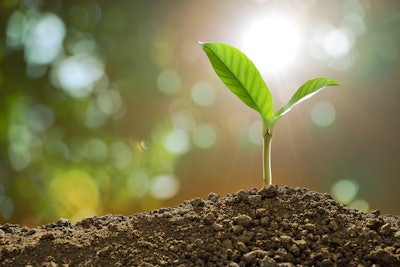
Currently, about 98% of the nation’s lettuce is trucked from California and Arizona, contributing to spoiled produce, food waste and rising transportation emissions. California continuously faces major droughts, and soil erosion is a problem plaguing farmers nationwide. As a result, traditional farming is increasingly unsustainable. This system is energy and water-intensive and results in growing lettuce in a dry, desert environment using unsustainable groundwater to irrigate and cross-country shipping by truck.
Furthermore, one truckload of lettuce coming from the West Coast results in over 10,000 pounds of greenhouse gases being emitted into the atmosphere. There are thousands and thousands of trucks per year bringing leafy greens to East Coast markets, and hundreds of hours are being spent planning the logistics of food distribution. For example, it is a 3,200-mile trek to ship to New England with flavor and freshness being lost by the mile.
However, the introduction of technologically advanced hydroponic greenhouse growing systems is disrupting the long-standing business practice of growing and trucking the nation’s greens thousands of miles across the country. This growing method brings year-round sustainable farming to the East Coast with a smaller carbon footprint.
Hydroponic production, growing without soil, naturally protects increasingly stressed topsoil that is vulnerable to soil erosion, an increasing problem in agriculture today. This precise, soil-less method utilizes up to 90% less water than field-grown greens to grow crunchy, flavorful lettuce. Greenhouse-grown lettuce can also be produced with 100% captured rainwater and almost 95% natural sunlight through special high-light transmission glad windows. Clean natural gas is burned to heat greenhouses and capturing the CO2 and releasing it back into the greenhouse makes the process net neutral. Solar panels also generate about 20-30% of electricity.
Hydroponic growing is also safer because the lettuce does not come into contact with contaminates that field-grown lettuce is subjected to from livestock, and the lettuce is not handled by human hands. It is also grown free of chlorine, other chemical washing agents and harmful chemical residues.
By making sustainability a core focus, each subset of operations is already greatly more sustainable than industry norms, including the supply chain. Transportation and logistics also play a critical role in product quality, supply chain efficiency and sustainability efforts.
One of the main factors driving lettuce quality is age-post-harvest. By growing produce hydroponically, locally grown lettuce is delivered within 24 hours, providing consumers with a fresher product that is transported in more a sustainable, climate-friendly way. A 24-hour delivery window means end customers are eating lettuce two to 12 days after harvest whereas West Coast greens are, at best, 10 days old but usually the lettuce is around 13-25 days after harvest.
Temperature control is also critical. Drivers must be devoted to preventing disruptions in the cold chain. To ensure that the lettuce does not freeze or get warm, drivers oversee product delivery all the way from the greenhouse facility’s 35°C cooler to customers’ distribution center 35°C coolers.
Optimizing distribution channels requires a lot of diligence and extensive planning to balance the workload of drivers and solve timing equations. However, once a rhythm is established, week-to-week there is a similar trucking plan to the previous week with some variations for customers that require additional freight.
To make transport more efficient, each truck makes four to eight stops on average per day and deliveries are kept with a 50- to 80-mile radius or 1.5-hour drive whereas field-grown lettuce is typically traveling 2,750 or more miles. Combining multiple customer stops into a single delivery run also enables massive delivery efficiencies and minimizes unnecessary stops and the use of additional trucking.
Local deliveries with multiple stops mean fewer road miles and increasing the number of customer pickups results in cost-savings for customers and better utilization of their internal fleets. A more localized approach to lettuce logistics also enables drivers to have consistent, local runs. In an industry dominated by long-haul freight carriers, hydroponic growing allows drivers to make it home to their families for dinner every night.
As demand for hydroponically grown produce increases, the exponential growth framework also drives changes in the supply chain. To keep pace with demand, as well as production and facility expansion plans, the number of tractor-trailer units will also need to grow. During this growth in units, electric-powered trucks and trailers will become more commonplace by 2025 due to societal and market shifts. This transition to electric vehicles furthers sustainability efforts and reduces the carbon footprint of logistics operations.
To provide consumers with high-quality, fresh produce, hydroponic growing systems have emerged as an important alternative to traditional agriculture. Year-round, local lettuce also leads to a more efficient and sustainable supply chain. Delivering lettuce within 24 hours reduces the carbon footprint of logistics and maximizes the product quality metric for consumers.