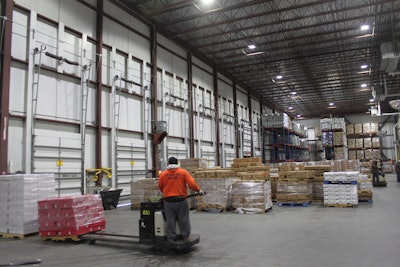
As the global cold chain expands, docking equipment that enables warehouse crews to maintain product temperatures is playing a bigger role. New cold storage facilities employ a variety of tools for managing temperature-controlled storage. These include high-speed doors, seals, vertical dock levelers, thermal walls and other tools.
When evaluating a dock environment, warehouse managers should evaluate the safety risks to workers, the need to maintain indoor temperatures from outside air, and how easily dock doors and levelers accommodate the load sizes the company manages.
Food safety considerations are also important. Dock seals separate areas where food is stored from the outside. Door seals on dock doors prevent outside air and contaminants that could harm the product.
Automated Doors Evolve
Automated doors, while more expensive than manual doors, better ensure temperature consistency.
Cheney Brothers, an Ocala, Fla.-based foodservice distributor, has deployed state-of-the-art automated doors in its 480,000-square-foot headquarters warehouse and 325,000-square-foot Riviera Beach, Fla. warehouse. The company is also building a 345,000-foot warehouse in Punta Gorda, Fla. The company ships to customers in the southeastern U.S., the Caribbean, Mexico and Latin America.
High-speed doors from Jackson, Wis.-based Rytec Corp. provide rapid storage and retrieval of product from the freezer and chilled storage rooms for Cheney Brothers, which operates 24 hours a day, six a days a week. The company maintains 38- to 40-degree F docks, with product going in and out of -5-degree F freezer storage and 34-degree F cooler rooms.
The company’s WMS system monitors the path of products, from the racking to the dock to the customer.
At the Ocala location, 26 forklifts and 105 pallet jacks roam warehouse the floor. Workers can access the 16-foot-tall door on the freezer in less than two seconds as it opens and closes at a speed of 100 inches per second.
The door’s speed ensures that it is not prone to forklift collisions. In the event of a collision, the door’s panels harmlessly release from their guides. Employees can then insert the panel back into the guides by simply opening and closing the door.
In the past, door damage required taking a door out of operation for repair. This was a problem because of the high volume of product. It also interfered with the company’s ability to provide emergency orders for restaurants or hotels that forgot to order something or ordered an inadequate quantity.
“We cannot afford to have a door down – ever,” says Danny Wells, senior director of engineering at Cheney Brothers.
The door speed plays a role in saving energy. The differential between the freezer and the dock is at least 43 degrees F. Conventional wisdom once dictated that freezer doorways called for heavy panel sliding doors to prevent heat transmission.
However, these solid panel doors would cause two problems. The slow speed could severely cripple product flow through the facility. Moreover, because the doors slide from side to side, they take up wall space equal to the doorway area. The facility needs all the wall space it can get for product racking for those 19,000 SKUs.
With an operation that sees thousands of cycles per day per door, heat transmission isn’t an issue because the door is rarely closed. Plus, the door’s high speed minimizes doorway exposure, reducing cold air infiltration out of the freezer.
When the door closes, it seals tightly. The door’s vertical edge becomes encased in the side guides to prevent cold air from escaping. Brush seals along the top of the panel, and a floor-hugging gasket, also prevent air release.
Cheney Brothers fine-tuned the system to further improve temperature control.
Eric Andrews, a company engineer, developed a zipper pocket along the bottom bar on the freezer doors. The bottom bar on freezer doorways can accumulate ice, and the pocket enables door contact along the floor. The zipper pocket facilitates the ability to easily clean the ice off of the bottom bar to keep it pliable. Rytec Corp. assisted Andrews in developing the zipper pocket.
The team also installed a Plexiglas window in the door’s side column to allow for easy inspection. This saved time and improved safety for performing periodic inspection of the door’s counterweight. Inspection previously required removing the vertical side guide that covered and protected the counterweight. For the 16-by-10-foot doors that provide access into the high-rack freezer, inspection meant bringing the scissors lift over to the door and lifting someone up to the top of the side column to remove the screw.
High-Speed Doors Cut Load On Refrigeration System
Chatham, N.J.-based Preferred Freezer Services (PFS) which operates 34 locations nationwide, utilizes insulated, high-speed doors for its freezers. By combining the use of these high-speed doors and a dehumidification system on the dock, PFS is seeing a significant reduction on the load to the refrigeration system and the working conditions on the dock.
One advancement of roll-up door design is in electronic control system. A Rytec design advancement is the development of the System 4 controller. The intelligent processor and variable frequency drive (VFD) are fully integrated at PFS. The system generates an energy efficient speed curve for smooth motion, soft starting and soft stopping.
The WMS enables the door to interface with the operation for up-to-the-second deliveries at the freezer doorways.
The WMS automatically signals the system open and close the doors on command and only as needed.
Visual Detection And Warning
Visual detection and warning systems are also improving safety and efficiency in food and beverage warehouses.
Ocean Spray Cranberries improved safety for lift truck operators at nine loading dock bays in its Tomah, Wis. facility while increasing efficiencies by installing a vehicle restraint and visualization warning system. The recently-installed Rite-Hite vehicle restraint and visualization warning system enables lift truck operators to see when it is safe to enter and exit a trailer. The system uses LED lights mounted directly in the forklift drive’s line of sight as they enter and depart the trailer.
