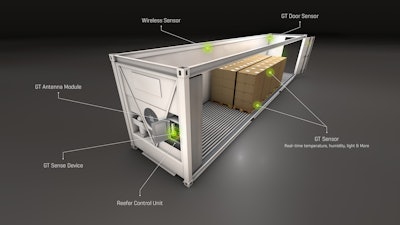
Last but not least, the old saying goes. And that certainly seems to be true for the ocean carrier sector. The industry is the last transportation mode to truly embrace digitization in a meaningful way, and as times change, it’s no surprise Maersk Line is leading the way.
In July, the ocean liner launched a solution called Remote Container Management (RCM), providing visibility of a refrigerated container’s location and the atmospheric conditions inside throughout its journey. RCM gives customers shipping refrigerated cargo an unprecedented understanding of their supply chain—something they have long been asking for.
While this is good news for shippers, and ultimately the consumer, it means the industry’s other major carriers must now follow suit or risk losing market share.
“There’s almost an impetus or a real push to (find a solution), because if you’re one of the big avocado importers and Maersk comes to you and says, ‘Well, I can give you all the temperature data real time, even on my ship,’ and you go to the next one in the top 10 and say, ‘Well, can you do that?’ And they say, ‘No.’ Well, where are you going to go?” explains Don Miller, vice president of global sales and marketing at Globe Tracker, a provider of solutions designed to remotely track, monitor and maintain supply chain assets.
“It’s not like (shippers) haven’t asked for the data before; they’ve always wanted it. It’s just a matter of (Maersk) opening up a can of worms, if you will, and now everyone really needs these solutions,” he adds.
And while the move by Maersk Line is certainly accelerating the sector’s move toward a digital supply chain, it is not the only factor contributing to innovation. In the food supply chain, it’s not solely about customer assurance (though that certainly is top of mind). Logistics providers also must comply with numerous federally-mandated regulations, such as the Food Safety Modernization Act (FSMA), as well as adhere to highly sensitive temperature standards for perishable commodities. Consumers are driving innovation in many industries, but with regards to the food and beverage sector, you are seeing faster adoption of technologies to optimize the supply chain. Not only is greater supply chain visibility a strategic advantage for the industry, but a matter of safety and health.
Perfect Timing
For a company like Globe Tracker, the timing could not be more perfect for a technological revolution in the way ocean carriers transport perishable goods. The software provider’s Sense Reefer, which provides real-time reefer monitoring and control, data and alarms, is now in its second generation, which included the addition of pallet-level sensors.
“This version is able to provide data inside the container from an individual pallet and even inside a box on the pallet. Light sensors can actually detect if someone even opens a box inside your container, if you wanted to have that specific demand,” Miller says.
From a food standpoint, Miller believes these sensors are one of the most exciting innovations to happen with fruits and vegetables, which have a high loss during transit.
“We are able to put multiple sensors in each pallet and condition monitor everything from when it goes into the container and comes out. What becomes exciting there is that we can create a first in, first out model for the pallets coming off the ocean because…we can monitor each pallet for damage and tilt and humidity and know what was affected where. Get a picture of the inside of the container, if you will,” Miller adds.
This in turn makes it easier for the distributor to determine the exact shelf life of an item before it is even off the container, thus realizing more sales of the product.
Sense Reefer was initially created primarily to address issues around repair and maintenance, but as Globe Tracker looked at the markets and what people were asking for, even from the shipping and third-party logistics (3PL) side, it was more about the cargo than it was about the actual container or equipment.
“We had to introduce a technology that would allow us to communicate through the refrigerated container wall right into the cargo space and to every pallet, even when the reefer is unplugged,” Miller says. “We made it possible with our device that it charges itself when the reefer is powered, so there’s no explanation of what the variation in temperatures are, and there’s no explanation of why you have no data because you’re in transition from vessel to port. You have an opportunity for data all the way through, which is particularly appealing for pharmaceuticals, but also food.”
