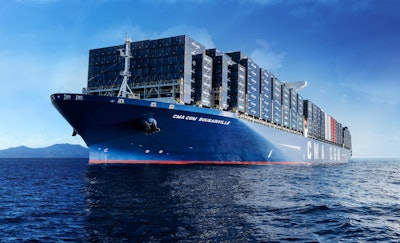
The expansion of satellite and cellular networks has unleashed a tidal wave of opportunities for tracking containers in transport.
As a result, technology investments have increased from 2014 to 2016, with IoT (Internet of Things) sensor and monitoring technology posting the biggest increase at 19 percent, followed by data loggers at 14 percent and GPS and satellite technology at 5 percent, according to a survey by AT&T and eft Supply Chain and Logistics Business Intelligence. The survey polled 600 supply chain decision makers to learn about their existing and future plans for leveraging IoT within their operations.
While most of this investment has focused on ground transport, interest in air and ocean transport have also made progress in recent years. When asked what area they are looking to most improve operational visibility, 80 percent of respondents cited land transport, followed by air shipments (50 percent) and ocean shipments (33 percent).
Ocean carriers, in particular, have made significant investments in recent years, with some of the largest carriers investing in “intelligent” containers.
“Intelligent” containers can provide real-time visibility of inventory, including critical areas such as temperature, humidity, vibration and air quality. For a small investment in hardware and software, containers can provide a lot of supply chain data that not only delivers timely cargo updates, but can also reduce costly manual inspections.
“It has enhanced management’s ability to make quick, actionable decisions in real time,” says Bryan Duncan, director of solutions sales at Wynright, a Daifuku North America Company. “As an example, if a temperature controlled container has a system malfunction, this information is available instantly and a manager can decide to re-route to a closer destination.”
Intelligent Containers Evolve
Early intelligent containers provided asset visibility and were largely designed to prevent theft and record the opening of containers, notes Mark Bünger, vice president at Lux Research Inc. The ability to monitor temperature, humidity and vibration has existed for about a decade, Bünger says, but it has been too expensive to deploy.
This has changed as satellite connectivity has become ubiquitous and electronics and software costs have fallen. Some technology providers have made the systems commercially available.
“Telematics has been used in fleet logistics for a long time, but almost always focused on the front half, the cab, the power unit or tractor,” says Steve West, BlackBerry Technology Solutions senior director of business development. There is a lot of value in the back-end areas such as the tracking container, trailer and chassis that technology companies have recently decided to focus on.
Ocean Containers Evolve
Some technology companies, such as France-based Traxens and Israel-based Loggino, are focusing on monitoring ocean containers. Bünger of Lux Research says tracking is especially critical for ocean transport since there is less opportunity to manually track containers during ocean transport. “Shipping has these huge wait times in ports,” he says. “The containers are a lot more vulnerable (to theft and vandalism) in ports than they are in other places in the supply chain.”
The tracking technology user can be the shipper, the packer, the logistics provider or the carrier, Bünger says. “One of the things that makes logistics in transportation globally so complex is that there are so many people that have an ownership stake in some part of it,” he says.
“We see the adoption starting to come up in terms of vessel-based tracking,” says Michael Dempsey, vice president of container and port solutions for the enterprise solutions group at Orbcomm, an M2M technology provider that has offered vessel tracking since 2008. “We see the temporary reefer monitoring market as growing significantly, especially because of FSMA (Food Safety Modernization Act).”
In addition to regulatory compliance, shippers want the data to enable “first expired, first out” product management, Dempsey notes.
“The solution rolling out today was on offer since 2008, but only a limited number of lines took it up then,” adds Sean Maguire, Orbcomm’s business and product development manager for container and port solutions. “The larger shipping lines are quite conservative, and it takes a long time for them to a) feel comfortable that the hardware is reliable enough, b) that they need it at all, and c) that their customers want it.”
“Now, however, we rarely meet any that deny it’s wanted by customers or that every reefer will be fitted in the future,” he says.
The Orbcomm hardware consists of two pieces, the telemetry device and the antenna. The telemetry device goes inside the controller cabinet and the antenna sits on the outside of the cabinet to achieve a good view of the sky for GPS and for good global GSM/cellular coverage.
