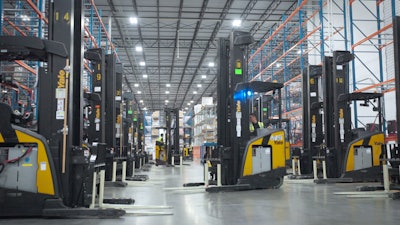
Picture this: you’re standing on the football field. The grass is freshly cut, the paint lines are crisp, the equipment is set – it’s game day. But when you look around, your team is not at full strength, with key players unavailable to play. How can you possibly win? That’s how it feels to deal with today’s labor shortage crisis.
Since 2022, the U.S. Bureau of Labor Statistics reports the warehouse labor force has decreased by over 120,000 workers. These difficulties are not showing signs of abating. Due to broad demographic shifts, the U.S. workforce is actually shrinking. The civilian labor force participation rate has been sliding downwards for the last 20 years, according to the BLS. Add to that the fact that baby boomers are reaching retirement age at a rate of about 10,000 per day and that by 2030, all will be at least age 65. At the same time, Americans are having fewer children, with the birth rate remaining below replacement levels. These demographic trends mean that warehouses must critically evaluate how they approach managing their workforce and leverage processes and technologies to help improve labor productivity and bolster retention.
Step 1: Listen to what operators need
Both to minimize the threat of turnover and encourage high performance, it is crucial that managers listen to what employees have to say and address what is important to them. At a general level, the Society for Human Resource Management identifies several factors that can help retain quality employees, including:
· Opportunities to use skills and abilities at work
· Trust and clear communication between employees and management
· Compensation/pay
Likewise, other factors can also drive employees away, namely a lack of feedback about performance, unclear expectations and failure to provide a framework that sets employees up for success.
To help cultivate employee trust, clear expectations and a framework for success, operations can turn to warehouse technology, such as telemetry. Telemetry systems offer a broad range of insights about lift truck usage and performance, some of which can be leveraged as effective tools for data-driven performance tracking. By assigning utilization and impact data to individual operators, warehouses can add an extra layer of accountability for ineffective operators, while incentivizing high-performing employees, yielding more informed labor management decisions.
Step 2: Assigning the right tasks to the right operators
While average annual turnover in the industry commonly comes in at nearly 50%, it can fluctuate wildly between operations. The WERC DC measures survey identifies “best-in-class” warehouses as having less than 6.2% annual turnover, while operations with turnover greater than 47% are classified as performers with “major opportunity” to improve. Limiting turnover can have significant ramifications for an operation’s bottom line due to the cost of turnover – hiring and training just one replacement worker can cost thousands of dollars.
Automation can handle repetitive tasks, like load transportation and even retrieving or depositing loads from elevated conveyor lines and storage locations. Augmenting a workforce with automation relieves employees of mundane, repetitive tasks, freeing them to focus on more engaging responsibilities. That shift is meaningful for retaining top talent, according to a Gallup study, organizations with better employee engagement achieve higher performance, including substantially better retention and productivity.
Step 3: Set operators up for success
The level of concern among industry leaders about today’s labor challenges indicates how acutely labor influences overall warehouse performance. Businesses depend on the speed, efficiency and accuracy of their operators to keep mission-critical workflows moving on target.
In such a tight labor market, warehouses are competing against each other for the same restricted pool of skilled workers. Rather than incur the expense and time commitment of training inexperienced personnel, warehouses may attempt to attract high performers away from other facilities located nearby, making offers of greater compensation, better opportunities or superior equipment.
Because warehouse labor is subject to such intense churn, businesses must make the best of available labor by setting operators up for high performance. Empowering operators to thrive at work can also give them reason to stay with an employer, helping to counter poaching efforts.
Beyond essential training, warehouses can take advantage of a class of technologies known as operator assist solutions (OAS) that can help lend lift truck operators a hand and further support adherence to best practices.
Traditional forklift awareness supports like lights and alarms may be more well known supports that fall under the broad OAS umbrella. But OAS can also take the form of newer technology systems that provide varying levels of support. A stability control system monitors input from the lift truck and applies automatic, real-time interventions to help support stable travel and provide operators with an immediate layer of feedback to help reinforce the best practices they learned in their training. Operator assistance technology can go even further, with awareness of not only inputs from the truck, but also of the operating environment. In practice, this level of technology can enable a broad range of functionality, such as automatically slowing down the truck if the system detects a pedestrian or obstacle in the path of travel.
Step 4: Implementing ergonomic equipment
Ergonomics and other equipment characteristics have a meaningful impact not only on operator comfort, but productivity, too. The National Safety Council reports that 97% of workers have at least one workplace fatigue risk factor and more than 80% have two or more. When multiple risk factors are present, the potential for injuries on the job increases.
Keeping operators fresher and more focused, combined with subtle features designed to boost performance, can lead to productivity gains that might seem small at first, but add up quickly. For example, one-touch controls on motorized pallet trucks can help operators expedite movement and between pick locations, helping shave seconds off each pick. The operator compartment can be equipped to support operator productivity. Generously sized compartments designed to prioritize visibility can help operators find a comfortable position without having to crane their necks to see the task at hand. For a smoother ride, cushions and suspended floor systems can significantly reducing shocks and vibrations felt by the operator.
Identify best-fit solutions for operators
Achieving best-in-class warehouse performance requires operations to understand labor as an important part of their total warehouse strategy. Just as managers might re-rack a facility to achieve a more efficient storage process or greater capacity, operations must consider what conditions can be optimized to improve labor performance. The solution may involve a combination of strategies, whether moving cumbersome, time-consuming tasks away from operators, using technology to manage performance and reinforce safe, efficient operation or equipping employees with tools that better support comfort and productivity. Actively incorporating operator input will help warehouses determine the best-fit set of tools and frameworks to maximize labor productivity and retention, while controlling costs.