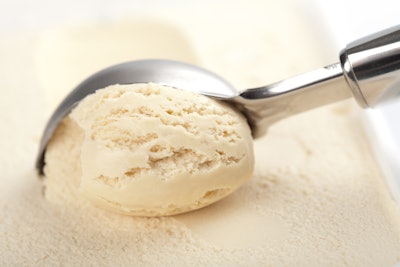
Background
Founded in 2012, Beyond Better Foods manufactures low-calorie, low-fat and low-sugar ice cream and snack products sold under the Enlightened brand. At any given time, 50 loads of Enlightened ice cream — roughly 2 million pints — are in transit from the company’s headquarters in New York City to major retailers across the United States.
“We are a growing brand, and product quality is one of our primary differentiators,” says Andy Kung, director of operations. “It’s critical that we know we are delivering the best product to our customers.
The challenge
Enlightened is more temperature-sensitive than standard ice cream, making temperature controls particularly crucial for ensuring a positive customer experience. The product’s optimum temperature range is -10 to -20°F. When temperatures rise above -10°F, the product loses its whipped fluffiness and shrinks. As a result, ice cream pints appear to be only three-quarters full. Without visibility to temperature conditions during transit, Beyond Better Foods risks product degradation and its brand reputation with every load of ice cream it shipped — particularly during the summer months.
Solution -- improved visibility for superior quality control
To gain greater control over product quality, Beyond Better Foods implemented Emerson Cargo Solutions’ GO Real-Time Trackers in November 2018. The units enable the company to track the location and monitor the temperatures of all in-transit shipments in real time. The trackers have proven indispensable, both for the intelligence they deliver and the convenience they provide.
Kung’s team can monitor the temperature on any shipment at any time using Emerson’s Oversight dashboard. In addition, the system alerts the team via email whenever temperatures stray from the optimum window. Armed with this data, Beyond Better Foods can monitor product quality and recall shipments exposed to temperature excursions during transit.
Moreover, the solution keeps the company’s fleet of carriers accountable by eliminating finger-pointing from the claims process.
“The peace of mind that we’ve gained has been an actual, tangible benefit,” says Kung. “Because we receive a flag any time there is a problem or a potential issue with temperature fluctuations, we can quickly assess and tackle it. That’s definitely worth the money spent.”
To streamline the cargo tracking process, Beyond Better Foods also partners with Emerson’s managed services team for every shipment. By shifting hours of manual processing time each month to Emerson, Kung and his team can re-focus their efforts on optimizing other aspects of production and warehouse operations.
Result -- data-driven decisions protect brand reputation — and profits
Before initiating the cargo tracking program with Emerson, customer complaints about product integrity exposed below-par shipping conditions after the fact. But, with Emerson Cargo Solutions’ GO Real-Time Trackers and Oversight portal, the company can get a jump on potential quality issues before products ever reach consumers.
In one instance, Beyond Better Foods needed to rush a truckload of Enlightened product to a new customer over the weekend for a scheduled product launch the following week. The timing of the shipment was critical and fell outside the range of its normal carrier network, requiring Beyond Better Foods to make arrangements with an untested third-party shipper. Although the product arrived on time and at the desired temperature, data reported by the shipment’s GO Real-Time Tracker revealed that conditions in the trailer rose well above 0°F during transit. Kung’s team was able to determine that roughly 48,000 pints of ice cream valued at $250,000 were damaged and pulled the shipment. Thankfully, Beyond Better Foods was able to send a replacement shipment and keep its new customer partnership intact.
“Considering that it was a new customer launch, we definitely didn’t want to provide product of compromised quality,” says Kung. “Thanks to Emerson, we were able to quickly schedule a second shipment. Even though it delayed the launch, the insights we gained enabled us to get the best product to our customer.”