Customers can decide how many containers they want to track. In most cases, shippers track all their containers. Some customers use the system on high-value loads only. “They can deploy on a fixed fleet that services a particular corridor or trade route, or they can move the device from reefer-to-reefer based on the booking,” Maguire says.
A Package Of Services
Orbcomm offers different container monitoring services. Reefer cargo tracking includes temperatures, humidity, running state, USDA temps, as well as all active alarms. Reefer machinery tracking includes compressor temperatures and pressures, vent positions, currents and voltages to predict or alert to potential problems or service needs. Telemetry device data includes GPS and GSM signals, internal battery voltages, and SIM details, including what country and GSM networks and tower it’s reporting from.
“Lines will typically make a limited set of data available to the customer such as mapping, temperatures and alarms,” Maguire says.
A shipper might request GPS reefer tracking. The shipper’s carrier can then add the sensor and dispatch the reefer for loading.
One Orbcomm carrier user offers their customers a login to see their booked reefers so both the carrier and the customer can track the reefers in real time and get alarms if any occur.
Maersk Steps Forward
Last year, Maersk Line finished the rollout of sensors on all 270,000 of its reefer containers.
Maersk Line began the project in 2010. The team spent two years developing the hardware and software, says Catja Rasmussen, Maersk Line head of remote container management (RCM). Maersk worked with technology providers on its back-end software. It then took three years to install the hardware on all the company reefers.
The Maersk reefers went “live” in May 2015. The company uses Ericsson satellite signals for monitoring vessels at sea and AT&T cellular signals, GSM (global system for monitoring communication), for tracking containers over land. A 3G SIM card allows remote monitoring of atmospheric conditions and power status.
Maersk Line initially focused on reducing its operating costs from the new technology that, through near-real-time data visibility, contributes to optimized fleet operations, Rasmussen says. Another one of the more robust capabilities is the ability to remotely control a container’s temperature. In a 15-week test period, the company has intervened in 180 instances in which they adjusted temperatures and most likely prevented product damage.
“We can react faster,” Rasmussen says. “We simply didn’t have the visibility before. Now we can constantly see where all our reefers are and how they are doing at any point in time.”
“We can also optimize the way our reefers are handled in the terminals,” she notes. Previously, after the reefers had been plugged into power outlets upon arriving at terminals, the employees would have to check the temperatures of every reefer at least once a day. With the real-time monitoring, the employees only have to attend to those reefers that need attention after having plugged in the power cables.
“We are optimizing our operational procedures before we launch this to our customers,” she says. The company hopes to make the technology commercially available in 2017.
What About Empty Reefers?
Another important feature is the ability to calculate the expected state of the empty export reefers. Empty export reefers require a service check before being returned to a customer. Prior to the remote monitoring, this service check could take as long as six hours, as the reefers in some cases would need to cool down before they could be checked.
“Because we are gathering all these data points, we are actually able to calculate the predicted state of the container, and thereby reduce the check to a 12-minute visual inspection for the majority of our reefers. This improves our equipment turn time and reduces CO2,” Rasmussen says.
The technology will expand over time to include new capabilities beyond temperature, power status, humidity and air supply/return air. The system does not currently monitor reefer gas content, but it does have the capability to monitor the product temperature. “We are constantly keeping our finger on the pulse to explore additional ways for RCM to create value to customers and products,” she says. “A natural next step is to further understand what there is a need for in the market.”
Cloud Technology Emerges
Mediterranean Shipping Company (MSC) and CMA CGM have recently invested in a cloud-based container monitoring system from Traxens that will include 4.5 million containers, representing nearly a quarter of the world’s ocean vessel containers. The company will retrofit existing containers with devices containing GPS and sensors that will relay data via cellular signals and their own proprietary mesh network.
Traxens says it will announce the deployment in the fourth quarter of this year.
“Our business model puts shipping lines at the center of deployment and shippers at the center of usage,” says Tim Baker, Traxens director of marketing and communications. “Shipping lines will soon order containers from the manufacturers requesting that they be delivered in the ‘smart’ version.”
Once the smart containers are in place, customers will access data through smartphones, web browsers, ERP and TMS systems. The data will include GPS coordinates, temperature, vibration, shocks, door openings, movement, internal temperature, humidity and air pressure.
