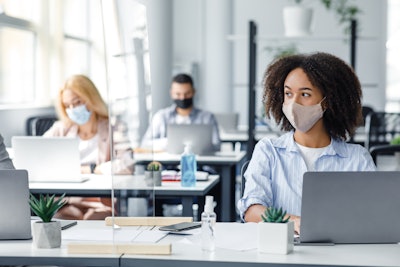
A combination of disruption to global supply chains and intensifying economic headwinds have resulted in a supply chain re-set.
Virtually every company is looking at their supply chains and assessing how to rebuild them to help ensure they are resilient enough to withstand further disruption. Many recall the ghosts of previous attempts at transformation and the ones that didn’t unlock the value that they set out to create.
Taking a closer look at the recent research by EY teams and the University of Oxford reveals that 75% of operations executive respondents chief operating officers (COOs), chief supply chain officers (CSCOs) and their direct reports have experienced at least one underperforming transformation in the last five years. It’s unsurprising that many are asking what they can do differently to improve the likelihood of success this time around.
The answer is to better understand and address human emotions. By paying more attention to the human factors that are often the root cause of transformation failure, COOs and CSCOs can increase their chances of a successful transformation to as high as 73%. Developing and implementing leading practices in the following six areas will put leaders in better position to succeed.
1. Lead: Practice courage, demonstrate curiosity and adopt a we not me mindset
Regardless of whether they have climbed the ladder within one organization or risen to the C-suite through a number of progressive roles across several organizations, COOs and CSCOs have an opportunity to improve their leadership skills by opening themselves up to new perspectives and ways of working. Displaying curiosity and looking at things from multiple perspectives is an essential skill, as is recognizing the limitations of your current mindset and capabilities. 52% of operations leader respondents say they understood the needs and views of the workforce versus just 32% of operations worker respondents who feel the same.
A servant leadership model creates time for every leader to engage the organization every day to build capability, eliminate barriers, align priorities and reinforce culture. A focus on employee enablement instead of managing empowers the workforce to contribute at their full potential.
2.Vision: Challenge the status quo and collaborate on a compelling why that inspires
Within supply chain circles there’s a lot of talk about artificial intelligence, the autonomous supply chain and “lights out” planning. Many COOs and CSCOs think it’s still years out. They would be wise to challenge that assumption.
Shifting to an autonomous supply chain will be a massively complicated initiative that many workers may not have the skills for, and where many of today’s jobs will become redundant. Similarly, at a time of economic uncertainty, COOs and CSCOs may pursue a transformation that only considers reducing supply chain costs. Both scenarios for transformation will create anxiety for workers if leadership doesn’t craft a vision that inspires them to believe in the transformation and go the extra mile when times get tough. Yet, according to the EY and University of Oxford research, operations leader respondents are 11 percentage points less likely than other functional leaders to say their transformation vision addressed an issue they were passionate about.
Employees understand it’s a competitive world. When they understand cost dynamics and how they can contribute to making a difference, vision becomes more than just a corporate slogan.
3.Care: Be transparent and engage in deep listening
During a transformation, there can be a surprising naïveté about what the journey entails and what it’s going to take to get to the next level. COOs and CSCOs need to be completely transparent with their teams about the ups and downs of the journey ahead so that there are no surprises.
They also need to demonstrate more empathy and psychological safety than they may be accustomed to. Only 32% of the operations workforce respondents agree that their function offered high levels of emotional support vs. 45% of operations leader respondents who feel the same. Supply chain and operations are high-octane environments that require a lot of fire fighting. These kinds of settings don’t tend to lend themselves to deep listening and emotional support. To provide their people with the right level of psychological safety, COOs and CSCOs may first have to embark on a process of personal development so that they can better understand the emotional journey and become the leader that workers need them to be.
4.Empower: Foster an environment of disciplined freedom
The idea of being given the autonomy or responsibility for their role can be scary for many workers. It’s a process from simply operating the machine or performing a series of tasks to understanding every aspect of the equipment and taking the lead on problem-solving. During the transformation journey, there may be some workers who aren’t willing to assume that level of responsibility initially. For those who are, the experience is empowering. However, even though 45% of operations leader respondents say the process encouraged innovative experimentation and new ideas, only 32% of operations worker respondents agree.
Of course, within the freedom to make autonomous decisions, there also needs to be discipline around reaching macro targets. A machine operator may have complete authority for shutting their equipment down in the middle of a shift to service it, but they will also need to understand the bigger picture in terms of the key performance indicators (KPIs) their line needs to meet. They will need to try and ensure that any decisions they make at a micro level align with the desired objectives or outcomes at a macro level.
5.Build: Address the human dimensions of technology
Conversations with the COOs and CSCOs almost always includes technology. Today’s supply chains are entirely reliant on technology, end-to-end. However, it’s important that COOs and CSCOs don’t chase the latest technology simply for the sake of it. They need to stay focused on the business problem they are trying to solve.
At the same time, they need to understand the impact technology has on their workforce. There is the issue of reskilling and upskilling talent to use new technology and giving them the time and space to learn and experiment with it. In our research, 33% of operations worker respondents say they have the digital skills and mindset needed for transformation versus 44% of all other workers surveyed.
Along other parts of the supply chain, leaders need to help workers prepare for new technology that may make day-to-day activities obsolete but will free them up for more strategic activities and decision-making. One of the ways to foster engagement and buy-in is to use technology to drive visible action. Technology isn’t the vision, but it can help to bring the transformation vision to life.
6.Collaborate: Create a culture of collaboration and co-creation
Creating a culture of collaboration is critical. Much can get lost in the seams of a supply chain, particularly when various parts continue to cling to siloed ways of working. Indeed, 45% of operations leader respondents say they collaborated well across units, functions and geographies, but only 34% of operations worker respondents agreed with this assessment.
The traditional approach to transformation is often one of separation and independence. Leaders do the thinking, workers do the doing, strategists do the strategizing and managers do the implementing. For new ways of working to be successful, leaders and workers need to work together to reimagine the concepts around process, delegation, ownership and empowerment and the KPIs by which performance is measured should shift to include behavioral metrics as well as capability metrics.
By adopting leading practices in six key areas, COOs and CSCOs will be better able to harness the power of their people to drive transformation success.