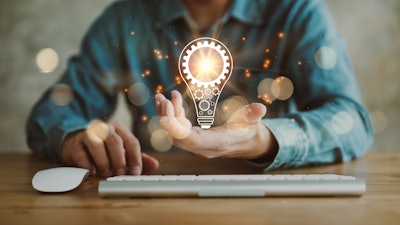
Accuracy is one of the major pillars of a successful supply chain, along with velocity and transparency. The global supply chain is stretched further than ever before, still catching up with the seismic shift from B2B2C to B2C during the pandemic – the sheer number of parcels has increased a shocking 27% since 2020. At the same time, technology has moved forward to meet the moment and prepare for the future, with an eye on accuracy.
To alleviate supply chain pressures, the industry is moving towards solving the challenges surrounding achieving accuracy through a digitally connected supply chain. While it may seem intuitive to connect each link, the unfortunate truth is that the supply chain has been built silo by silo over time. While it is obviously impossible to physically connect the points along the supply chain, it is possible to digitally connect them. A digitally connected supply chain will meet current and future challenges.
Achieving accuracy at source
When a digital ID is given to each item at source, it has a ripple effect all the way across the supply chain to the final destination. By utilizing intelligent labels such as RFID at source, a unique ID is given to the product at its infancy, and this unique product license plate then carries the product’s comprehensive data through every step of the supply chain. The digital ID acts as a trigger for automation as that product moves from facility to facility. Accurate product data created at the source can ensure accuracy across the supply chain.
The objective of a digitally connected supply chain is to make the parcel move more efficiently through the shipping network. The simple fact is that accuracy enables greater efficiency. That’s because a large component of that efficiency is reducing the significant number of errors that happen across a multi-touchpoint supply chain and costs brands and retailers millions of dollars each year.
Goodbye clipboards
Among the major pain points that create inaccuracies are manual processes. In the 21st century, with tablets, laptops and mobile phones embraced by all adults both at home and at work, the fact that people are still running around with clipboards defies logic. It is not a secret that a manual spot-check of inbound and outbound parcels is neither efficient nor accurate. It’s high time that the errors that manual processes generate are relegated to history.
A major benefit of digitally connecting products throughout the supply chain is consistency of accurate product counts. With RFID labels, no line of sight is required so products can be scanned passively by deploying automated reading technology such as a tunnel placed along a conveyor belt, or an overhead reader placed above a dock door. Whatever type of label is utilized, the result is the same: a true record of chain of custody of every item and accurate count for every shipment as it travels to each subsequent touchpoint on the supply chain.
The advantage of RFID is immediately evident in inventory control. RFID accomplishes inventory control without a line of sight, much less a pencil and paper. Not only do intelligent labels allow operators to manage inventory faster and more accurately, but data also contained in the label flows through the entire ecosystem.
Data drives downstream accuracy
Whether inbound and outbound operations deploy intelligent labels for parcels or pallets, an important aspect of streamlining and automating supply chain operations is having the accurate data they contain. This data is more important at every point downstream because any network error will be magnified at each subsequent point.
By mass reading parcels, a palette or truckload, a connected digital ID solution automatically spots the numerical difference and communicates the gap to the supplier. So, for starters, retailers need not pay for items not received from suppliers. At each inbound and outbound touchpoint, the counts are verified for accuracy.
Digital IDs on every product directly addresses the increasing volume and complexity of supply chain partners by allowing all operators to have full transparency on what is coming inbound and going outbound. The verification process is triggered by the digital ID at every touchpoint. This benefits the warehouse responsible for receiving orders and then sending them out, as well as the shippers who need to account for what comes into the trucks and what goes on the road. Further on, a retail store has accurate expectations for product count, arrival, enabling them to plan for operations from stocking to replenishment to promotions.
For example, LTL shipping takes many steps starting at pick up, through the carrier network, and on to the last mile. If something goes awry upstream, the error is magnified and becomes more costly downstream, because all the touchpoints become invalid until the discrepancy is corrected. The simple fact is every misrouted parcel wastes time and costs money. Avoiding routing errors by having accurate and visible data, translates to a much less error-prone process. Our studies show that in digitally connected supply chain processes, operational efficiency increases 20%.
The exponential change in the retail landscape has forced supply chains to take a step back and holistically examine operations. Executives are looking to implement technology and processes that enable resilience to address not only the current landscape, but to be future proofed for the next set of challenges. It is inevitable that supply chains will increase in complexity as consumer expectations for speedy, accurate delivery continue to escalate. The digitally connected supply chain is the way forward.