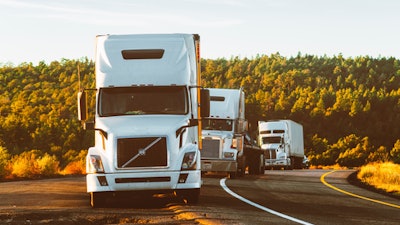
The current driver shortage couldn’t come at a worse time. On top of global supply chain issues, a number of reopenings and other events are putting a strain on resources already stretched thin. More restaurants are coming back online, schools are reopening, and of course, we’re headed into the holiday season, when consumers expect packed shelves and freezer cases to supply their holiday meals.
Given the crunch, the drivers we do have are often loaded with more hours, deliveries and stress, leading not only to mistakes, but also turnover, which only makes the problem worse. Adding to the challenge, nearly a quarter of the trucking workforce is expected to hit retirement in the next decade, which means this won’t be a short-term problem.
Fortunately, while the forecasts are dire, there’s also good news. You likely have untapped efficiencies in your routes, assets, scheduling and operations that could relieve some of the pressure and help you do more with less.
The key to finding these efficiencies is improving your visibility, which in turn can lead to greater efficiency and process improvements. Let’s look at three ways to find hidden efficiencies within your fleet to help ease the strain of driver shortages.
Know where your drivers are to plan more efficient routes
If you’re having trouble finding new drivers, look into how you can most efficiently route the drivers you do have. By finding more productive routes and avoiding delays, you can complete more deliveries in fewer days with the same number of drivers you have right now.
With real-time visibility into where drivers are and what they’re doing, you can plan ahead to move shipments faster. For example, if a driver takes a full trailer load from a vendor to a distribution center, they might drop that trailer before it’s received and head back to their home location — maybe it’s the end of their shift or they’ve reached their maximum active hours under Department of Transportation rules.
That’s inefficient for the driver, who is driving back without a shipment, and for asset utilization, since the trailer is left behind. By knowing where the driver will be and when they’ll arrive, you can make sure they return to their home location with another load, bringing the trailer back to its home location as well.
More visibility and planning can also help re-route drivers around accidents, flooding and other hazards that can leave them stranded in traffic and delay deliveries. By knowing where drivers are and when they’re expected to arrive, you can arrange assets and deliveries accordingly to maximize every driver’s time and output.
Keep an eye on assets to find more time
The efficiency of driver routes and asset utilization go hand in hand, and by better managing assets, you can make more timely and efficient deliveries without adding more drivers.
There are a number of attributes you should know about each asset, including what shipment it’s carrying, when the shipment was picked up and when it’s going to arrive at the distribution center. With the knowledge of where that asset is and when it will become available, you can start to plan when it can be utilized again.
If you don’t know when the asset will arrive, it’s hard to plan the next shipment, and a trailer that arrives mid-day might not be loaded again until the next morning. If you track that asset more closely, however, and know it will arrive mid-day, you can plan to load it and send it out on an afternoon route as well.
This kind of visibility also helps you avoid unscheduled downtime that might disrupt deliveries and leave available drivers without a trailer. If you know where a trailer will be, you can find gaps in schedules to keep up with maintenance and ensure the fleet runs efficiently. A better understanding of asset utilization ensures available drivers are most useful.
Get all teams on the same page to find force multipliers
To better utilize the drivers you have, you need strong communication across the organization. Often, different teams use different systems to keep track of assets, log inventory and manage drivers. Business operations, warehouse dispatchers, maintenance, even drivers themselves all have pieces of information that can help your organization complete deliveries more efficiently.
Gathering all the data from all different functions in one place for better visibility can act as a force multiplier that helps everyone make better decisions. Greater visibility into driver activity and asset utilization not only helps you more efficiently assign drivers, but also tells you a story about your warehouse activity, dispatchers, receiving schedules and more.
Those insights can help you save days by better aligning your operations. Any delay in delivering inventory can have a knock-on effect because if you’re past a cut-off, you’re not just losing a couple hours; you might lose a day or a couple days when you otherwise could have moved more inventory.
Aligning different functions to ensure timely deliveries not only keeps you running efficiently, but also can uncover new resources. If you have assets that don’t require a CDL, for example, being more efficient in receiving, dispatch and shipping processes might uncover resources in the business that could support driving in cases when a CDL is not required.
Look at the driver shortage as an opportunity
Like many organizations, you’ve had to do more with less throughout the pandemic, the supply chain crunch and the ongoing driver shortage. However, these constraints are also pushing businesses to find previously unknown efficiencies.
If you approach these challenges by gathering data and increasing visibility, you can not only meet your obligations despite the driver shortage, but also build more efficient and productive operations that will pay dividends for years to come.