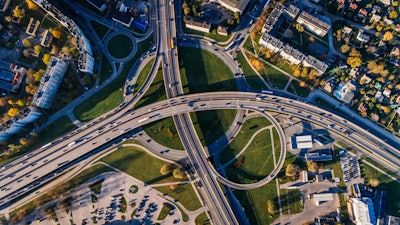
The Coronavirus disease (COVID-19) pandemic, ongoing labor disputes and global economic volatility have all contributed to supply chain disruption, and ocean freight shipping has been a key contributor to the problem. McKinsey identified that between the first quarter of 2020 and the last quarter of 2021, average container schedule delays doubled globally and increased by 600% on the Far East and North America trade lanes. Additionally, since 2019, average global container shipping rates have increased by 4-5 times. As critical as these factors are to the problem, one of the most significant contributors to the disruption predates the pandemic and is easier to fix.
Poor utilization of available carrier capacity is a systemic, industry-wide issue. Outdated communication, data sharing and collaboration practices diminish shippers’ ability to move freight efficiently or improve contract utilization. The reliance on manual, time-intensive processes often results in information being out of date, hampering shippers from taking action. In addition, human error is commonplace, further devaluing the information. To solve the problem, shippers and carriers need to modernize their approach to managing available capacity through a combination of technology and updated processes.
Modernizing outdated processes
With so much uncertainty, shippers acknowledge they urgently require more visibility to optimize carrier allocation. Despite the need, nearly 75% of supply chain functions still rely on static spreadsheets and Bills of Lading (BOLs) to manage allocation. In order to minimize further disruption and improve agility, shippers must accelerate the adoption of technology. Modern approaches to managing allocation improve visibility for shippers, allowing them to adapt and adjust as things change.
No one can predict or be immune to all of industry’s challenges. However, shippers can take proactive steps to mitigate the risk of further disruption and make on-time delivery a differentiator and competitive advantage rather than a constant battle.
- Share information and communicate. Companies who use modern approaches and maintain relationships with their data sources for more efficient data sharing will have a competitive advantage over those who stick to traditional practices and are forced to make changes reactively instead of proactively. Currently, shippers spend multiple hours a week managing their allocation as they receive data from multiple sources in various formats. Shippers need access to cross-platform, real-time analytics to have an accurate view and determine capacity and proper carrier allocation. This visibility allows shippers to see which carrier bookings might be in trouble before it’s too late to make a change of plans and avoid delays.
- Streamline data collection and processing. Manually managing data leaves many opportunities for error such as data accuracy and version control issues. This legacy approach slows down analysis leaving shippers with data too old to be valuable when a quick pivot is required. Automating data collection and analysis is vital to give shippers the agility to navigate and adapt to the constantly changing landscape. Instead of relying on static data, shippers need a more dynamic approach that provides data in real time so that they can more accurately forecast their allocation needs and make rapid adjustments to mitigate disruption.
- Standardize processes to prevent misallocated shipments. Key metrics, terminology and planning periods often vary from carrier to carrier, which presents challenges for shippers trying to align capacity with demand. Working collaboratively with carriers to determine common operating procedures improves efficiency and minimizes miscommunication due to inconsistent methodologies. Standardizing these processes saves shippers money when they no longer have to scramble to get inventory to the correct ports, carry excess inventory or book backup carrier options to compensate for unanticipated delays outside of their control.
The majority of shippers recognize that the only constant in the industry is uncertainty and need to take steps to modernize many of the processes and procedures they have relied on. By updating communication methods, sharing information efficiently and modernizing data practices, they are better positioned to manage the inevitable disruption.
The challenging carrier allocation environment isn’t going to disappear overnight. Consumer demand continues to fluctuate, economies are under pressure, and supply chain challenges take time and collaboration of many key players to resolve. Adapting to the environment as it exists today with an eye toward the future is an opportunity for shippers to stand out in a competitive retail environment.
Those brands that fail to embrace the modernization imperative run the risk of encountering more issues that will impact their bottom line and reputation. Delayed shipments lead to dissatisfied customers who are more likely to switch allegiance to a competitor. Shippers looking to thrive this holiday season must turn to technology and embrace the latest allocation management practices to avoid encountering more issues. Unlike many of the challenges they face, allocation management is one problem that they can solve.