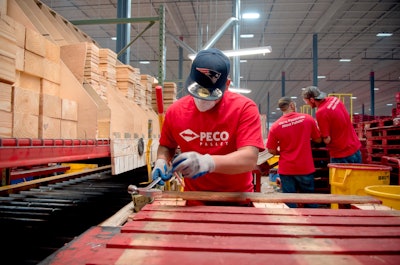
The pandemic has upended virtually every facet of supply chain operations. Strategies that once emphasized “just-in-time” speed and velocity and minimal “at-rest” inventory are being rewritten along “just-in-case” lines. Why? To respond to pandemic-related disruptions with a new emphasis on ordering larger lots of goods and holding more product in warehouses or distribution centers for longer periods of time to enhance safety stock in this time of uncertainty.
And, that means adjustments to strategies and tactics to maintain and manage pallet supply networks.
Pallet networks operate under many of the same supply chain dynamics as goods themselves. A sufficient supply of pallets is critical. Supply chains require pallets in the right place at the right time, otherwise product shipments are delayed or cancelled, inventory flow is disrupted and product availability is compromised. A pallet network requires the same coordinated planning, attention to detail, cost and flexibility as that devoted to the overall supply chain and the products moving within it.
Here are some key questions supply chain and logistics managers should consider as they evaluate and adjust their pallet supply decisions to adapt to today’s market realities.
Which approach is best: buy or rent pallets?
It depends on several factors, and the objectives of your supply chain for product velocity as well as longer-term storage. Such factors include type of product being shipped, where shipments are going, how long in transit, “dwell time” or how long the pallet is in storage and parked at the destination warehouse or distributor and when the pallet is released to be recovered and redeployed.
Factors to consider in a “buy” strategy
It has been widely reported that lumber prices are skyrocketing. The increased lumber prices have dramatically increased the cost of purchasing a new Grocery Manufacturers Association (GMA)-certified nine-block 48x40-inch white wood pallet, which today is approaching $50 (a year ago it was closer to $35.) And, that’s if you can find them. Rising costs along with a shortage of raw material has limited new supply and made what is available that much more expensive.
Then, as the pallet owner, expense for recovery, maintenance, repair, repositioning and redeployment all must be planned for and absorbed. The lifetime usability of a typical stringer pallet is limited as well. Typically, a stringer pallet will have two cycles of use with 4-6 handlings per cycle before their useful life expires, they become unsafe to use and must be discarded. Also, to be factored in are replacement costs to replenish your owned pallet inventory. These supply chains have not been spared by the historic lumber market increases and availability concerns.
An owned white-wood solution typically is adopted by shippers or distributors who have a need for long inventory hold times (typically months), and who consider pallets the same as packaging “dunnage” – a throwaway operating cost.
Factors to consider in a “rent” strategy
The highly engineered, 4-way, 9-block-style rental pallet is by far the most durable and efficient as it moves through the supply chain. It is engineered to accommodate the rigors of automated handling systems, is easier to wrap and pinwheel, is typically sturdier and more reliable and can carry more weight, and most importantly, is a sustainable operating model.
The key to accurately measuring a pallet rental program is focusing on total trip cost and, more broadly, total cost of ownership. Rental pricing is typically done on a per-turn basis, with other variable costs for items like fuel (for the transportation cost to recover and return the pallet to the pallet company’s staging and maintenance depots) and lumber surcharges.
Considering all the various factors, once an operating plan is developed, a dependable pallet rental cost can be tightly dialed in, enabling the shipper to reliably budget and manage the expense.
Unlike white wood, with rental pallets all costs for recovery, maintenance, repair and delivery and replenishment of pallet inventories to the user – such as a consumer products manufacturer, distributor or beverage producer – are assumed by the pallet rental firm.
One decision yardstick to consider in a rental strategy is how quickly the pallet “turns;” in other words, how long it takes to complete its delivery mission, be released back to the pallet company and returned to its inventory network.
Faster turns, reduced handling and less wear on the pallets typically reflect lower price points. Beverages and perishables tend to be the fastest-moving products (and incur the lowest rental costs), with pallets available for recovery in as little as 10 days. Supply chains where the need to hold product on pallets for up to 30 days still can offer an attractive total cost of ownership in a rental program, again, considering usage variables and dwell time.
Rental pallet pricing can vary significantly based on quantity, shipper location, usage and demand. Typically, a rental pallet will do multiple turns per year. And, with effective maintenance and quality control, the life of a rental pallet can extend beyond 10 years with appropriate repairs and maintenance.
What’s the biggest challenge shippers face in designing and deploying a cost-effective pallet supply strategy?
The biggest challenge is lack of alignment between the various constituencies within a company that influence or participate in the supply chain. Procurement wants the lowest price on everything. Warehouse managers want to optimize floor space and inbound/outbound flow of goods. Traffic managers want the lowest freight costs. Order management wants strong on-hand inventory and fast order cycle fulfillment. Sales forecasting wants sufficient product on hand to avoid stockouts and missed revenue opportunities. Demand management wants supply when and where it is needed on time.
Today, many companies are increasing inventory stocks and seeing related supply chain costs jump. The key to achieving lowest total landed cost is exerting effective control through a collaborative approach that breaks down traditional silos, encourages cooperation and has all players agreed on a common set of metrics across the board. That’s the key to achieving lowest total landed cost.
For the pallet provider, the key then is to be flexible, understand the different dynamics and find process improvements or adjustments that can reduce costs and waste while delivering the best cost/service solution.
What should the end game be in a pallet inventory strategy?
A successful strategy will secure the lowest total cost of ownership, and that pallet cost will be influenced by all the elements of managing, moving, holding and deploying your product in the market. Every pallet strategy should be built upon a process improvement goal: How does it support and effect the “whole” of inventory management?
A pallet provider should have the tools and expertise to work with you and define a strategy that reduces dwell time and leverages superior pallet availability and performance to get you the optimal product velocity aligned with the lowest total landed cost for your product. Every business wants to speed the turn of inventory and maintain the optimal level of safety stock to meet consumer demand. Pallet assets have to be completely aligned with and in support of those objectives. Sophisticated and purpose-designed programs, balancing cost, asset availability and leveraging optimized and fluid national pallet networks are ideally positioned to deliver those benefits.