The system provides status of the vehicle restraint, alerting the driver when the vehicle restraint has secured the trailer and it is safe to enter. The system has reduced the need for dock workers to chock wheels or check trailer status to unlock full trailers.
“Forklift drivers can get tunnel vision and not notice the lights on a standard control box,” says Troy Bergum, product manager of Rite-Hite Products Corp. “We bridge the communication gap.”
More recently Sartori, the Plymouth, Wis.-based cheesemaker, focused on improving the loading dock environment on account of the Food Safety and Modernization Act (FSMA).
According to FSMA, docks are a high-risk zone for food defense and facility security. To prevent theft, reduce contamination and improve dock worker safety, Sartori installed Rite-Hite’s latest automatic vehicle restraints – the SHR-5000 Shadow Hook Dok-Lok. This vehicle restraint wraps around a trailer’s rear-impact guard, securing the trailer to the loading dock. It reduces trailer separation accidents while deterring theft.
The strong connection between the trailer and the loading dock reduces holes, gaps, and other openings where dirt, debris, insects, and other environmental contaminants can enter the building. Vehicle restraints, along with Rite-Hite’s Dok-Commander controls panel, can interface with a company’s security system, as well.
Sartori deployed Rite-Hite’s vehicle restraints and vertical-storing leveler at the dock, and high-speed doors inside its facility. The vertical leveler allows the loading dock door to close directly onto the pit floor, rather than onto the leveler, which minimizes outside air infiltration and prevents contaminants from entering the building. The high-speed doors minimize temperature changes and air particulate contamination between the facility’s rooms.
Insulated Walls Play A Role
Flexible, modular walls are also finding application on loading docks.
Randall Manufacturing’s insulated curtain wall system, InsulWall, helps warehouses maximize space, protect inventory, conserve energy and move easily when business needs change. InsulWall provides temperature separation up to 40 degrees F (22 degrees C). It is constructed with recycled insulation making it a LEED contributing product. It is available in a variety of R values, thicknesses, and weights.
This flexible, thermal curtain wall installs easily from ceiling joists or roof decks and can be stationary or on roller track.
Kristine Grudis, Randall Manufacturing sales manager for warehouse products, says InsulWall’s thermal properties, flexibility, and modularity enable easy installation around the inside perimeter of a dock. In situations where certain areas have to maintain a temperature that is well below the outside temperature, compressors have to work overtime to maintain the inside temperature. This is highly energy intensive.
One foodservice distributor had to maintain dock temperature of 49 degrees Fahrenheight while the outside temperature on many days exceeded 100 degrees, Grudis notes.
The strip doors in the bays, which the company used to keep dirt, bugs and debris from entering the dock area, were not effective thermal barriers. To create an effective barrier, the company installed InsulWall inside the dock area on a roller track. Windows sewn within the InsulWall kept the dock area bright and safe.
When the trucks arrived, the warehouse workers rolled back the InsulWall from the bay door and closed the door. The InsulWall helped maintain the temperature on the dock while the rest of the building remained cool. For the first time, the compressors were clicking off between 2:30 and 3 p.m. daily, which reduced electricity use.
The InsulWall achieves three goals: 1) maintain dock temperature and product integrity, 2) conserve energy, and 3) ease the toll of excessive heat and humidity on the compressors.
Dock Levelers Boost Efficiency
Vertical storing hydraulic dock levelers are a fairly new development for improving warehouse efficiency, says Tim Bauer, director of industrial architecture at Ryan Companies, the Minneapolis, Minn.-based builder, designer and real estate management firm. Vertical storing levelers are more efficient energy-wise and protect the door from damage and allow “drive through” door design where the operator can control the trailer door.
An extended lip chamfer – a beveled edge connecting two surfaces – provides a smooth transition from the trailer bed to the dock leveler. A smooth transition between loading dock and trailer reduces jolts to forklift operators, thereby minimizing product and equipment damage. The overhead door closes all the way to the pit floor, providing better environmental control over temperature and humidity extremes.
New food safety regulations are encouraging food warehouse managers to take a closer look at docking equipment. Warehouse managers have a host of automated systems to choose from.
Flexible Conveyors Enable Truck Loading And Unloading
Flexible Material Handling (FMH) Conveyors, based in Suwanee, Ga., offers flexible, gravity,-powered, telescopic and rigid-belted conveyor systems for truck loading and unloading. FMH designs each conveyor to expand, contract and flex as needed.
FMH’s Nestaflex two-stage, gravity expandable conveyor specifically designed for truck loading. The 10-inch, steel frame and the 18-inch tires, coupled with a 1.5HP drive system make the TL-2 easy to use and long lasting.
The MAXX rigid, extendable belt conveyors are available in telescopic, drive-out multi- and single -stage booms. They can be used for high-volume, automated shipping and receiving applications. Users can automate loading and unloading areas and convey a variety of products from large to small cartons. A VFD-controlled belt drive system provides transitions from belt starts and stops at speeds up to 250fpm. Each telescopic conveyor also includes a VFD-controlled extension drive providing smooth operation when extending and retracting the conveyor.
For More Information:
FMH, fmhconveyors.com
Preferred Freezer Services, www.preferredfreezer.com
Randall Manufacturing, www.randallmfg.com
Rite Hite Products Corp., www.ritehite.com
Ryan Companies, www.ryancompanies.com
Rytec Corp., www.rytecdoors.com