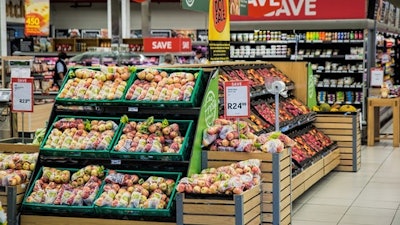
Will the food we want be on shelves? Will it cost more than we’re used to paying? Will we be limited in the quantity we can purchase? These are questions consumers have become accustomed to asking since the beginning of the Coronavirus disease (COVID-19) pandemic. As consumers, we’re familiar with food supply chain challenges because of the direct impact it has on our lives.
COVID-19 upended food supply chains by disrupting the flow of food from farms and producers to consumers. The stresses of the pandemic created bottlenecks in labor, processing, transport, sourcing and logistics – in addition to major shifts in demand.
While factors such as changing consumer preferences, trade conditions, technological advances and shifting social patterns were already impacting food supply chains, the pandemic exacerbated them.
Various ways the pandemic caused disruptions
There has been an ongoing labor shortage issue in the U.S. agricultural industry since before the pandemic. From 2002-2014, for instance, the number of field and crop workers in America declined by 146,000. It makes sense then that one of the most pressing pandemic-related challenges for the food industry was the availability of workers – for farm and food production sites alike. With value chains that are highly dependent on migrant workers, travel restrictions, tighter border controls and general virus fears made it difficult for farmers to get the help they needed when they needed it.
Travel restrictions and tight border controls also impacted the movement of products along the supply chain. Air freight restrictions in particular made the transport of food very difficult and expensive. During the week of May 10-16, global air cargo capacity was 26% lower than during the same period last year. This primarily caused disruptions for perishable products with a high value-to-weight ratio (such as fruits and vegetables), which are most often transported by passenger planes.
Another factor that contributed to food supply chain disruption was the scaling down – or in some cases, shutting down – of processing plants. Packing plants for fruits and vegetables, as well as meat processing facilities, are confined spaces that make it difficult to respect social distancing requirements. For this reason, many firms reported high rates of worker absences and even when workers could socially distance, the efficiency of operations was greatly reduced.
Finally, food manufacturers limiting the production of certain types of food, as well as shifting consumer purchasing patterns, made sourcing more difficult to predict and adjust.
Reconfiguring food supply chains for future resilience
As the food industry continues to streamline operations in ever-changing market conditions, there is an opportunity to redesign supply chains. Farmers, producers, distributors, retailers and consumer packaged goods companies will need to navigate fluctuating conditions for some time, and having the right tools and technology in place can provide future resilience.
First and foremost, businesses need end-to-end supply chain management to enhance visibility and collaboration among stakeholders. In the food and beverage industry specifically, companies are dealing with mass amounts of non-standardized data, which impedes efforts to create transparency through the value chain. To standardize and prevent inconsistencies with data, organizations must eliminate siloes that are causing data to be missing, incomplete or to exist in multiple places across disparate systems. Taking these steps will also support the digitization of the supply chain to create increased transparency and new opportunities for innovation.
The significant, negative impact of labor shortage on the food supply chain should also be a wakeup call for businesses. Moving forward, procurement leaders must ensure that contingent work is a part of their larger business strategy. It’s critical that companies have the ability to find temporary work quickly – during a crisis or otherwise – to ensure business continuity.
Lastly, businesses must establish partnerships with multiple manufacturing centers and have multiple supply chains, with the ability to coordinate operations seamlessly between them. By having access to several different sources of supply, businesses instantly become more agile and better equipped to pivot if one supplier is facing challenges.
Embrace innovation, diversification and collaboration
Now is the time to prepare for the next crisis – whether it’s a meat shortage, food recall or another pandemic.
But, being truly prepared takes more than planning – it requires new technologies, processes and entire ways of thinking. Businesses must use the momentum of change from the outbreak to embrace innovation, diversification and collaboration. Those who do will develop stronger supplier relationships and supply networks that are resilient and able to withstand future risk.