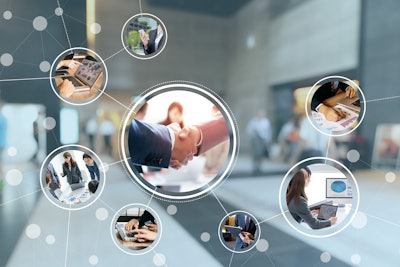
The pandemic hit the U.S. manufacturing industry hard with nearly a 1.5 million job losses. So, it stands to reason that as we move toward recovery, there will be workers to fill the positions opening up, however the story is not so simple. According to the National Bureau of Labor Statistics, manufacturers are yet to recover 41% of the jobs lost due to the pandemic, leaving more than half a million open manufacturing jobs.
Even before the pandemic, Deloitte research projected that 2.4 million factory jobs could remain unfilled through 2028. And indeed, The National Association of Manufacturers (NAM) Manufacturers’ Outlook Survey continues to find that attracting and retaining a quality workforce is one of the top business challenges for manufacturers. In this current environment, many manufacturers are also investing in and making the move to becoming true smart factories, by collecting and connecting production data, analyzing the data to drive better insights and augmenting human intelligence with machine intelligence.
Sourcing, developing, and retaining talent is especially problematic in smart factories because they are competing against industry peers as well as top tech companies who are looking for similar skills. To win at the talent wars, smart factory leaders are going to need to get creative and think differently.
Transform jobs into superjobs
Smart factory jobs look different from those in traditional manufacturing environments. While much of the low-skilled, repetitive work is being automated, other jobs are proliferating – ones that require employees to work alongside machines, analyze and interpret data, solve problems as they arise and communicate with a diverse range of organizational stakeholders. In short, many smart factory positions are evolving into “superjobs.” Superjobs are positions that combine components of varying traditional jobs and are “super charged” by artificial intelligence (AI) and smart technology. They bring together technical skills and institutional knowledge with soft skills such as communication, customer service and collaboration.
The emergence of superjobs forces organizations to think about architecting work in new and creative ways. Automating existing tasks will yield a certain level of improvement, but it will only go so far. By combining the strengths of the human workforce with machines and platforms, manufacturers can achieve exponential improvements in customer service, output and productivity.
Turn workforce development into your secret weapon
Workforce development and training have always been important methods for keeping workforce skills fresh and relevant. But, today’s smart factories will need to train or re-skill entire talent pools—from those just coming into the organization, to existing employees who often take on entirely new roles. Interestingly, organizations have a need for both more traditional manufacturing skills such as machining, welding and fabrication as well as newer skills like data analytics and programming.
There has been a re-emergence of “vocational” programs as a preferred pathway to developing key manufacturing skills. Additionally, many manufacturing organizations have developed relationships with universities and even high schools to ensure a steady pipeline of talent. Industry leaders go further, creating immersive apprenticeship experiences for students that give them both real-world experience, as well as a passion for the industry itself. This last point is key -- in order to attract the type of talent it requires for the future, manufacturing will need to sell itself to a new generation of job seekers who may alternatively gravitate toward a career in tech. That means dispelling traditional notions of what it’s like to work in manufacturing and painting a picture of the exciting career paths the industry has to offer, like the use of agile, cross-functional teams, the establishment of knowledge transfer programs between longer tenured and new members of the workforce and the opportunity to use cutting-edge technology.
Re-skilling the existing workforce--many of whose jobs are being automated--has also become critical. This is especially important for high performers whose jobs are at risk for automation. In the case of machine operators, for example, organizations should consider looking at top performers in this job category and invest in these individuals to learn advanced skills such as CAD/CAM and CNC programming as a way to develop and retain them by providing a tangible career path for growth in an environment that will increasingly require workers to partner with machines.
Another example of critical skills is digital fluency—a capability that can be applied broadly to multiple workforce challenges. There are a number of advanced technologies that companies can leverage to ramp up digital fluency. For example, augmented reality (AR)/virtual reality (VR) glasses can be used to simulate new tasks and help employees develop the skills needed to accomplish them.
Widen the net and shrink the holes
Two of the most basic talent management challenges manufacturing organizations face are attracting the right talent and keeping it. Given the fact that many factory jobs – especially those calling for technical and digital capabilities – remain unfilled, organizations may need to start considering other talent sources, like focusing on attracting a more gender-balanced workforce. Only about one in three manufacturing roles are filled by women, and according to the 2021 Deloitte and The Manufacturing Institute DEI Study, one in four women in those manufacturing roles are contemplating leaving the industry, often the result of poor work-life balance or lack of flexible work arrangements. On a related note, turnover also can be high among minority populations, with employees, especially black employees, citing lack of career progression and cultural mismatches.
The need to address diversity, equity and inclusion (DEI) gaps in manufacturing organizations has become more urgent. According to Deloitte’s 2021 Global Resilience Study, manufacturers who undertake DEI efforts tend to have better financial results, and 63% of manufacturers say DEI has enhanced their ability to attract, retain and develop talent.
Well-executed DEI training, targeted employee resource groups and formal mentorship and sponsorship programs that help employees identify career paths are all critical elements of any DEI strategy. They should be part of a broader DEI strategy that manufacturers are increasingly adopting. Here are some of the specific areas where manufacturers are focusing to move the needle:
· Clarify career pathways and leadership training for employees. Nearly 73% of respondents believe that defined career pathways are most impactful at retaining employees.
· Pivot hiring strategy to broaden selection requirements (e.g. knowledge, skills, abilities) against which candidates are filtered and measured.
· Expand beyond talent programs to address DEI. Manufacturers are looking at areas like supply chain, product development and external partnerships as ways to advance their DEI journeys.
It is vital to the future of manufacturing that organizations embrace and implement workforce strategies that helps develop and retain their current workforce, while also working toward developing a new generation of workers. By doing so, they will position themselves as employers of choice who will continue to grow and invest in their workforce.