Making Sense of Data
Real-time data and visibility has never been more important than in today’s consumer demand-driven environment, especially in the transportation of food and beverage. But having data and actually understanding that data are two very different things. ClearMetal, which has self-titled itself as a predictive logistics company, is helping companies to make sense of supply chain data and get advanced visibility and predictive visibility into their supply chain’s flow by utilizing an artificial intelligence (AI)-based platform.
“Our platform cleans that data. It structures it. It normalizes that information and allows companies in the supply chain to finally make valuable use of the data that they have in their hands,” explains Adam Compain, founder and CEO of ClearMetal.
“Second, what we do is we provide applications that allow supply chain professionals to make the most efficient decisions on how to order cargo, how to watch those shipments move across the world, predict when exceptions might go awry, and when those shipments will finally arrive at their destination. And basically also predict the behavior of the different logistics providers that are serving those shippers.”
The third benefit of ClearMetal’s AI-based solution is its predictive visibility capabilities. Shippers are able to predict much farther in advance, and with much higher granularity of certainty, what’s likely to go awry in the supply chain or when shipments will finally arrive.
“Supply chain experts can actually make better decisions, plan strategically, manage exceptions before they actually happen, and deliver far better customer service to the recipients of those shipments,” notes Compain.
A shift in production upstream in the supply chain as well as the Amazon Effect downstream is putting new pressures on both logistics providers and the shippers to run much leaner supply chains. Many logistics providers, including ocean carriers, Compain says, are waking up to the fact that in this new digital era they have to use a fundamentally different type of technology and approach than they used in the past.
“What we’re seeing with transportation and logistics specifically, is there’s an interesting use case, because everyone needs predictability. Everyone needs visibility and traceability,” says Brian Nella, director of marketing for ClearMetal. “And if you think about food, you’re dealing with perishables. It’s not just customers that are seeking assurance. You have regulators and safety compliance rules around traceability and ingredients. In some cases, the customers are driving innovation, but in others, like with food, you actually have regulators as well.”
Nella believes the food and beverage industry may actually see innovation and a movement toward a digital supply chain faster because of the multiple pressures the sector faces. “Supply chain visibility is no longer just a strategic advantage, but it’s also sometimes a matter of health and safety,” he adds.
Customers Expect Visibility
Global trade is one of the biggest and oldest industries in the world that still operates like it is 1970, according to Nerijus Poskus, vice president of global pricing and procurement at Flexport, a freight forwarding and customs broker.
“Flexport is challenging the status quo by applying a modern software layer as part of our freight forwarding service, enabling our team to be efficient and allowing importers to have full visibility and control into their shipments every step of the way,” he explains.
In a nutshell, Flexport’s software enables them to provide real-time shipment updates and SKU-level visibility for each of their clients’ shipments, which requires a keen eye in data integrity and operations.
“This kind of transparency helps our customers better understand their supply chain activities (e.g., landed cost of goods) and make even smarter business decisions,” Poskus adds.
And while automating transaction costs is not a new concept, Flexport is innovative in the way it has combined machine learning with human expertise. Most companies have customer support teams that operate in a silo. Flexport operates in autonomous squads, with representation from sales, account management, operations and customs compliance. Each squad owns its client relationships from end-to-end and is empowered to make their own decisions on what is best for the customer and the business without needing to appeal to a higher authority.
“We operate in a complex industry, and that means that every shipment we manage will need an expert involved,” notes Poskus. “It’s this combination of human expertise and machine intelligence that allows us to provide the most value to our customers and set us apart from our competitors.”
Poskus believes this level of transparency and reliability soon will become the norm for ocean carriers, as customers will expect visibility into their partner’s operations on their behalf.
“We envision a world without the significant bottlenecks we see today,” says Poskus. “To eradicate all of those lags…we are open to new technologies and to disruption, and we’re excited about bringing in modern techniques to help the industry adapt for this decade.”