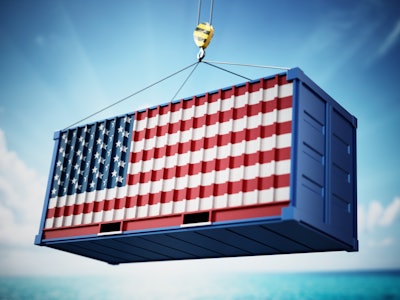
In the past five years, companies have made many changes in their supply chain networks by considering re-shoring and nearshoring the sourcing and assembly of products. U.S. manufacturing companies preferred offshoring to countries in Asia like China because of the lower labor costs and favorable regulations. As more and higher import tariffs were introduced and China’s labor charges increased, this became a less favorable option. As a result, U.S. manufacturers are looking for alternatives to China further stimulated by the growing economic and political tensions between the two countries. Countries in Latin America like Mexico, Colombia, Costa Rica, among others, offer greater benefits to U.S. companies looking to nearshore their suppliers. The main industries that have turned to Mexico in a big way are food and beverage, automotive, aerospace, medical devices and electronics.
At the same time, nearshoring dramatically changes an organization’s supply chain partners, transportation flows and lead times. These new changes increase risk and affect their resilience and agility. Sourcing from multiple countries reduces even more the multi-tier visibility into suppliers.
In fact, according to Gartner, “less than 5% of supply chain leaders report having strong visibility into their contract manufacturers Tier 2 and beyond.” For example, when U.S. automotive companies nearshored their suppliers, assembly and manufacturing to Mexico, this brought radical change in the transportation flows within North America, introducing new challenges and increasing the need for more visibility into different methods of supply chain transportation.
Let’s look at the main benefits of nearshoring to Mexico.
Labor
From a labor perspective, Mexico has a low labor cost but also a healthy working population profile whereas China’s labor cost continues to increase, and their labor force is rapidly aging. Additionally, Mexico offers a talent pool of highly skilled and cost-effective employees. The quality of Mexican labor and higher management employees has been steadily improving over recent years due to the nation’s improved education standards.
Transportation lead times and costs
Trading with Mexico leads to lower transportation costs and a shorter lead time for products to reach the U.S. market by over-the-road transportation. This can help take uncertainty away, which has increased since 2020 and allows U.S. companies to respond to an ever-changing market more quickly and effectively. This provides agility, which in turn increases resiliency. At the same time, shorter lead times reduce inventory levels allowing companies to better utilize their working capital and lower inventory holding costs. This makes nearshoring to Mexico far better than offshoring to faraway nations.
Trade relations
Mexico has become the largest trading partner of the United States. The two countries share strong and favorable trade relations, supported by several agreements. For example, the United States-Mexico-Canada Agreement (USMCA) encourages U.S. companies to set up manufacturing facilities in Mexico. This agreement allows free trade between the three major economies in North America.
Due to the Free Trade Agreement (FTA) Mexico has with several countries, companies from the United States can access multiple markets in other countries if they set up manufacturing in Mexico. This contrasts sharply with the United States’ tense relationship with China where the recent trade war, political disagreements and the pandemic have greatly impacted trade relations.
COVID-19 concerns
During COVID-19, China has had to deal with many government-imposed lockdowns, which affected manufacturing locations, warehouse locations as well as port closures. Additionally, Asia has seen several labor strikes adding additional disruptions to the flow of goods. Mexico has been much more resilient during COVID-19. Throughout the pandemic, the US-Mexico borders have remained open for trade and companies manufacturing units in Mexico were still able to conduct business relatively smoothly.
Infrastructure
Mexico has invested heavily in recent years to develop its industrial areas to attract foreign direct investment from businesses. These steps have drastically improved the manufacturing sector of the country.
Mexico has become so attractive that even China has massively invested in its manufacturing. Major Chinese companies are investing aggressively in Mexico, taking advantage of an expansive North American trade deal. Tracing a path forged by Japanese and South Korean companies, Chinese firms are establishing factories that allow them to label their goods “Made in Mexico,” then trucking their products into the United States duty-free.
But with these benefits also come with challenges. As companies look at their entire networks to make sourcing decisions, there are many risks to consider. Logistics networks are a major component of this decision process as new locations bring logistics capacity, labor, cost and lead-time concerns with them.
To manage these risks, companies turn to supply chain visibility to provide key inputs into data they can use to do proper scenario planning and analysis. Once the organization has executed their re-shoring strategy, companies can further use real-time visibility data to do better long-term supply planning, more accurate transportation planning as well as gain enhanced visibility to their new suppliers. That is why supply chain visibility remains a top focus for companies to improve supply chain risk management.
In a world full of increasing complexity, manufacturing in Mexico simply makes more sense. However, companies need to strategically plan to overcome challenges such as Mexican regulations, the cost of investment and adapting the company’s culture.