safety.
Finally, employee health and safety is no easy task in a bustling food facility. Dust exposure, biological viruses, flammable debris and slip hazards are all common dangers that must be mitigated to maintain a safe and healthy workplace.
Add this all up, and it’s a burden for facility managers to ensure all areas are cleaned regularly—not to mention scheduled and tracked. And that was before a global pandemic stepped on the scene.
COVID-19 complications stress staff and supply chain
Facility managers are facing staffing and supply chain challenges of the likes never seen before. Facilities are forced to move available staffing to production lines to make sure they are putting products on shelves and in the hands of customers. Moving workers to more production-oriented tasks can mean less manpower for cleaning. While that might make ends meet in the short run, it poses a problem when a product becomes contaminated or an inspection fails because of an unclean facility.
When it comes to the Great Resignation, facility cleaning jobs rank low on the list of desirability. Custodial jobs are hard to fill – they are often the last to staff and the first to be open. In fact, employee turnover averaged around 200% pre-pandemic. With so many facilities facing worker shortages, that sets up the likely scenario that the same individual driving a forklift or on the production lines might be pulled in to operate a manual walk-behind or ride-on scrubber.
When facilities are under pressure to get product in or out the door, something has to give, and it’s not the forklift driver or production worker. Positions that affect the intake and output of a product will always be prioritized over cleaning operations, but at what risk? Failing any sort of inspection is problematic enough pre-pandemic; failing an inspection now can seal the fate of a factory already dealing with labor and production shortages.
For facility inspections – particularly post-pandemic – it’s no longer good enough to show manual logs or binders of daily cleaning sheets. Safety managers need documentable, verifiable proof that something that was supposed to be done was actually done. When cleaning with a manual solution, it’s difficult to quantify or qualify what was cleaned, when it was cleaned, how well it was cleaned and by whom. Additionally, it leaves room for human interpretation and error.
Autonomous solutions provide relief and results
Forward-thinking manufacturers are turning to autonomous cleaning solutions to realize operational efficiencies, meet heightened cleaning standards and improve worker safety. Featuring smart artificial intelligence (AI)-driven navigation, easy operation and a host of manufacturing-specific benefits, floor-scrubbing autonomous mobile robots (AMRs) represent the next phase of innovation on the factory floor.
Consistent, around-the-clock cleaning can be achieved through autonomous solutions that don’t require around-the-clock human support. Moreover, robots provide a more consistent, efficient and measurable clean.
With a robot cleaning expansive facility floors, management can assign labor to the most valuable tasks while reducing employee injuries and absences due to repetitive strain and fatigue, a critical need amongst some of the worst labor shortages seen in decades. Likewise, a clean facility helps ensure food production stays on task and is completed without contamination, as well as keeps existing labor safe and healthy; two critical components of maintaining facility efficiency and output during supply chain issues.
Finally, AMRs eliminate any challenges or time spent by safety managers providing documentation of a facility’s cleanliness. A digital cleaning report can be at the ready any time, showing what was and wasn’t cleaned down to the inch and why. Hard-to-quantify cleaning efforts suddenly become concrete, making routine cleaning reports or annual inspections go faster and smoother. Cleaning is no longer an issue of trust – it’s a definitive and documentable process.
Investing in robots isn’t just a new way to clean. It’s a way to solve staffing and supply chain shortages. And in the long run, it’s investing in a technological future that can redefine your cleaning function, making it more productive, more cost-effective and easier to run.