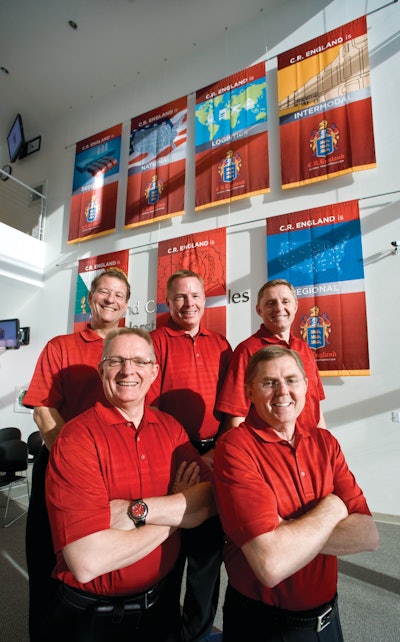
If there’s one thing that’s certain right now, it’s that the trucking industry is awash in uncertainty. Unlike other transportation providers, the trucking industry is battling numerous and unpredictable variables ranging from labor to regulations to fuel prices, all of which are making the fleet manager’s job ever more challenging.
A host of variables in the market
A shortage of qualified drivers has been a concern for the industry over the past few years, but with the advent of new and stricter regulations, the problem is bound to get worse. Furthermore, it’s putting a tighter squeeze on capacity.
“We’re in a tight capacity market right now,” acknowledges Derek Leathers, CEO of Werner Enterprises. “The driver shortage is becoming more real and it’s becoming increasingly more difficult to obtain and attract quality drivers.”
Adding to the capacity constraints is the overall financial climate in the industry, which is keeping new entrants on the sidelines, says Leathers. Thirdly, are government regulations, he says.
“All three have a net effect of limiting the growth of capacity, but in our opinion, the result is actually a net capacity reduction.”
The impact of government regulations alone are a huge challenge for the industry, in part because there have been revisions of key regulations over the past few years, and there are likely to be more changes ahead.
In December, the Federal Motor Carrier Safety Administration (FMCSA) issued revised hours of service rules, which prompted a mixed reaction from the trade community. Although many were bracing for a more dramatic overhaul, that doesn’t mean that the latest revisions aren’t causing some anxiety in the industry.
CSA, or the Compliance, Safety, Accountability initiative, is the other moving target on the trucking industry’s radar.
“We believe there are still some fundamental issues with the program,” Werner’s Leathers explains. The initial effect of CSA was to unnecessarily “cleanse drivers from the network,” he says, even though for many there wasn’t a correlation with safety. Secondly, it added costs, says Leathers, especially in the area of maintenance. He gives several examples, such as “pulling tires off 1/32 too early, or opting to fix lights where the truck is sitting rather than getting it to the next port in your network where it can be done by your own mechanics.”
These “add up to maintenance ‘cost creep’ for carriers, and that’s definitely been a negative under CSA,” says Leathers.
State regulations are impacting the trucking industry, too. The California Air Resources Board’s (CARB) Transportation Refrigeration Unit regulation is one example, and it has a significant impact on food shippers and carriers alike.
“You can’t be in the temperature controlled space and not operate in California,” concedes Leathers. But, the cost of compliance is stiff, which further hikes up operating costs.
The obvious question on shippers’ minds is how will all the turmoil in the industry affect rates?
According to Leathers, “Whenever rates are in play there’s always a bit of gamesmanship, potentially on both sides of the desk.” Yet, the climate is less contentious than in prior years, he points out.
“I think shippers are very realistic now and they understand that our cost pressures are real and they’re not going away. Overall, the dialogue [with shippers about rates] has been very open.”
Leathers believes the key to weathering the storm lies in collaboration between shippers and carriers, which can ultimately lower costs even as rates are going up. “There’s never been a more important time to collaborate,” he emphasizes. “Costs are absolutely going up from the carriers’ perspective and some of those are going to have to be passed on to shippers. The question is: ‘How do you mitigate them?’ In our experience, there’s still plenty of planning optimization and design work out there to offset the rate inflation that is inevitable. And, now’s the time for shippers and carriers to get serious about it.”
Sustainability continues to pay off
Like many leading carriers, Werner has remained committed to sustainability and continues to see a payoff for its efforts.
“We’re heavily involved in all things fuel efficient,” says Leathers. “But, it’s driven primarily by our desire to be the lowest cost carrier to our customer.” Aside from environmental responsibilities and maintaining the company’s high level status in the EPA’s SmartWay program, Werner relies on sustainability initiatives to save fuel.
“Fuel is the single highest operating expense that we have outside of labor,” says Leathers, “and we’re going to work extremely hard to control our fuel costs.”
Trailer skirting is one aerodynamic enhancement that Werner has pursued vigorously to reduce fuel burn. “We actually developed, marketed, and patented our own trailer skirt, called the ArrowShield,” says Leathers. In prime operating conditions, the trailer skirts can boost fuel efficiency by 5 percent. Even if the actual percentage is closer to 4 percent, Werner estimates that it could save 5.5 million gallons of fuel a year, which translates to millions of dollars saved annually as well.