“Users will have the option of buying data from these containers on a trip-by-trip/container-by-container basis,” says Baker. “Further down the road, we will have a simple web interface where any shipper can subscribe to data from any single container on a single trip. We have some interesting challenges to rise to before we get to that stage.”
In October 2015, the Traxens technology was implemented on some containers on board the Bougainville, CMA CGM’s flagship vessel. “With the technology, containers are able to communicate among themselves and to the ship’s communication infrastructure by using built-in relay antennas,” says Clara Guerin, press and digital communication assistant at CMA CGM. “At the moment, the technology gathers data about GPS position, temperature, shocks, vibration, internal temperature, humidity etc.; anything that can be measured can be potentially added to the list. All collected data are sent to CMA CGM headquarters via Traxens’ data centers.”
BlackBerrry Updates Intermodal Solution
BlackBerry Technology Solutions has developed an end-to-end, cellular-enabled, intermodal solution called BlackBerry Radar, connecting the device to a cloud-based infrastructure that supports the applications that a customer would use to monitor a fleet and its cargo. BlackBerry’s self-powered sensor captures temperature, humidity, door openings and motion. The solution can leverage available cellular infrastructure to track cargo. The device collects data almost 10 times more frequently than other solutions.
West refers to the standard reporting interval as “near-time data.” The system can also be programmed to provide alerts in real time, when an event is triggered. An example being when a temperature exceeds a certain threshold, an alarm is sent immediately.
BlackBerry is currently piloting tests, and it recently made the system available commercially. The business model will consist of purchasing the retrofittable device and paying for the monitoring service.
BlackBerry initially viewed carriers as its target customers, but the company has fielded a lot of interest from shippers. “We are seeing quite a diversity in customers wanting to explore this type of solution,” West says.
“Automating the recording of IOT cold chain data receiving ensures that temperatures are being maintained throughout the entire cold chain, thereby remaining compliant with FDA food safety standards,” says Kevin Beasley, chief information officer at VAI, a software provider. “IOT technology also ensures the integrity of the temperature in the cold chain. When you are shipping a product for example, if you included IOT technology, then your customers can receive the benefit of that data as well, and prove that you are shipment compliant.”
‘Intelligent Container Project’ Identifies Cold Transport Strategies
Container temperature monitoring can help minimize deviations in the quality of food products that cannot be avoided using existing technology. An ongoing project at the University of Bremen in Bremen, Germany, called “The Intelligent Container,” has demonstrated that enhanced monitoring can deliver insight into new strategies for transport and warehouse management.
For example, different harvest conditions, harvest-to-cooling time and deviating transport
temperatures can create variances in product quality. These deviations can be compensated for by intelligent stock rotation under the condition that the remaining shelf life is known for each item.
Measurements of supply and return air temperature, as provided by standard telematics units, are insufficient for predicting product temperatures and resulting quality deviations, according to a recent project update.
The “intelligent container,” however, can capture spatial temperature deviations via a network of 10 to 20 wireless sensor nodes. The nodes measure product temperature directly inside the packaging, and biological models calculate the effect of various deviations in environmental parameters on the product quality.
Gas sensors are able to monitor additional factors influencing quality. Ethylene gas, in particular, emits from the ripening process of several fruits.
The project verified results using case studies with bananas and different meat products. The case studies included temperature mapping for truck and container transport, development and “parameterization” of shelf life models, and test transport with the prototype “intelligent container.”
Possible decision points for implementing the “first expired, first out” principle were defined after an analysis of the supply chain.
Dr. Reiner Jedermann, a research associate at the university, says that two sub-projects launched in 2014 and 2015. The aim is to fine tune sensor components of the intelligent container and to explore new application fields. For example, the wireless anemometers (WAMs), which measure wind speed, have been redesigned to measure low air flow speed between pallets and packings. Currently, they are used to capture the air flow profile in cold storage rooms to develop better ventilation control and to reduce energy consumption.
“When the project is finished next year, we plan to apply the WAMs to measure airflow in containers as well and optimize stowage and packing,” says Jedermann.
The survey found that most companies (59 percent) use IoT for alarms and real-time monitoring rather than optimization and prediction. As an organization’s IoT strategy evolves, optimization and prediction play a greater role.