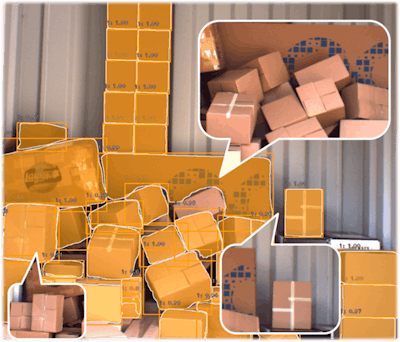
Labor challenges are impacting nearly every global industry, including food processing and logistics. According to The Conference Board, “the U.S. economy alone needs 4.6 million additional workers (2% of its population) per year to maintain current levels of supply, demand and population balance.”
Elsewhere, Germany needs 1.6 million (3%), South Korea needs 2 million (5.5%), China needs 47 million (5%). These numbers suggest labor may be the single biggest, most-persistent threat to businesses and the global supply chain.
The dull, dirty and dangerous jobs have proved among the most difficult to staff, including trailer and container unloading and receiving and handling of dry goods (ingredients) and other heavy bags. These jobs put a great physical and mental strain on workers, increasing the risk of injuries.
Neither the Occupational Safety and Health Administration (OSHA) nor the European Agency for Safety and Health at Work (EU-OSHA) limit maximum lift weights for workers, though the National Institute for Occupational Safety & Health (NIOSH) suggests a maximum of 51 pounds. That’s because lifting heavy objects at work comes with a number of health risks.
In 2022 (the most recent year of available data), nearly 600,000 occupational injuries treated in U.S. hospital emergency departments were the result of overexertion and bodily reaction, according to the Center For Disease Control and Prevention’s (CDC) Work-Related Injury Statistics Query System.
The U.S. Bureau of Labor Statistics reports for 2021-2022, Laborers and freight, stock and material movers incurred 166,100 reported injuries including sprains/strains/tears, fractures, cuts, lacerations, punctures, bruises/contusions, heat and chemical burns, amputations, carpal tunnel syndrome, tendonitis, and soreness/pain.
It’s no wonder these jobs are becoming more difficult to fill. The combination of demanding physical labor (heavy lifting, repetitive motions) and extreme working conditions (cold storage/shipping containers, cement loading docks, etc.), and increased competition for workers, essentially ensures people are seeking alternative employment.
Improving worker safety
To improve recruitment and retention, companies need to improve worker safety, and the fastest route is automating as many of the dull, dirty and dangerous tasks as possible. Leading companies are already implementing advanced automation solutions to ease the worker’s burden.
Trailer and container unloading is another example of especially dangerous work, with extreme heat and cold temperatures, poor visibility, uncomfortable and unstable surfaces, and the need to deal with objects that have shifted during transport. To date, these same variables have stymied automation of this task, but advances in computer vision solve these problems with the same three-step approach used for picking heavy objects: item identification, prioritization and precise picking instructions.
An oft-overlooked element in worker safety is reducing repetitive motions. Even light-duty tasks repeated for hours a day and weeks on end can cause significant and lasting injuries to workers. Repetitive strain injuries are common in hands and joints and can cause pain, swelling, tingling, numbness and stiffness, sometimes to extreme degrees. Tasks like salad kitting that include picking sachets and small food items and placing them in containers are perfect examples of the type of repetitive motions that can seem insignificant but can cause lasting harm after an extended period.
A traditional fear of automation is working displacement, which is understandable. However, automation isn’t about replacing human workers but complementing them. When it comes to dull, dirty and dangerous jobs, automated solutions protect workers, handling tasks that put workers in harm’s way and filling the voids created by ongoing labor shortages. Humans can let automation handle the heavy, repetitive and dangerous tasks, enabling them to focus on safer, and hopefully more rewarding work. Prioritizing worker safety and satisfaction can help reduce turnover and time off due to work-related injuries, ensuring greater continuity in times of global labor challenges. Companies who have faced constant turnover are well aware how expensive it can be to recruit and train a replacement for the departing employee (estimates vary, but 6-9 months of the departing employee’s salary seem reasonable). On top of which companies lose productivity, leadership and institutional knowledge, and more declines with each departure.
Automated solutions have different expenses to be sure but pay off by filling labor gaps, delivering consistent production, and keeping team members healthier and happier by handling the dull, dirty and dangerous tasks so workers don’t have to.