Last August, Utility Trailer introduced the USS-120A, the company’s next generation advanced aerodynamic side skirt.
The product is SmartWay verified as an “advanced side skirt” providing a minimum of 5 percent fuel savings, and can be used with low rolling resistance tires on dry vans to achieve CARB (California Air Resources Board) compliance for California operations.
Great Dane Trailers’ ThermoGuard trailers offer a sustainable aspect in terms of their efficiency and performance.
“ThermoGuard is an interior liner for reefer trailers and it’s the only liner in the marketplace that was designed by a trailer manufacturer for the sole purpose of reducing hours run and amount of fuel used in reefer trailers,” explains Chris Hammond, vice president of dealer sales for Great Dane.
In a conventional reefer trailer the insulating foam degrades over time, “and you lose 25 to 35 percent of the insulating ability with a traditional lining,” he says.
The result is increased fuel use as the reefer unit works harder to keep the trailer cool. And, not only is the fuel usage increasing, the reefer unit is running more hours, which adds to wear and tear and more frequent oil changes.
Great Dane’s field tests, run over a 7 year period, resulted in approximately 2,000 gallons of fuel saved for a single truckload operation.
Chris says that the ThermoGuard liner is also stronger. “It’s a derivation of our PunctureGuard product. It’s very resistant to being cut or torn compared to traditional liners, which protects the cleanliness of the trailer.”
Larry Cantanzaro, vice president for safety, Kane is Able, echoes the benefits of sustainability initiatives. The carrier recently purchased fifty International ProStar tractors, which are helping Kane keep fuel costs down, he reports. Ideally, if the government started offering incentives for investing in fuel efficient equipment, the financial benefits would be even greater, Cantanzaro asserts.
In the meantime, Kane has implemented a variety of sustainability measures. “One example is setting truck governors to 62 mpg, which not only keeps the speed down, but encourages the drivers to use cruise control, which also saves fuel,” explains Cantanzaro.
The carrier also uses auxiliary power units (APUs) and super single tires to help reduce fuel costs on its fleet.
In addition, Kane continues to promote the advantages of load consolidations to its customers. “We have been agents of change trying to push our customers in that direction,” says Cantanzaro. Fortunately, “customers are becoming more receptive to it and it’s begun to grow, especially as freight rates have started to climb.”
An emerging interest in CNG and LNG
The industry has started to pay more attention to alternative fuels, specifically compressed natural gas (CNG) and liquid natural gas (LNG).
Although the national infrastructure for filling stations isn’t fully developed and the equipment itself needs further improvements, the good news is that 87 percent of natural gas used in the U.S. is produced domestically and it offers a much cleaner emission compared to diesel.
According to Thom Pronk, C.R. England’s corporate vice president for recruiting, training, and safety, “LNG is a great initiative for our company and we’re seeing tremendous benefits from it. We’re hoping it becomes more cost effective so that the entire industry jumps into it.”
The carrier has been piloting a program with Coca-Cola that involves the use of LNG-powered trucks based out of Ontario, California.
Mitch England, corporate vice president for the carrier, says a growing number of LNG stations in California make the program possible.
“We would love to use this technology more,” says England, but cost is still a barrier, even with government assistance. However, England remains optimistic that it will become a viable alternative in the future.
According to Andy Douglas, Kenworth Truck Company’s national sales manager for specialty markets and a key player in the company’s green truck initiatives, the future may be right around the corner.
“Currently, many local transit and government agencies use CNG to power trucks and buses, so that fuel source may be easier to find. Meanwhile, the natural gas infrastructure available to the public is expanding at an accelerated rate across the U.S. and Canada along well traveled transportation routes.”
Software and technology tools
Despite the myriad challenges in the marketplace, advancements in software and technology are helping both fleet operators and their drivers keep pace with the changes.
Xata Corporation’s Christian Schenk, vice president of product marketing, says saving the customer money is paramount. “We need to help them with their compliance issues and other regulatory pressures,” he says, “and ultimately help them pull cost out of what is typically a very expensive thing to manage.”
And, Xata’s solutions are not only geared towards the fleet operators, but the drivers as well. One product the company is launching soon, Xata Passport, allows drivers to “manage their own safety scores and profitability, and compare themselves to their peers,” explains Schenk.
He compares it to a ‘Car Fax’ report that the driver can take with him, should he change jobs. For example, the driver is able to document his average mpg, his hard brake counts, and so forth.
According to Schenk, “By giving him these tools, the driver becomes a better business person who is also a safer, more valuable employee.”
In the meantime, Scheck says the “mobile revolution” continues to drive changes in the industry and at Xata.
“We are investing more to enable features that were traditionally available only with on-board computers. In other words, we’re building all of our solutions into mobile applications. So the driver will be able to operate in any paradigm he wants—whether that’s a device that’s mounted on the dash, or on a ruggedized hand-held, or on a tablet PC.”